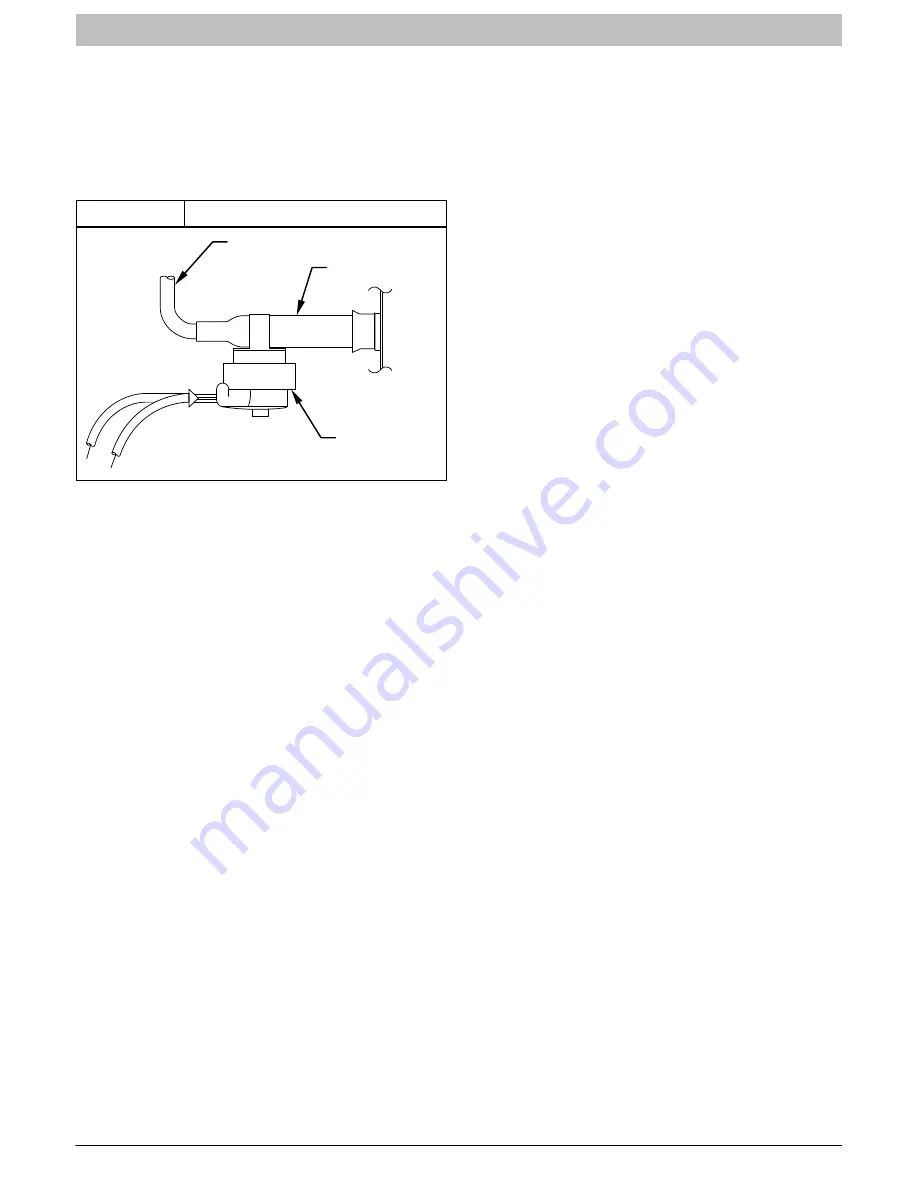
INSTALLATION INSTRUCTIONS
R
−
410A Split System Heat Pump
428 01 5302 00
11
DEFROST SYSTEM
A. DEFROST THERMOSTAT
The defrost thermostat is factory installed on a short tube
stub extending from the coil end plate. Refer to Figure 11
and confirm that the thermostat is securely fastened in
place on the tube stub.
Figure 11
Defrost Thermostat
FEEDER TUBE
TUBE STUB
DEFROST
THERMOSTAT
COIL
B. DEFROST CONTROL BOARD
The defrost board is a time/temperature control which
includes a field
−
selectable time period between defrost
cycles of 30, 60, or 90 minutes (quick
−
connects located
at board edge, factory set at 60 minutes).
