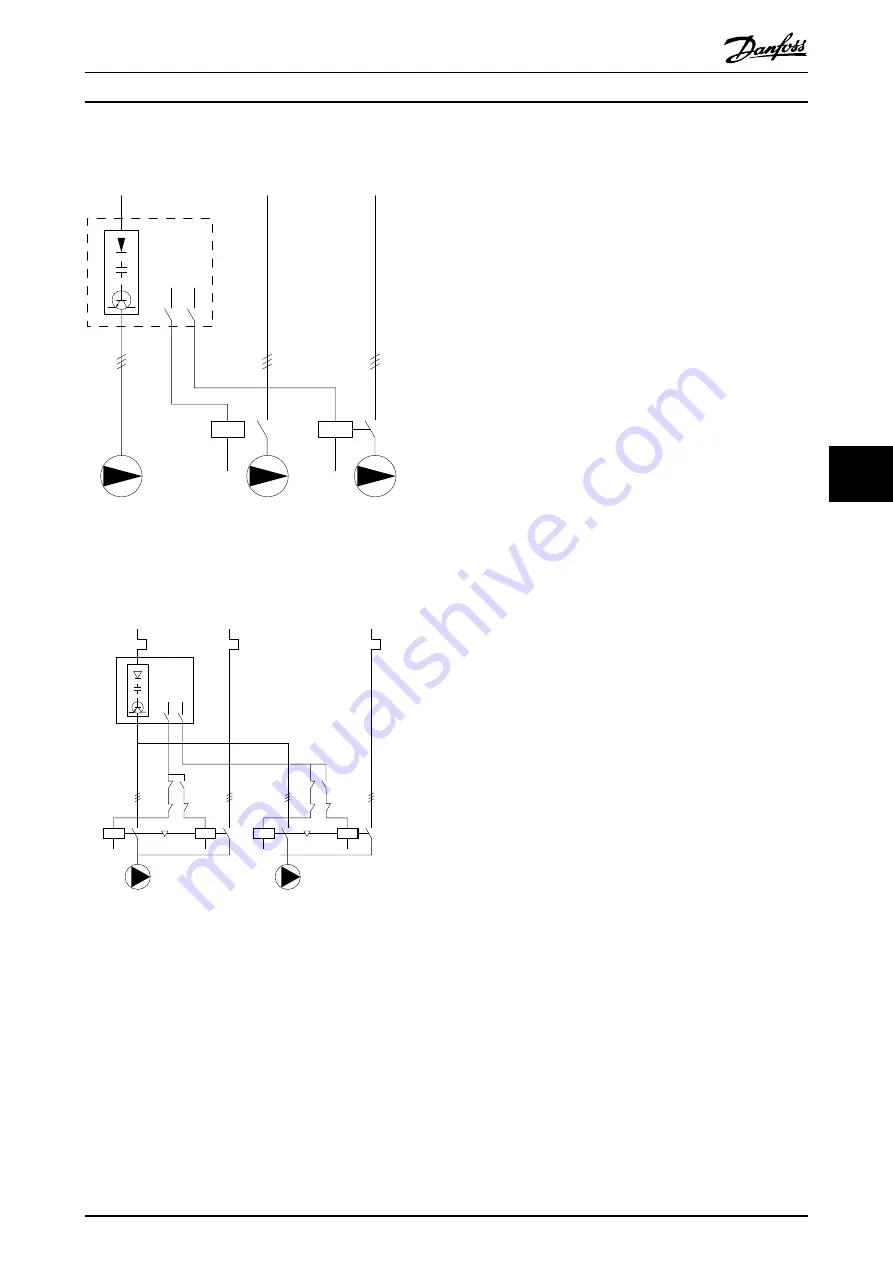
7.1.11 Fixed Variable Speed Pump Wiring Diagram
L1/L2/L3
L1/L2/L3
L1/L2/L3
Po
w
er S
ec
tion
RELA
Y 1
RELA
Y 2
130BA376.10
Illustration 7.9 Fixed Variable Speed Pump Wiring Diagram
7.1.12 Lead Pump Alternation Wiring
Diagram
130BA377.13
L1/L2/L3
FC
L1/L2/L3
L1/L2/L3
k3
k2
k3
k1
K2
K1
K1
K1
K4
K3
K4
K3
R1
R2
Illustration 7.10 Lead Pump Alternation Wiring Diagram
Every pump must be connected to 2 contactors (K1/K2 and
K3/K4) with a mechanical interlock. Thermal relays or other
motor protection devices must be applied according to
local regulation and/or individual demands.
•
RELAY 1 (R1) and RELAY 2 (R2) are the built-in
relays in the frequency converter.
•
When all relays are de-energised, the first built in
relay to be energised cuts in the contactor
corresponding to the pump controlled by the
relay. E.g. RELAY 1 cuts in contactor K1, which
becomes the lead pump.
•
K1 blocks for K2 via the mechanical interlock
preventing mains to be connected to the output
of the frequency converter. (via K1).
•
Auxiliary break contact on K1 prevents K3 to cut
in.
•
RELAY 2 controls contactor K4 for on/off control
of the fixed speed pump.
•
At alternation both relays de-energises and now
RELAY 2 is energised as the first relay.
Application Examples
Design Guide
MG11BC02
Danfoss A/S © Rev. 06/2014 All rights reserved.
127
7
7