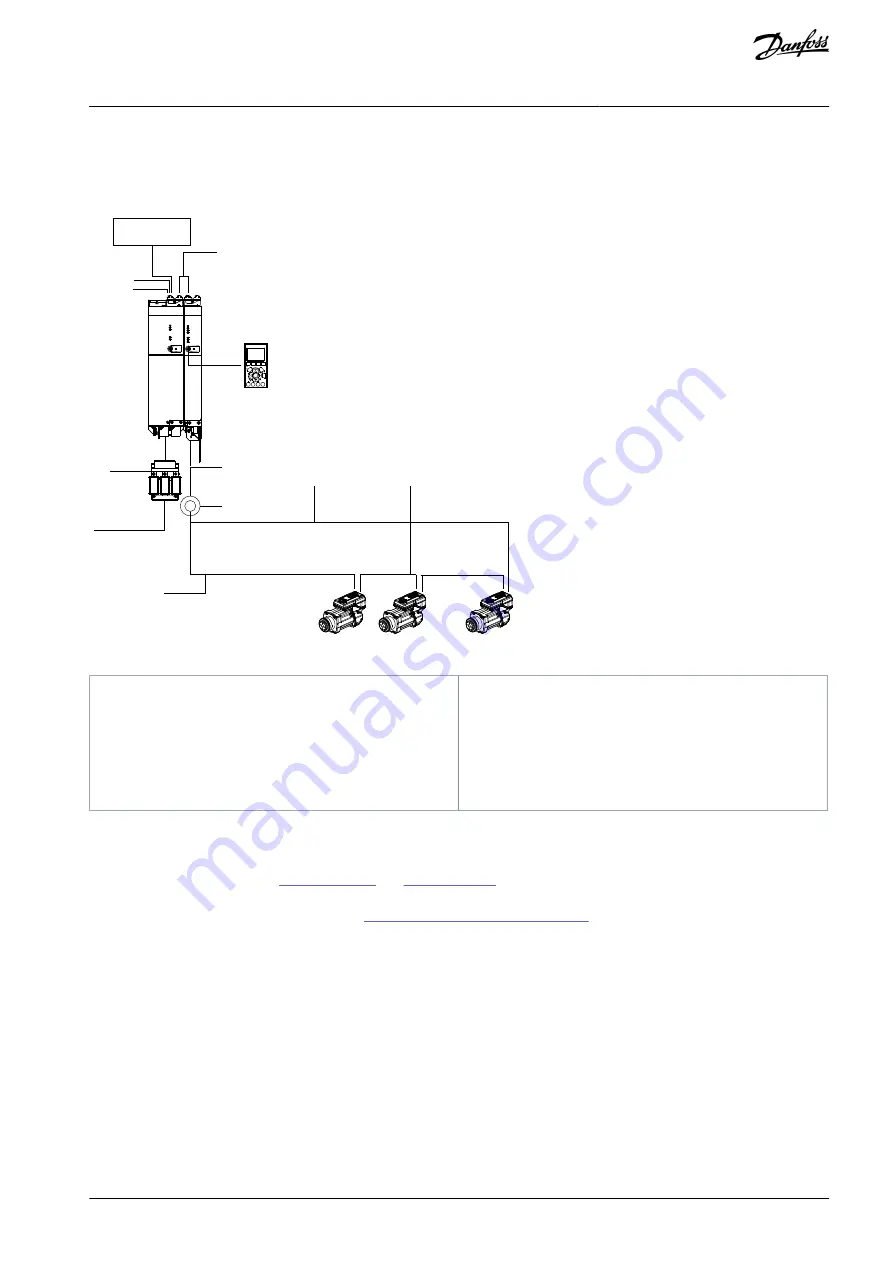
•
•
•
•
•
•
3 System Description
3.1 Overview of the ISD 511 System
AC 400–480 V
ISD 511
UDC + Real-Time Ethernet Bus + STO + UAUX
. . .
PSM
510
DAM
510
STATUS PSM
LINK/ACT
DEV
SVS ST
NET ST
X1
X2
STATUS DAM
LINK/ACT
DEV
SVS ST
NET ST
AUX
X1
X2
X3
PLC
1
4
2
5
6
3
24/48 V
STO
e30bj993.10
Status
Hand
On
Off
Reset
Auto
On
OK
Ba
ck
Ca
nce
l
Inf
o
Quick
Menu
Main
Menu
Alarm
Log
LCP
Real-Time Ethernet Bus + STO
Illustration 1: Overview of the VLT® Integrated Servo Drive ISD 511 System
1
AC line choke
2
Feed-in hybrid cable, maximum 6 m (not provided
by Danfoss)
3
Feed-in hybrid cable from DAM 510 to slip ring,
maximum 30 m (not provided by Danfoss)
4
Slip ring (not provided by Danfoss)
5
Feed-out hybrid cable, maximum 6 m (not provided
by Danfoss)
6
Loop cable, 0.235 m/0.365 m (not provided by Dan-
foss)
The ISD 511 is a high-performance decentral servo motion solution. In this decentral system, the ISD 511 servo drives are operated
in a DC group and controlled by a PLC.
The hybrid cables used in the servo system contain the DC-link supply, the Real-Time Ethernet, U
AUX
, and STO signals. For further
information on hybrid cables, see
and
A maximum of 68 ISD 511 servo drives can be connected on 1 line and a maximum of 5 ISD 511 servo drives can be grounded in 1
group via the 2 PE screws on the servo drive (see
5.3.1 Grounding the ISD 511 Servo Drive
). The minimum cable cross-section is
4 mm
2
.
The ISD 511 system consists of:
VLT
®
Integrated Servo Drive ISD
®
511
Power Supply Module (PSM 510)
Decentral Access Module (DAM 510)
Auxiliary Capacitors Module (ACM 510), optional
Expansion Module (EXM 510), optional
Cabling infrastructure
AQ377148425069en-000101
/ 130R1213 | 21
Danfoss A/S © 2023.08
System Description
VLT® Servo Drive System ISD 511
Operating Guide