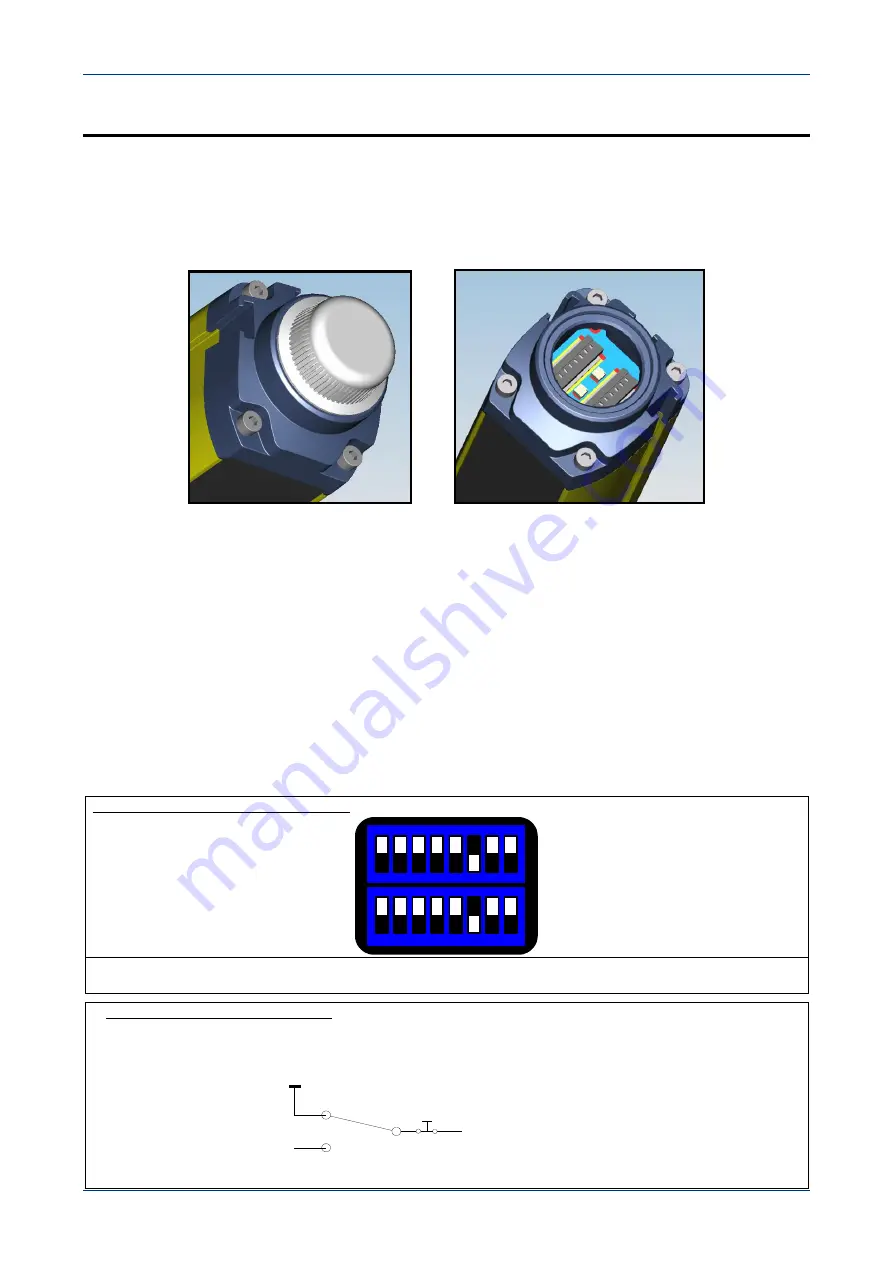
SG BODY REFLECTOR MUTING
25
5 ELECTRICAL CONNECTIONS AND CONFIGURATION
All electrical connections to the emitting and receiving units are made through male M12 connectors, located
on the lower part of the two units.
For active unit M12 12-poles and a M12 5-poles connectors are used.
A closing cap coupled with the top cap of the RX unit can be unscrewed to access dip-switches slot. By
means of internal dip-switches the user can set-up some functions, as described in paragraph 5.5.
Figure 29
5.1 IMPORTANT NOTES FOR INSTALLATION
For the correct functioning of the SG BODY series safety light curtains, the following precautions regarding
the electrical connections have to be respected:
•
Do not place connection cables in contact with or near high-voltage cables and/or cable
undergoing high current variations (e.g. motor power supplies, inverters, etc.);
•
Do not connect in the same multi-pole cable the OSSD wires of different light curtains;
•
The device is already equipped with internal overvoltage and overcurrent suppression
devices. The use of other external components is not recommended.
5.2 MINIMAL CONNECTION
Dip switches configuration:
EDM disabled
1
2
3
4
5
6
7
8
1
2
3
4
5
6
7
8
Dip switches n°1,2,3,4,5,7,8: ON
Dip switches n°6: OFF
Wires configuration:
automatic restart
Power supply: 0V, 24V
+24Vdc
0V
RESET/RESTART/RESTART MODE
line
NC
OTHER lines: floating
Summary of Contents for SG4-RB2-050-OO-N
Page 1: ......
Page 3: ......
Page 7: ......
Page 73: ...66 SG4 RB2 3L SG4 RDB2 3L ...
Page 74: ...SG BODY REFLECTOR MUTING 67 SG4 RB2 3T SG4 RDB2 3T ...
Page 91: ...84 ACTIVE PASSIVE ...
Page 92: ...SG BODY REFLECTOR MUTING 85 ACTIVE PASSIVE ...
Page 95: ...88 ...