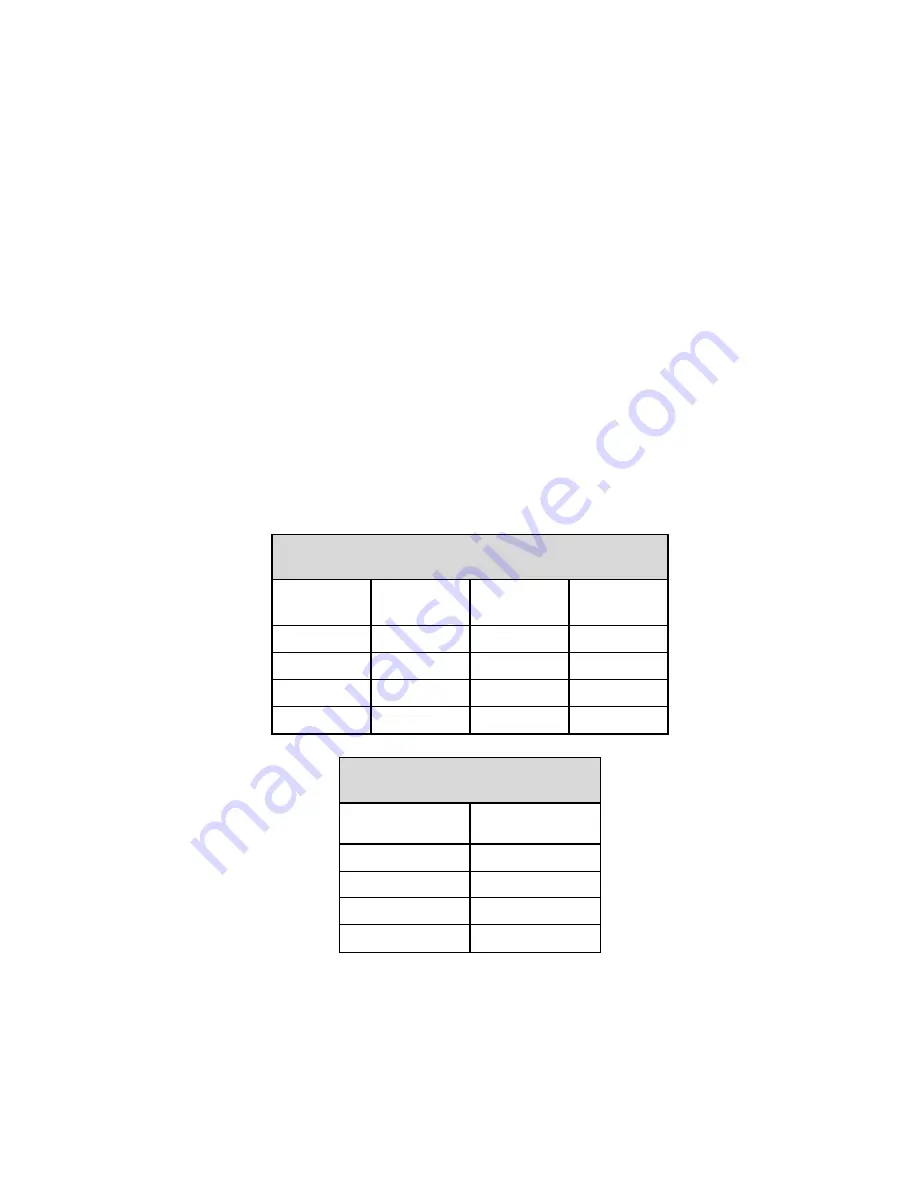
DEKKER Vacuum Technologies, Inc. – HullVac / September 2016
24
Clean the area and replace the pipe plug with a grease fitting (as generally they are not equipped with a grease
fitting). Remove the grease drain plug, located at the lower portion of each motor face (typically a plastic plug),
and loosen any hardened grease that may block the drain. Add the recommended volume of the previously
described grease using a hand operated grease gun. Run the motor for 2 hours. Replace the pipe plug in grease
drain.
Mixing of lubricants is not recommended due to possible incompatibility. One of two things may happen if
incompatible greases are mixed: (1) the mixture could harden and not release any of the oil; (2) the mixture
could soften, releasing all of the oil. When changing lubricants, be sure to grease and then re-grease after 100
hours of service.
Frequency/volume of greasing is based on service conditions, speed and frame size. See the Motor Bearing
Lubrication Schedule table below.
Standard conditions:
8 hour day operation, normal or light loading, clean environment at a 100ºF maximum
ambient temperature.
Severe conditions:
24 hour operation or shock loading, vibration, dirty or dusty environment.
Extreme conditions:
heavy shock, vibration, or dust. See the
Motor Bearing Lubrication Schedule
table
below for lubricating details.
Motor Bearing Lubrication Schedule
Lubrication Frequency – Ball Bearings
Roller bearings - divide time by 2
NEMA
Frame
Standard
Conditions
Severe
Conditions
Extreme
Conditions
182-215
3 years
1 year
6 months
254-365
2 years
6-12 months
3 months
404-449
1 year
6 months
1-3 months
ALL
6 months
3 months
1 month
Lubrication Volume
NEMA
Frame
Volume
(Cubic Inches)
182-215
0.5
254-286
1
324-365
1.5
404-449
2.5