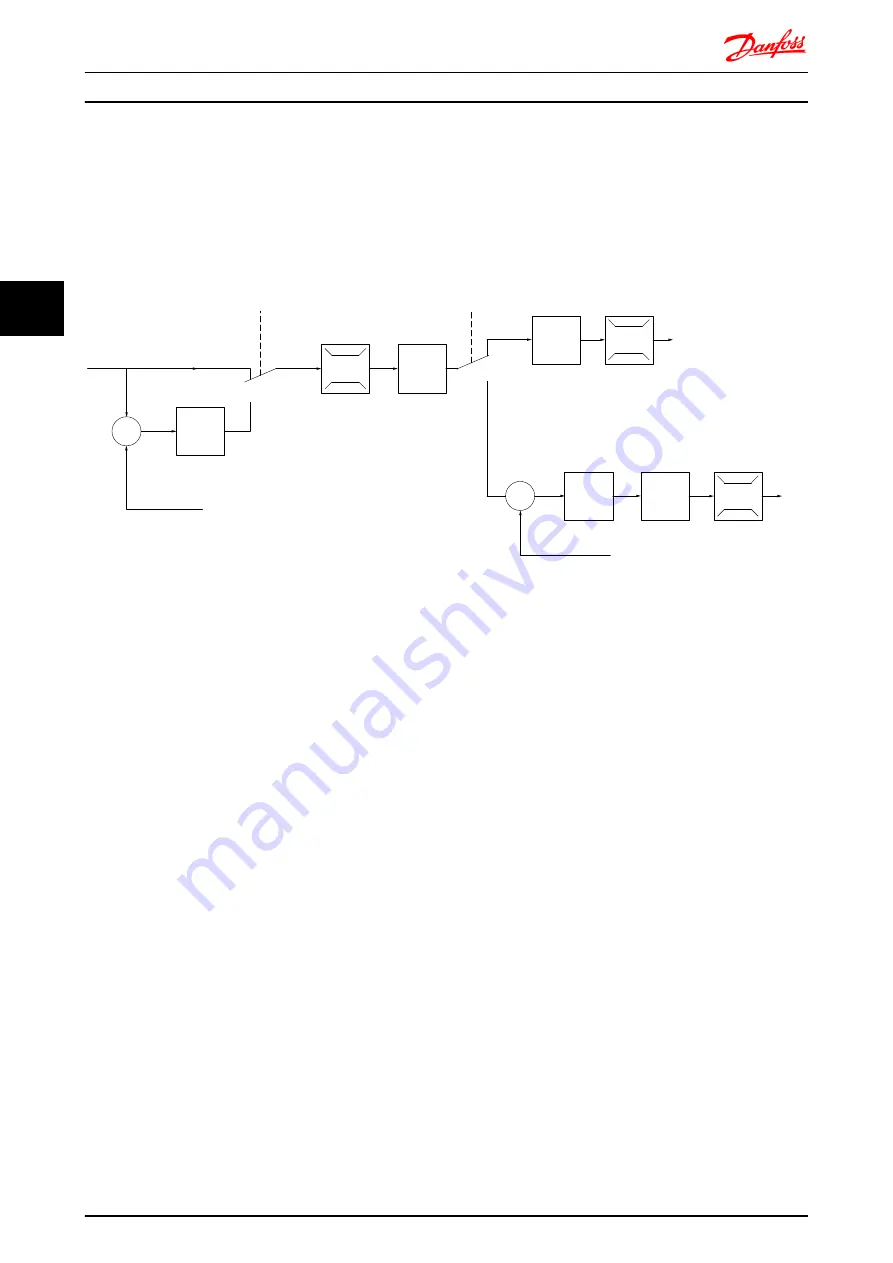
4.5 Control Structures
4.5.1 Control Structure in VVC
plus
Advanced Vector Control
+
_
+
_
Config. mode
Ref.
Process
P 1-00
High
+f max.
Low
-f max.
P 4-11
Motor speed
low limit (RPM)
P 4-12
Motor speed
low limit (Hz)
P 4-13
Motor speed
high limit (RPM)
P 4-14
Motor speed
high limit (Hz)
Motor
controller
Ramp
Speed
PID
P 7-20 Process feedback
1 source
P 7-22 Process feedback
2 source
P 7-00 Speed PID
feedback source
P 1-00
Config. mode
P 4-19
Max. output freq.
-f max.
Motor
controller
P 4-19
Max. output freq.
+f max.
P 3-**
P 7-0*
130BA055.10
Illustration 4.15 Control Structure in VVC
plus
Open Loop and Closed Loop Configurations
In the configuration shown in
,
1-01 Motor
Control Principle
is set to
[1] VVC
plus
and
1-00 Configuration
Mode
is set to
[0] Speed open loop
. The resulting reference
from the reference handling system is received and fed
through the ramp limitation and speed limitation before
being sent to the motor control. The output of the motor
control is then limited by the maximum frequency limit.
If
1-00 Configuration Mode
is set to
[1] Speed closed loop
the resulting reference passes from the ramp limitation
and speed limitation into a speed PID control. The Speed
PID control parameters are located in the parameter group
7-0*. The resulting reference from the Speed PID control is
sent to the motor control limited by the frequency limit.
Select
[3] Process
in
1-00 Configuration Mode
to use the
process PID control for closed loop control of for example,
speed or pressure in the controlled application. The
Process PID parameters are located in parameter group
7-2* and 7-3*.
4.5.2 Control Structure in Flux Sensorless
Control structure in Flux sensorless open loop and closed
loop configurations.
Application Examples
VLT
®
Decentral Drive FCD 302
62
MG04H102 - VLT
®
is a registered Danfoss trademark
4
4