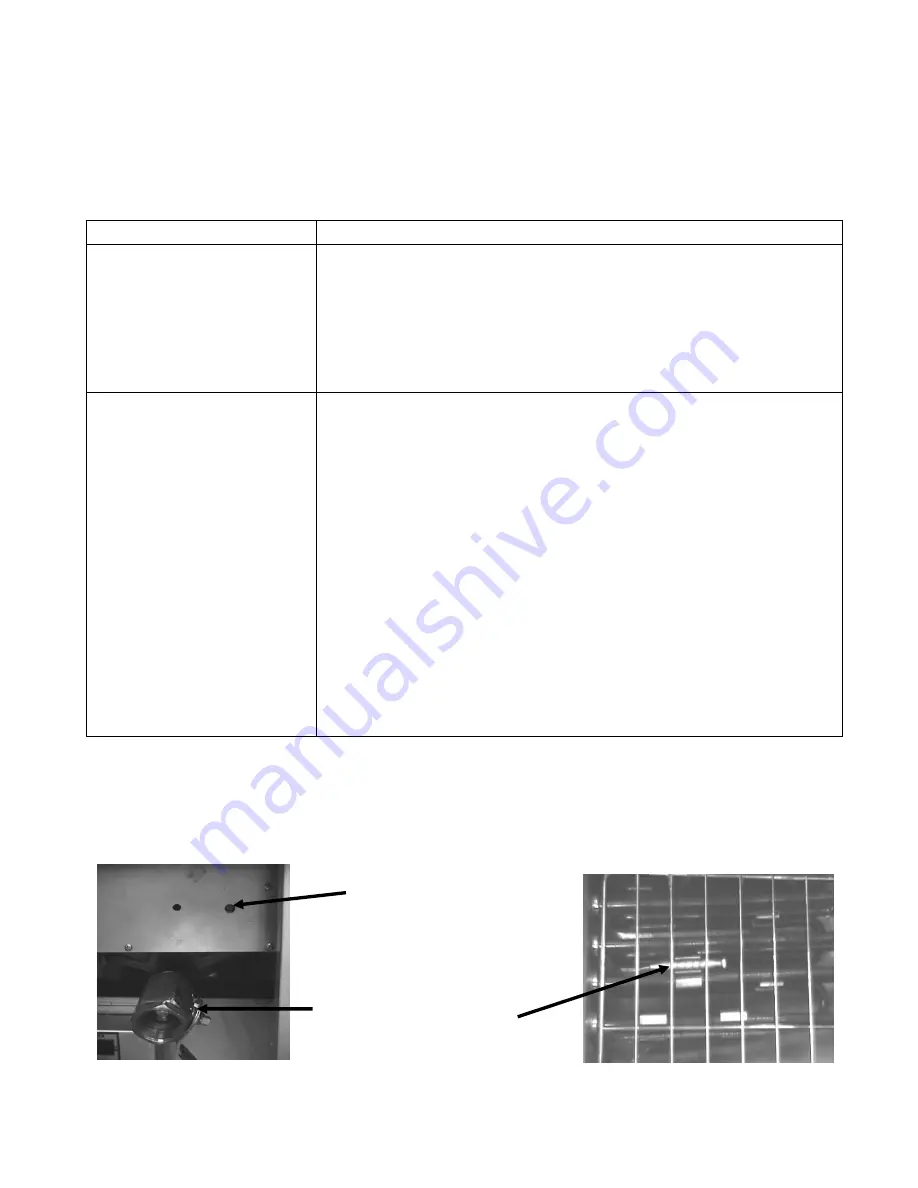
14
6.
TROUBLESHOOTING GUIDE
The problems and possible solutions given below cover those most commonly encountered by
operators.
FOR DETAILED TROUBLESHOOTING AND SERVICE-RELATED INFORMATION, CALL
THE DEAN SERVICE HOTLINE AT 1-800-551-8633 (USA/Canada only) or 1-318-865-1711.
PROBLEM CORRECTIVE
ACTION
Operator hears click sound
when the temperature
controller dial is turned but
vessel remains cold. No
evidence that elements are
warming the vessel.
With the power switch “ON”:
1.
Manually reset the high temperature limit switch (push red button
on the panel above the drain valve). See Figure 6-1.
2.
Check for tripped branch or main circuit breakers or blown fuses.
Poor temperature control
on the cold side or hot side;
excessive warm-up time;
temperature recovery is
slow or inadequate when
vessel is loaded; uneven
heating; excessive
temperature overshooting
during warm-up; scorching;
overheating; or high limit
switch must be reset often.
Check thermostat adjustment:
1.
Check that the thermostat bulb/probe in the vessel has not been
knocked loose from its operating position. It should be clamped
to the second element with 1,5 mm (1/16 inch) spacing. See
Figure 6-2.
2.
Place the sensing bulb of a high quality immersion thermometer
about 38 mm (1-1/2 inches) above the thermostat sensing bulb
and set the temperature controller dial to 177°C (350°F).
3.
Wait at least 30 minutes for the oil temperature to stabilize.
4.
If temperature is not /- 5°C (10°F) of the dial setting, call
service for a new operating thermostat/temperature controller.
High Limit
Reset Switch
Sensing Bulb in
Fryer Vessel
Drain
Valve
Figure 6-1
Figure 6-2