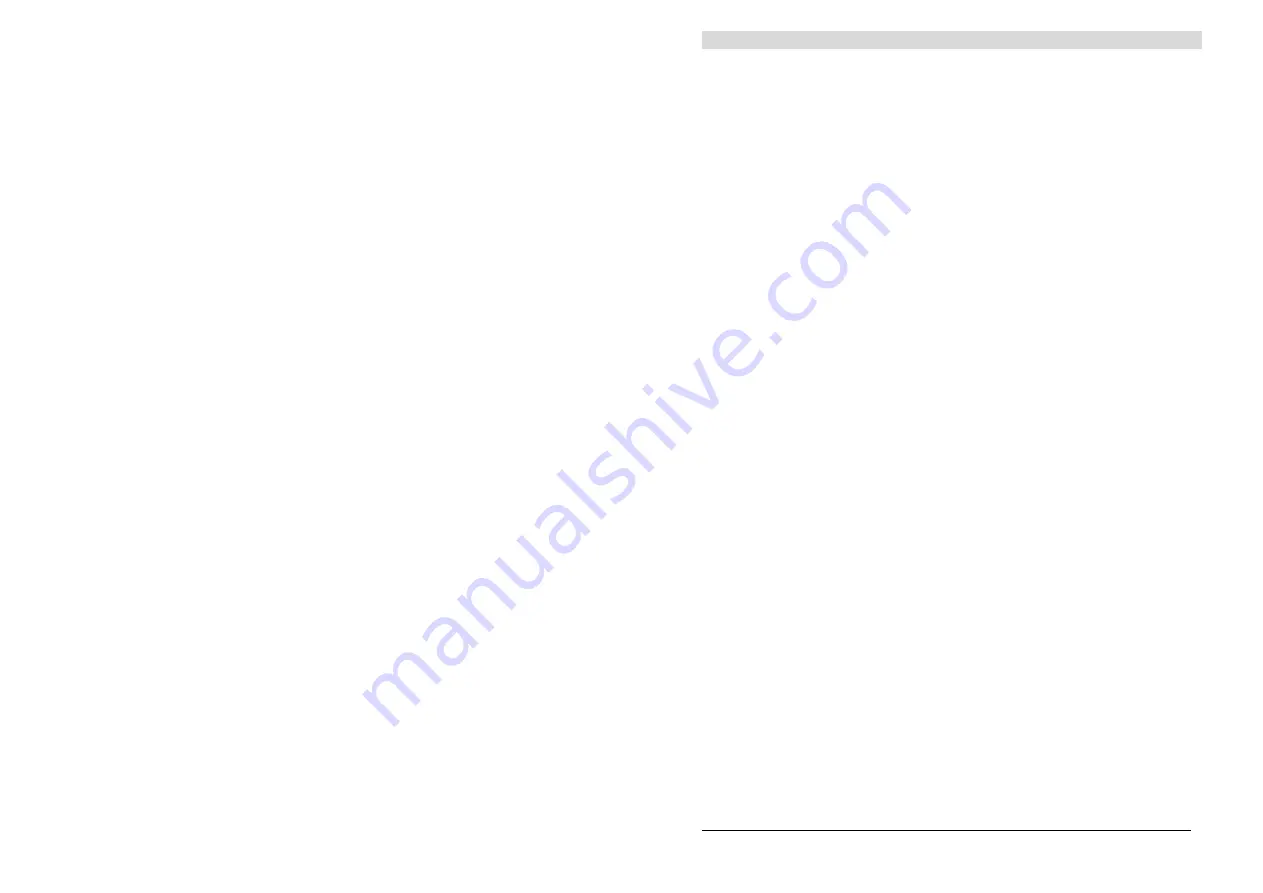
BWS-T2 Series
Instructions manual
4
EN 811: Oktober 1992
Safety of machinery - Safety distances to prevent danger zones being
reached
by the lower limbs
EN 999: Januar 1995
Safety of machinery - The positioning of protective equipment in respect
of approach of parts of the human body
EN 954 Part 1: März 1997
Safety of machinery; Safety related parts of control systems
- General principles for design
EN 60204 Part 1 Safety of machinery, electrical equipment of
machines - General requirements
Draft prEN 1050: Aprl 1996
Safety of machinery; risk assesment
FINAL DRAFT IEC 61496-1/Ed. 1.0: Safety of machinery - electro -
sensitive equipment,
Part 1: General requirements and tests.
Documents 44/206/FDIS and 44/206A/FDIS: 1997-03-28
FINAL DRAFT IEC 61496-2/Ed. 1.0: Safety of machinery - electro -
sensitive equipment,
Part 2: Particular requirements for equipment using active
opto-electronic
protective
devices.
Documents 44/208/FDIS and 44/206A/FDIS: 1997-0530
The BWS-T2 can be used in conjunction with our line of photoelectric
sensors as shown in the Technical Specifications.
The BWS-T2 has been designed so that one (1) or two (2) Emitter-Receiver
pairs can be connected to it.
The operating voltage is: 24VDC
±
10%.
The status of the system is indicated by 3 visible LEDs:
•
FREE
green
•
ALARM
red
•
TEST
yellow