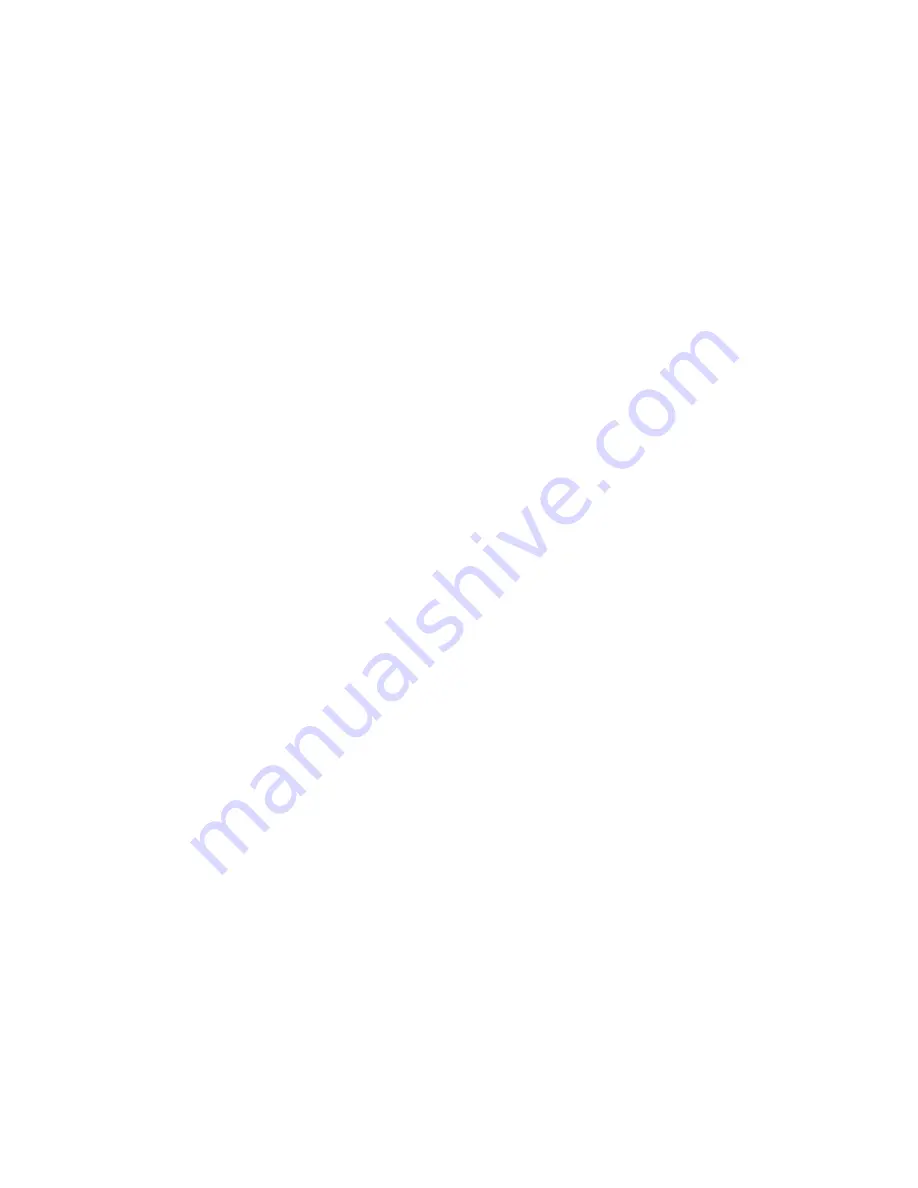
13
Parameter-Selection Mode can be entered by simply pressing and holding the Enter button down for
three seconds. Once in Parameter-Selection Mode, the far left of the display will be a ‘P’. The right
side of the display will indicate the currently selected parameter number for editing purposes. Pressing
the Up or Down button will increase or decrease the selected parameter number on the display.
Although the parameter numbers are in numerical order, some numbers are skipped. These numbers
represent reserved parameters that are not yet implemented and are not displayed. Once the desired
parameter number is displayed, a press of the Enter button will change the display to the Value Mode.
When in Parameter-Selection Mode, pressing the Enter button with parameter 0 selected will
cause the unit to return to Running Mode.
Example displays for Parameter-Selection Mode are P
1, P 13, and P 54. See the Software Parameters for a list of available parameters.
Value Mode is used to modify the value of the selected parameter. When in Value Mode, the two dots
which form the colon, between digits two and three, will alternately flash (one, then the other) to inform
the user that a parameter’s value is being edited. Pressing the Up or Down button increases or
decreases the selected parameter’s value. See the Software Parameters for a list of allowable values
and ranges. Value changes take effect immediately. For example, when scrolling through the alarm
output conditions, the relay will activate as the always-active selection is passed. Once the desired
value is showing in the display window, pressing the Enter button again will return to Parameter-
Selection Mode. The new value is not saved in permanent memory until the Enter button is pressed.
Removing power from the unit while in Value Mode may result in the specified new value being lost.
Detailed Configuration Instructions
Default Configuration
When shipped from the factory, the following basic settings are in place:
Rate Mode Operation in RPM
S1 and S2 Signal Input Pulses per Revolution: 1
Decimal Point Display: Off
Display Range: 0 - 2400
Speed Range: 0 - 2400 RPM
Accel and Decel: 2500 RPM per second
Signal Input 2 (S2) Mode: Jog @ 1000 RPM when Low
User Input 1 (UIN1) Mode: Emergency Stop when Low
Alarm Output: Disabled
Resetting the Unit to Factory Defaults
The factory-default settings can be easily restored using either of two methods. Both methods require
the Program Enable jumper to be in the “On” position. The first is to apply power to the unit with both
the Enter and Down buttons pressed for 3 seconds. The second is to change the value of parameter
95 to 5.
JP1 (Program Enable Jumper)
The JP1 jumper is located under the dust cover on the back end of the upper board. When the jumper
is set to the "Off" position, all programming features are locked out to the front panel user. When the
jumper is in the "On" position, the programming parameters are open to change. JP1 is shipped from
the factory set in the "On" position.