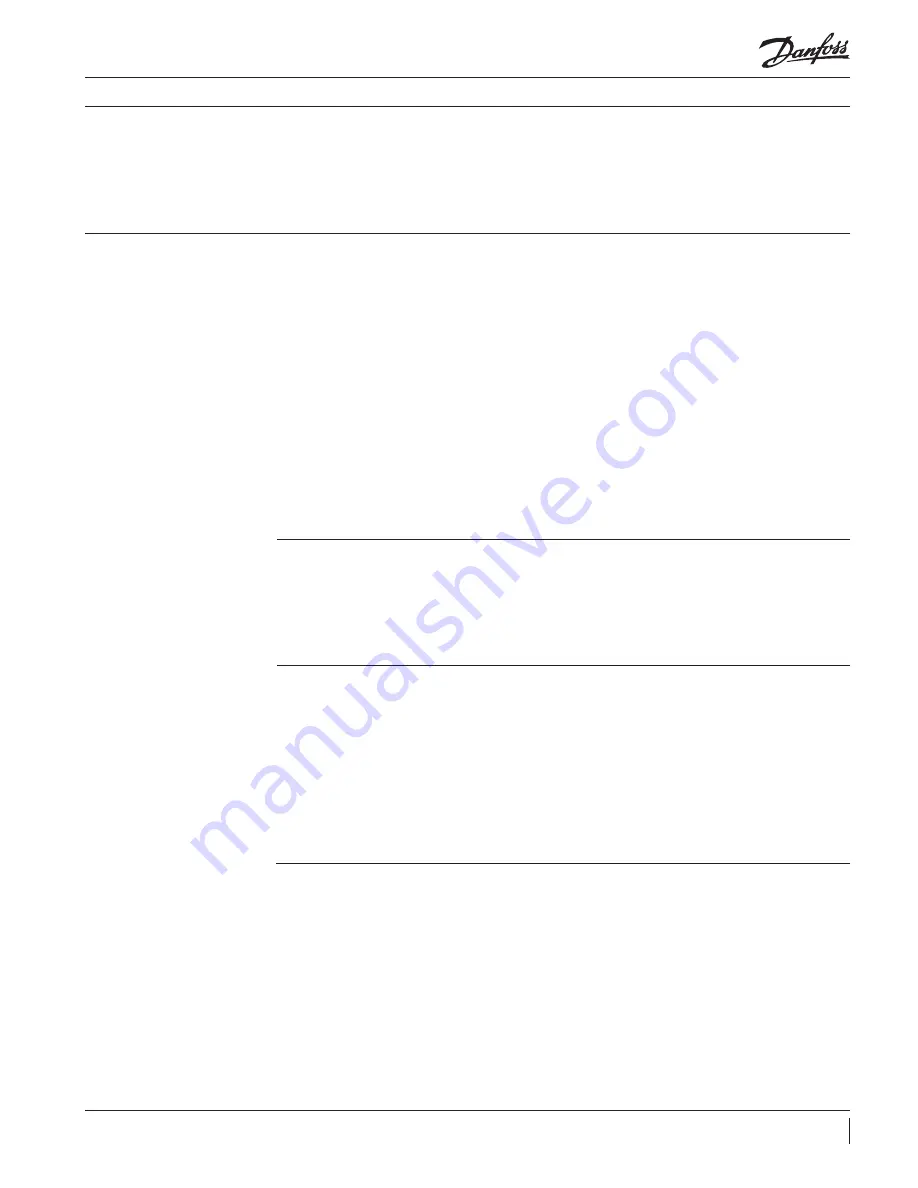
Application guidelines
41
FRCC.PC.014.A4.22
Specific application recommendations
Discharge line and
reversing valve
Defrost and reverse cycle
Suction line accumulator
Water utilizing systems
The VSH scroll compressor is a high volumet-
ric machine and, as such, can rapidly build up
pressure in the discharge line if gas in the line
becomes obstructed even for a very short period
of time which situation may occur with slow-act-
ing, reversing valves in heat pumps. Discharge
pressures exceeding the operating envelope may
result in nuisance high-pressure switch cutouts
and can generate excessive load on bearings and
motor.
To prevent such occurrences, it is important
that a 39.4 ft minimum discharge line length be
allowed between the compressor discharge port
and the reversing valve or any other restriction.
This gives sufficient free volume for the discharge
gas to collect and to reduce the pressure peak
during the time it takes for the valve to change
position. At the same time, it is important that
the selection and sizing of the reversing or 4-way
valve ensure that the valve switches quickly
enough to prevent against too high discharge
pressure and nuisance high-pressure cutouts.
Check with the valve manufacturer for optimal
sizing and recommended mounting positions.
It is strongly recommended to reduce the com-
pressor speed to 30Hz before the 4-way valve is
moved from a position to another.
Refer also to high and low pressure protection.
After the 4-way valve is moved to defrost posi-
tion, and in order to shorten the defrost period,
the compressor speed can be maintained at 70Hz
during the defrost period.
When the compressor is started again, after
defrost, it will run at 30Hz for a 10 seconds period.
After this period it is recommended to maintain
the speed at 50Hz for 10 to 15 seconds. Thus to
avoid excessive liquid refrigerant to come back to
the compressor sump.
The use of a suction line accumulator is strongly
recommended in reversible-cycle applications.
This because of the possibility of a substantial
quantity of liquid refrigerant remaining in the
evaporator, which acts as a condenser during the
heating cycle.
This liquid refrigerant can then return to the
compressor, either flooding the sump with refrig-
erant or as a dynamic liquid slug when the cycle
switches back to a defrost cycle or to normal
cooling operations.
Sustained and repeated liquid slugging and
floodback can seriously impair the oil’s ability to
lubricate the compressor bearings. This situation
can be observed in wet climates where it is nec-
essary to frequently defrost the outdoor coil in
an air source heat pump. In such cases a suction
accumulator becomes mandatory.
Apart from residual moisture in the system after
commissioning, water could also enter the re-
frigeration circuit during operation. Water in the
system shall always be avoided. Not only because
it can shortly lead to electrical failure, sludge in
sump and corrosion but in particular because it
can cause serious safety risks.
Common causes for water leaks are corrosion and
freezing.
Corrosion
: Materials in the system shall be
compliant with water and protected against
corrosion.
Freezing
: When water freezes into ice its volume
expands which can damage heat exchanger walls
and cause leaks. During off periods water inside
heat exchangers could start freezing when am-
bient temperature is lower than 32°F. During on
periods ice banking could occur when the circuit
is running continuously at too low load. Both
situations should be avoided by connecting a
pressure and thermostat switch in the safety line.
sive temperatures. Operating the compressor at
too high discharge temperatures can result in
mechanical damage to the compressor as well as
thermal degradation of the compressor lubricat-
ing oil and a lack of sufficient lubrication.
Refer to section “Discharge gas temperature pro-
tection” function for frequency converter settings
and accessories availability.