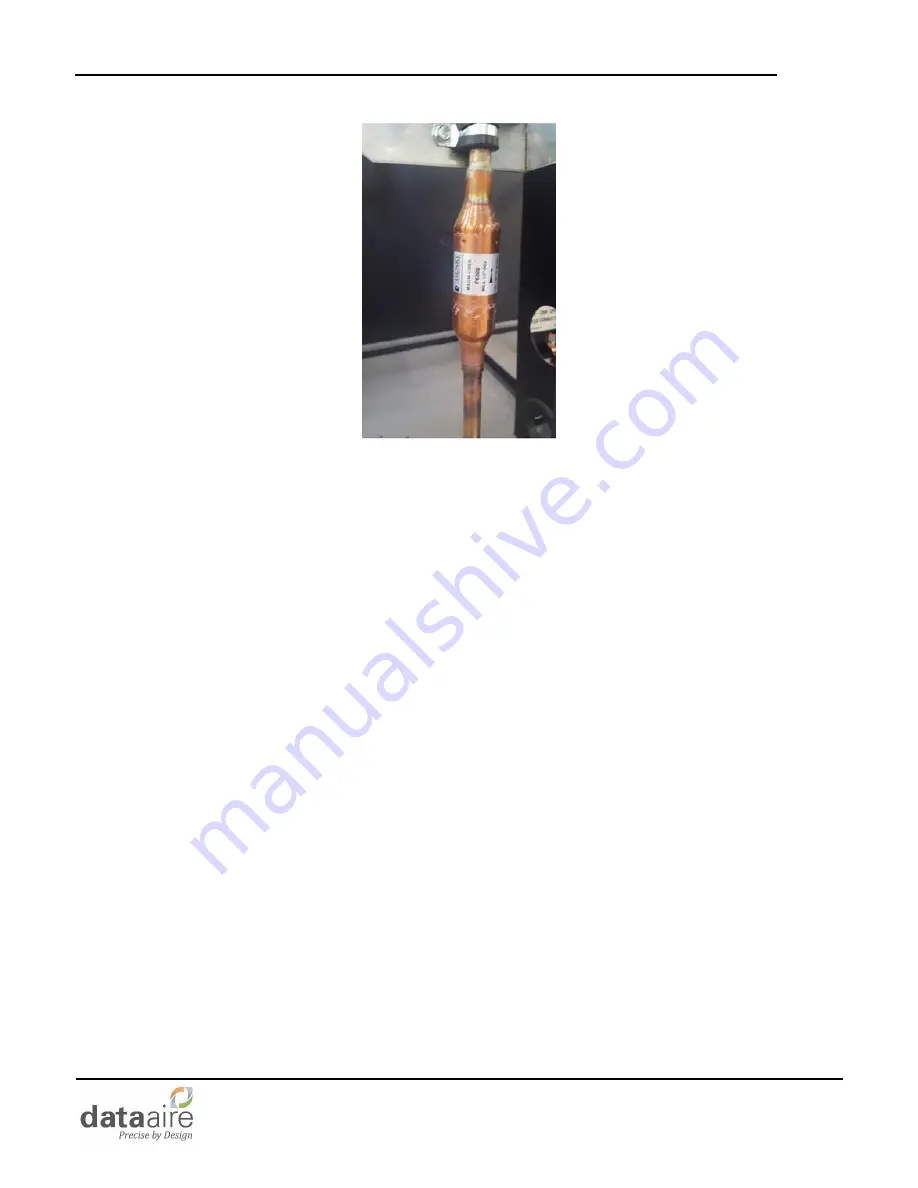
Installation, Operation and Maintenance Manual
Page
16
of
100
Figure 4 - Typical Discharge Line Check Valve
Note: Figure 4 - Typical Discharge Line Check Valve is only intended to show an example of a common check valve.
This picture may not represent your specific unit, check valve size, location or orientation.
Discharge line pressure should not exceed 9 PSI for R-410A. Recommended gas velocity for proper oil return is 1,000
FPM. Slope horizontal lines downward in the direction of the refrigerant flow (1/2” for every ten feet of line length).
Discharge lines do not require insulation but due to the high temperatures of the refrigerant inside the line, the
pipes may be insulated to protect against burns to individuals near or around the lines. They should be insulated if
the heat dissipated is objectionable or to prevent injury from high-temperature surfaces. In the latter case, it is not
essential to provide insulation with a tight vapor seal because moisture condensation is not a problem unless the
line is located outside.
External field piping must be supported within 18” of the inlet and outlet connections.
3.2.2
Liquid Lines
Liquid line size is determined by the recommended allowable pressure drop and velocity. The liquid line pressure
drop is 9 PSI for R-410A. The recommended liquid velocity should be below 300 FPM. To avoid excessive liquid line
pressure drop, the air-cooled condenser should be located above or at the same level as the evaporator. Condenser
installation more than fifteen (15) feet below the evaporator is not recommended. Insulation of liquid lines is not
required but can be useful in preventing condensation from forming and to avoid flashing on long pipe runs.
Although the liquid line ordinarily does not require insulation, the liquid line should be insulated to minimize heat
gain when it passes through a warmer area.
3.2.3
Line Traps:
Line traps assist with vertical oil travel and proper oil return. In a gaseous state, the refrigerant is a poor carrier of
oil therefore oil will begin to fall back down with vertical rises greater than 20 feet therefore, discharge line trapping
is required.
•
Discharge (hot gas) Line Traps:
1.
Traps must be installed by the installing contractor on the vertical rise of the discharge line.