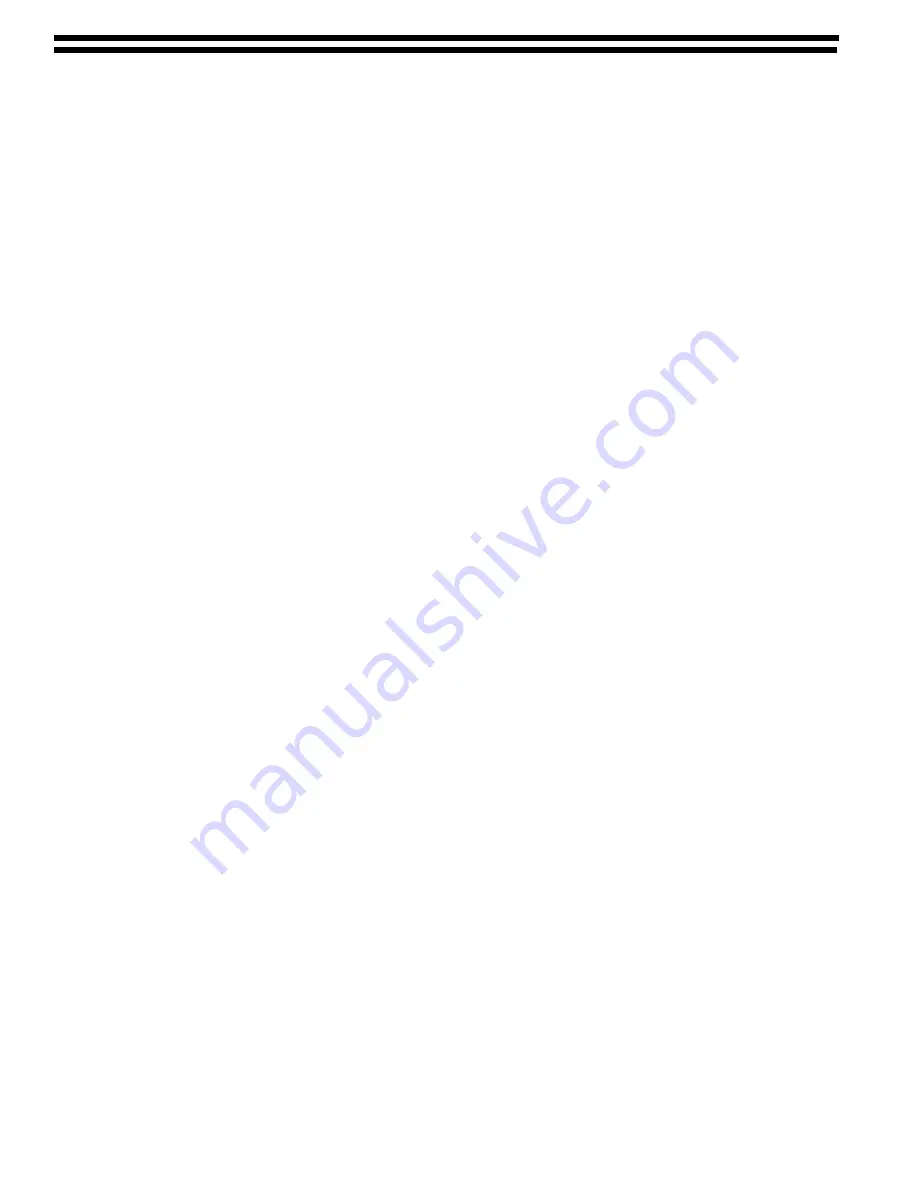
100.6015.10
- 12 -
4 SERVICE
Preventative maintenance kits for each of the assemblies are available from the factory. Each kit contains all
the parts and detailed instructions that are required for complete maintenance. All o-rings and gaskets that
have been disturbed during the disassembly must be replaced during reassembly in order to insure safe,
trouble free operation. Failure to replace these parts could result in a shortened operation period and bodily
injury.
Refer to Figures 4, 5, and 6
4.1
Cleaning the Flowmeter Assembly
4.1.1 Use a coin or washer as a screwdriver and loosen the bottom meter inlet plug while holding the
flowmeter assembly to make sure it does not drop out. It may be necessary to use pliers if the plug
has not been removed for some time.
4.1.2 Loosen the plug about three (3) turns and remove the meter assembly. (Push up and out on the
flowmeter to remove).
4.1.3 Bend a paper clip or wire and pull out the ball stops on each end of the glass tube. DO NOT LOSE
THE METERING BALL.
4.1.4 Clean the inside of the glass tube with a pipe cleaner or bottle brush using wood alcohol, and rinse
thoroughly with warm water.
4.1.5 Clean the metering ball using wood alcohol, and rinse thoroughly with warm water.
4.1.6 Thoroughly dry the glass metering tube. Reassemble the metering stops and ball.
4.1.7 Reinstall the meter assembly by tightening the meter inlet plug making sure that it is on center with
the top and bottom gasket.
NOTE: The meter gaskets can usually be reused. Turn the gaskets over for best results.
4.2
Rate Valve Cleaning
4.2.1 Unscrew the rate valve plug from the valve bonnet.
4.2.2 Remove the valve bonnet from the top of the front body.
4.2.3 Clean the parts by immersing in alcohol or soapy water, rinse, and dry thoroughly with a clean cloth.
4.2.4 The o-rings on the valve bonnet may need replacing if scratched or bruised.
4.2.5 Examine the valve sleeve for nicks or any marks. The sleeve may be removed for this purpose. Use
caution to avoid marking the surfaces.
4.2.6 The o-ring on the outside of the valve sleeve usually may not require replacing.
4.2.7 Inspect the rate valve hole in the meter housing and clean with a damp cloth if necessary. DO NOT
use any sharp tools that may scratch the internal surface. Never use any solvent for cleaning the
plastic, as it will deteriorate rapidly. Wood alcohol can, however, be used successfully.
4.2.8 Apply a thin film of fluorolube grease to o-rings and slide the valve sleeve into the top body.
4.2.9 Replace rate valve.
Summary of Contents for 200 Series
Page 6: ...100 6015 10 6 Figure 1 100 PPD 2 kg h Meter Panel ...
Page 7: ... 7 100 6015 10 Figure 2 200 PPD 4 kg h Meter Panel ...
Page 9: ... 9 100 6015 10 Figure 4 100 PPD 2 kg h Meter Panel Components ...
Page 10: ...100 6015 10 10 Figure 5 250 PPD Max 4 kg h Meter Panel Components ...
Page 11: ... 11 100 6015 10 Figure 6 300 6 kg h 500 PPD 10 kg h Meter Panel Components ...