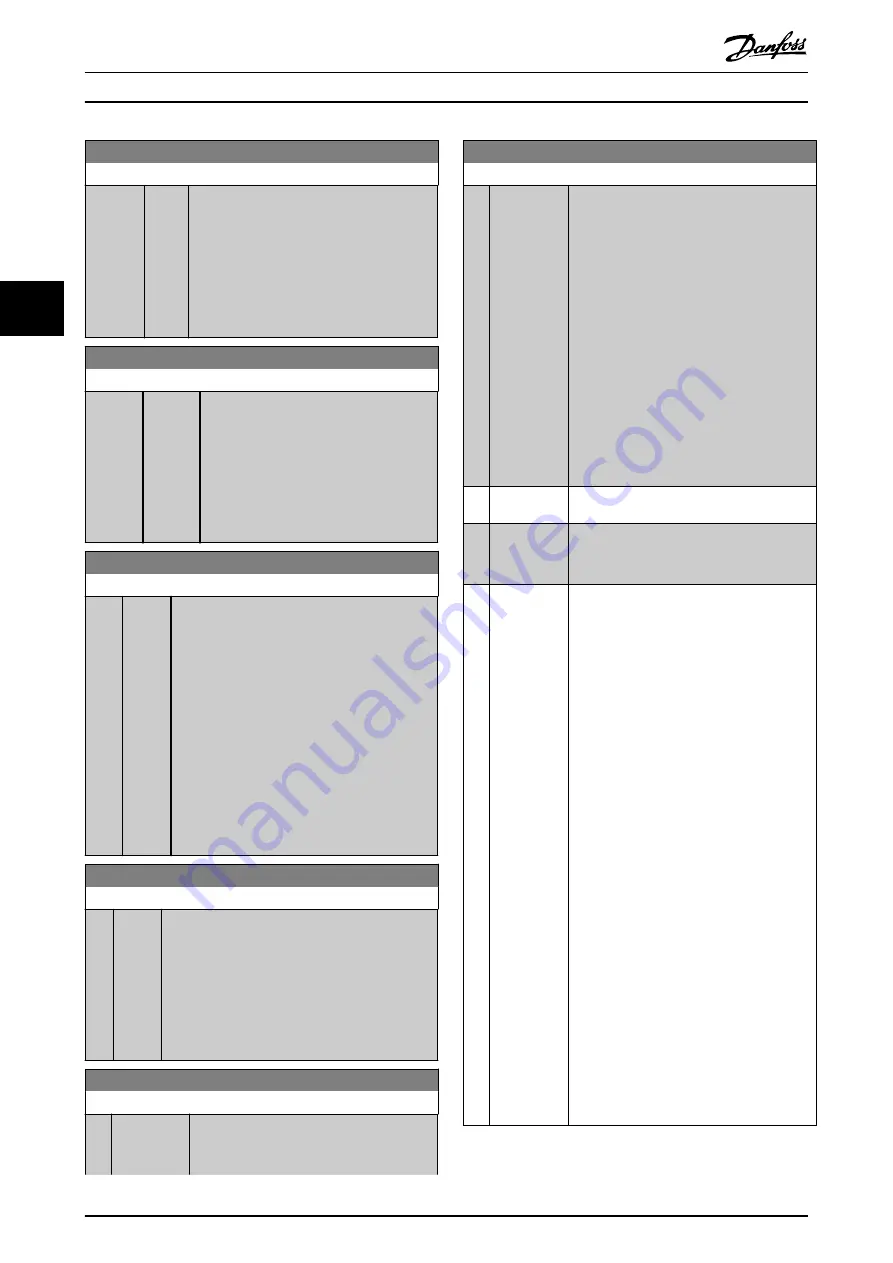
1-75 Start Speed [Hz]
Range:
Function:
Size
related
*
[ 0 -
10 Hz]
This parameter can be used for hoist
applications (cone rotor). Set a motor start
speed. After the start signal, the output speed
leaps to the set value. Set the start function
in
parameter 1-72 Start Function
to
[3] Start
speed cw
,
[4] Horizontal operation
, or
[5] VVC
+
clockwise
, and set a start delay time in
.
1-76 Start Current
Range:
Function:
Size
related
*
[ 0 -
10000 A]
Some motors, for example cone rotor
motors, need extra current/starting speed
to disengage the rotor. To obtain this boost,
set the required current in this parameter.
Set
parameter 1-72 Start Function
to
[3] Start
speed cw
or
[4] Horizontal operation
, and set
a start delay time in
.
1-78 Compressor Start Max Speed [Hz]
Range:
Function:
0 Hz
*
[ 0 -
650 Hz]
This parameter enables high starting torque. This
function ignores current limit and torque limit
during start of the motor. The time from the start
signal is given until the speed exceeds the speed
set in this parameter becomes a start zone. In
the start zone, the current limit and motoric
torque limit are set to the maximum possible
value for the frequency converter/motor
combination. The time without protection from
the current limit and torque limit must not
exceed the value set in
parameter 1-79 Compressor Start Max Time to Trip
.
Otherwise, the frequency converter trips with
alarm 18, Start Failed
.
1-79 Compressor Start Max Time to Trip
Range:
Function:
5 s
*
[0 -
10 s]
The time from the start signal is given until the
speed exceeds the speed set in
parameter 1-78 Compressor Start Max Speed [Hz]
must not exceed the time set in this parameter.
Otherwise, the frequency converter trips with
alarm
18, Start Failed
. Any time set in
for use of a start function must be executed
within the time limit.
1-80 Function at Stop
Option:
Function:
Select the frequency converter function after
a stop command or after the speed is
ramped down to the settings in
1-80 Function at Stop
Option:
Function:
parameter 1-82 Min Speed for Function at Stop
[Hz]
.
Available selections depend on the setting in
parameter 1-10 Motor Construction
.
•
[0] Asynchron
.
-
[0] Coast
.
-
[1] DC hold
.
-
[2] Motor check, warning
.
-
[6] Motor check, alarm
.
•
[1] PM, non-salient SPM, non Sat
.
•
[2] PM, salient IPM, non Sat
.
•
[3] PM, salient IPM, Sat
.
-
[0] Coast
.
[0]
*
Coast
Leaves the motor in free mode.
[1] DC hold /
Motor
Preheat
Energizes the motor with a DC hold current
(see
parameter 2-00 DC Hold/Motor Preheat
[3] Pre-
magnetizing
Builds up a magnetic field while the motor is
stopped. This allows the motor to produce
torque quickly at commands (asynchronous
motors only). This premagnetizing function
does not help the very first start command.
Two different solutions are available to pre-
magnetize the machine for the first start
command:
1.
Start the frequency converter with a
0 RPM reference and wait 2 to 4
rotor time constants (see the
equation below) before increasing
the speed reference.
2.
2a
Set
to the premagnetize
time (2–4 rotor time
constants).
2b
Set
parameter 1-72 Start
Function
to
[0] DC hold
.
3.
Set the DC-hold current magnitude
(
to be equal to I
pre-
mag
= U
nom
/(1.73 x Xh).
Sample rotor time constants=
(Xh+X2)/(6.3*Freq_nom*Rr)
1 kW=0.2 s
10 kW=0.5 s
100 kW=1.7 s
Parameter Descriptions
VLT
®
Midi Drive FC 280
38
Danfoss A/S © 12/2015 All rights reserved.
MG07C102
4
4