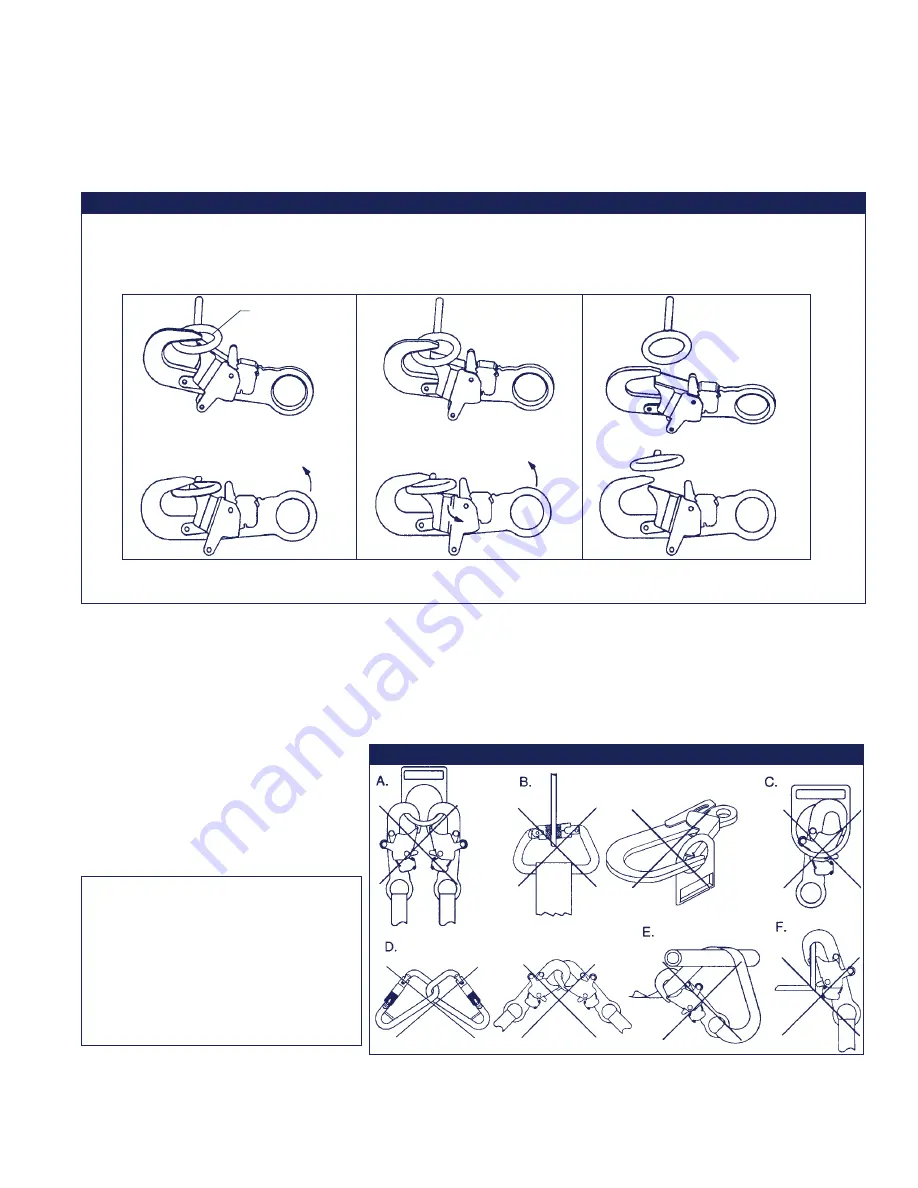
3
mechanisms to inadvertently open regardless of how they become oriented. Contact DBI/SALA if you have any
questions about compatibility.
Connectors (hooks, carabiners, and D-rings) must be capable of supporting at least 5,000 lbs. (22kN). Connectors
must be compatible with the anchorage or other system components. Do not use equipment that is not compatible.
Non-compatible connectors may unintentionally disengage. See Figure 3. Connectors must be compatible in size,
shape, and strength. Self locking snap hooks and carabiners are required by ANSI Z359.1 and OSHA.
2.3
MAKING CONNECTIONS: Only use self-locking snap hooks and carabiners with this equipment. Only use
connectors that are suitable to each application. Ensure all connections are compatible in size, shape and
strength. Do not use equipment that is not compatible. Ensure all connectors are fully closed and locked.
DBI/SALA connectors (snap hooks and carabiners) are designed to be used only as specified in each product’s
user’s instructions. See Figure 4 for inappropriate connections. DBI/SALA snap hooks and carabiners should not
be connected:
A. To a D-ring to which another
connector is attached.
B. In a manner that would result in
a load on the gate.
NOTE: Large throat opening snap hooks
should not be connected to standard size
D-rings or similar objects which will result
in a load on the gate if the hook or D-ring
twists or rotates. Large throat snap hooks
are designed for use on fixed structural
elements such as rebar or cross members
that are not shaped in a way that can
capture the gate of the hook.
C. In a false engagement, where features that protrude from the snap hook or carabiner catch on the anchor and
without visual confirmation seems to be fully engaged to the anchor point.
D. To each other.
If the connecting element that a snap hook (shown) or carabiner attaches to is undersized or irregular in
shape, a situation could occur where the connecting element applies a force to the gate of the snap hook or
carabiner. This force may cause the gate (of either a self-locking or a non-locking snap hook) to open, allowing
the snap hook or carabiner to disengage from the connecting point.
1. Force is applied to the
snap hook.
2. The gate presses against
the connecting ring.
3. The gate opens allowing the
snap hook to slip off.
Figure 3 - Unintentional Disengagement (Roll-out)
Small ring or other
non-compatibly
shaped element
Figure 4 - Inappropriate Connections