Defrost mode is identical to cooling mode except that
outdoor
−
fan motor stops and second
−
stage heat is
turned on to continue warming conditioned space.
Initially, the defrost cycle timer starts when the contactor
is energized and a 24 VAC signal is present on the T1
terminal. Then the defrost cycle begins when the defrost
thermostat is closed and the cycle timer times out (30, 60,
90 or minutes).
There are two
timers
involved in the defrost sequence:
Interval Timer
– 30, 60, or 90 minutes, selected by
setting the jumper on the defrost board. Timer is only
active during calls for heating. Timer starts when the
defrost thermostat closes 32
°
F (0
°C
). Timer stops when
a defrost is initiated by the defrost board or when the
defrost thermostat opens 65
°
F (18
°
C).
Defrost Timer
– 10 minutes, not adjustable. Timer is only
active while the coil is defrosting. Timer starts when the
defrost board initiates a defrost. Timer stops when the
defrost thermostat opens 65
°
F (18
°
C) or after timing out
at 10 minutes (whichever comes first).
SPEEDUP
pins are provided on the defrost board to help
in troubleshooting without waiting for timers to expire.
Jumpering the SPEEDUP pins causes any active timer to
run very fast (256 times normal speed). Jumpering the
SPEEDUP pins does not by itself initiate any timers, it
only affects timers that are already running or are already
part of the sequence.
To initiate a forced defrost cycle (test cycle), the defrost
thermostat (Figure 11) must be closed.
There are two ways to verify that the defrost thermostat
is closed:
1. Jumper across the DFT terminals on the defrost
board (Figure 12). With this method, the defrost
thermostat is removed from the circuit, and operation
of the defrost thermostat itself will not be observed.
Skip to #3.
2. Use a volt-meter to confirm there is no voltage across
the DFT leads. 24 volts across the SFT terminals
indicates an OPEN defrost thermostat. Zero volts
across the DFT terminals indicates a CLOSED defrost
thermostat.
With this method, the operation of the defrost
thermostat can be observed during the test. If the
defrost thermostat is confirmed closed, skip to #3.
If the defrost thermostat is open (24 volts across DFT
leads) it may be possible to close the defrost thermostat
by forcing a frost buildup on the outdoor coil. Follow
these steps:
S
Turn off power to unit.
S
Disconnect outdoor fan-motor lead from OF2 on
control board (Figure 12). Tape lead to prevent
grounding.
S
Restart unit in heating mode; wait for
accumulation of frost on outdoor coil. Use
volt-meter to confirm there are zero volts across
the DFT leads (thermostat closed).
S
Turn off power to unit. Replace outdoor fan-motor
lead to OF2 on control board (Figure 12). Restart
the unit in heating mode.
3. With unit running in heating mode and the defrost
thermostat closed, the entire defrost sequence can
be sped up for testing by shorting together the
SPEEDUP pins on the defrost board. Use a
flat-headed screwdriver to short the pins together.
4. Hold the SPEEDUP pins shorted together until the
reversing valve shifts.
SPEEDUP reduces whatever time was left on the
interval timer (30/60/90 minutes). In normal operation
the reversing valve will always shift with the SPEEDUP
pins shorted for between 1 and 21 seconds.
5. After shorting the SPEEDUP pins together as
described in #4, the reversing valve will energize
(shift to AC mode), the outdoor fan will stop, the strip
heat will energize, and the coil will begin to defrost.
There are two options for the defrost test:
a. Remove the short from between the SPEEDUP
pins immediately after the reversing valve shifts,
and the unit will defrost for a shortened period of
time (something less than 10 minutes). The
defrost will stop when the defrost thermostat
opens (reaches 65
°
F)(18
°
C) or when the defrost
timer times out (something less than 10 minutes).
b. Leave the SPEEDUP pins shorted together for
more than 2 seconds after the reversing valve
shifts, and the unit will immediately return to
heating operation (#6 below). Continue to leave
the pins shorted together and the sequence
starts over at #4 above.
6. Unit returns to heating mode after defrost sequence.
Reversing valve shifts back, outdoor fan starts up,
and strip heat de-energizes.