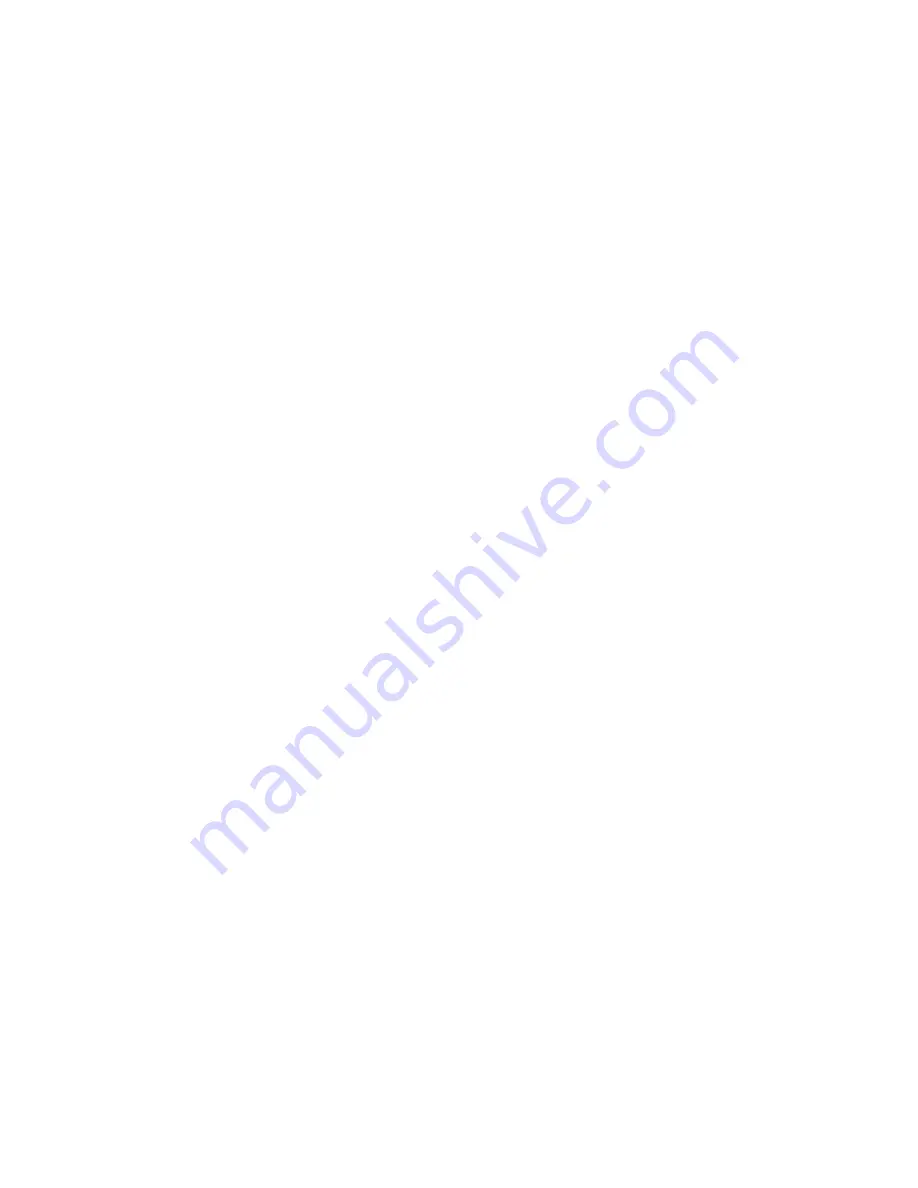
DS6100
DATALOGIC
2.16 - Installation
2.5.1 Power Supply
The supply voltage for correct operation of the scanner must be between 10
and 30 VDC.
The max. power consumption is 10 W.
The power block (optional), supplies the power necessary for the DS6100
and allows mains power to be used.
A security system allows the laser to activate only once the motor has
reached the correct rotational speed; consequently, the laser beam is
generated after a slight delay from the power on of the scanner.
2.5.2 Main Serial Interface
The main serial interface is compatible with the following electrical standards:
RS232
RS485 full-duplex
RS485 half-duplex
20 mA current loop
The 20 mA Current Loop interface is available if the optional INT-26
accessory is installed. This accessory interface replaces the RS232/RS485
selections.
The main serial interface type and its relative parameters (baud rate,
data bits, etc.) are selected via software either using the WinHost utility
program or Host Mode programming. For more details refer to the
section "Main Interface Menu" in the WinHost Help On Line.
Details regarding the connections and use of the main interface selection are
given in the next paragraphs.