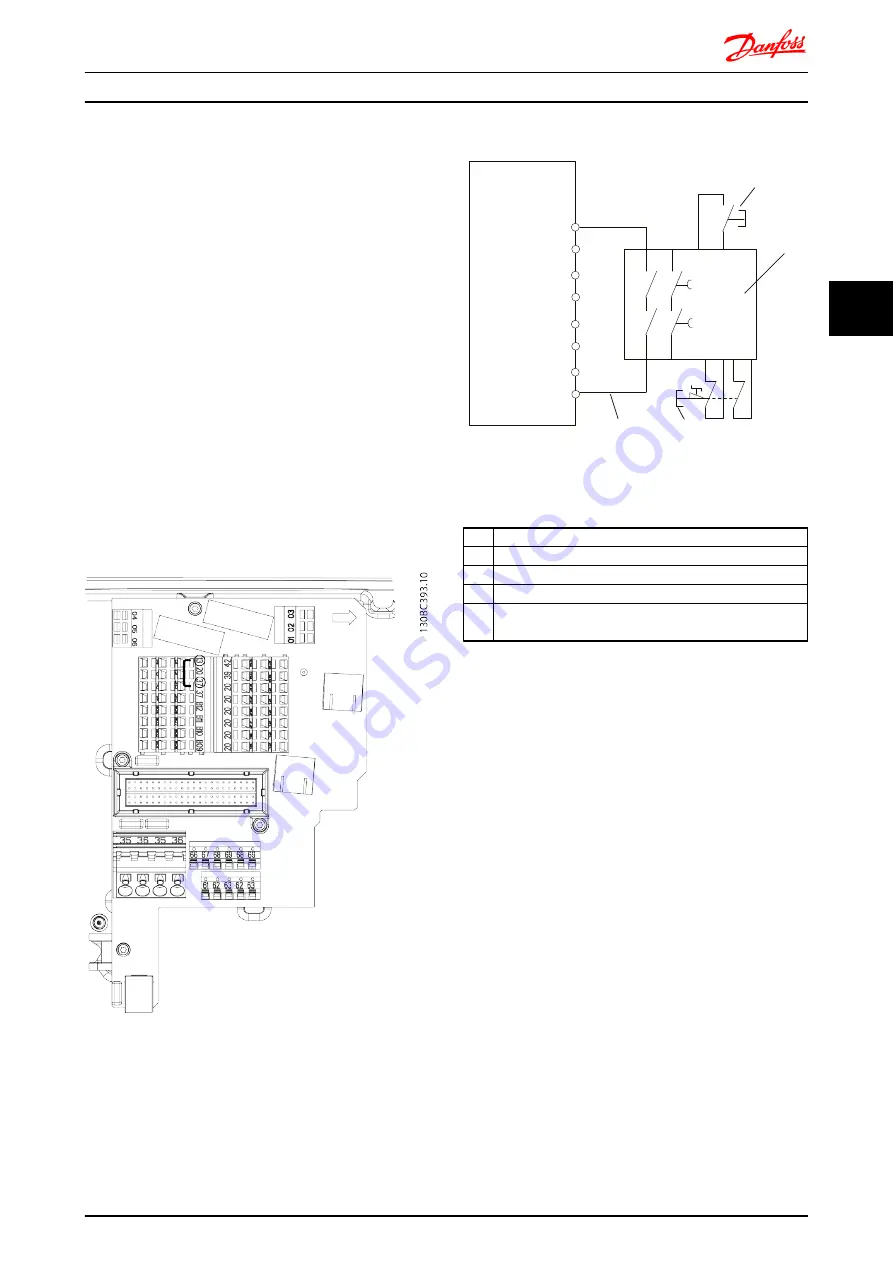
the Safe torque off function, the system can
produce an alignment torque which maximally
rotates the motor shaft by 180/p degrees. p
denotes the pole pair number.
•
This function is suitable for performing
mechanical work on the system or affected area
of a machine only. It does not provide electrical
safety. Do not use this function as a control for
starting and/or stopping the frequency converter.
Follow these steps to perform a safe installation of the
frequency converter:
1.
Remove the jumper wire between control
terminals 37 and 12 or 13. Cutting or breaking
the jumper is not sufficient to avoid short-
circuiting (see jumper on
).
2.
Connect an external Safety monitoring relay via a
NO safety function to terminal 37 (safe stop) and
either terminal 12 or 13 (24 V DC). Follow the
instruction for the safety device. The Safety
monitoring relay must comply with Category 3
(EN 954-1)/PL “d” (ISO 13849-1) or SIL 2 (EN
62061).
Illustration 4.23 Jumper between Terminal 12/13 (24 V) and 37
130BC971.10
12
2
4
1
5
3
37
Illustration 4.24 Installation to Achieve a Stopping Category 0
(EN 60204-1) with Safety Cat. 3 (EN 954-1)/PL “d” (ISO 13849-1)
or SIL 2 (EN 62061).
1
Frequency converter
2
Reset button
3
Safety relay (cat. 3, PL d or SIL2
4
Emergency stop button
5
Short-circuit protected cable (if not inside installation IP54
cabinet)
Table 4.28 Legend
Safe Stop Commissioning Test
After installation and before first operation, perform a
commissioning test of the installation using safe stop.
Moreover, perform the test after each modification of the
installation.
Example with STO
A safety relay evaluates the E-Stop button signals and
triggers an STO function on the frequency converter in the
event of an activation of the E-Stop button (See
). This safety function corresponds to a
category 0 stop (uncontrolled stop) in accordance with IEC
60204-1. If the function is triggered during operation, the
motor runs down in an uncontrolled manner. The power
to the motor is safely removed, so that no further
movement is possible. It is not necessary to monitor plant
at a standstill. If an external force effect can occur, provide
additional measures to prevent any potential movement
(for example, mechanical brakes).
Application Examples
VLT
®
Decentral Drive FCD 302
MG04H102 - VLT
®
is a registered Danfoss trademark
69
4
4