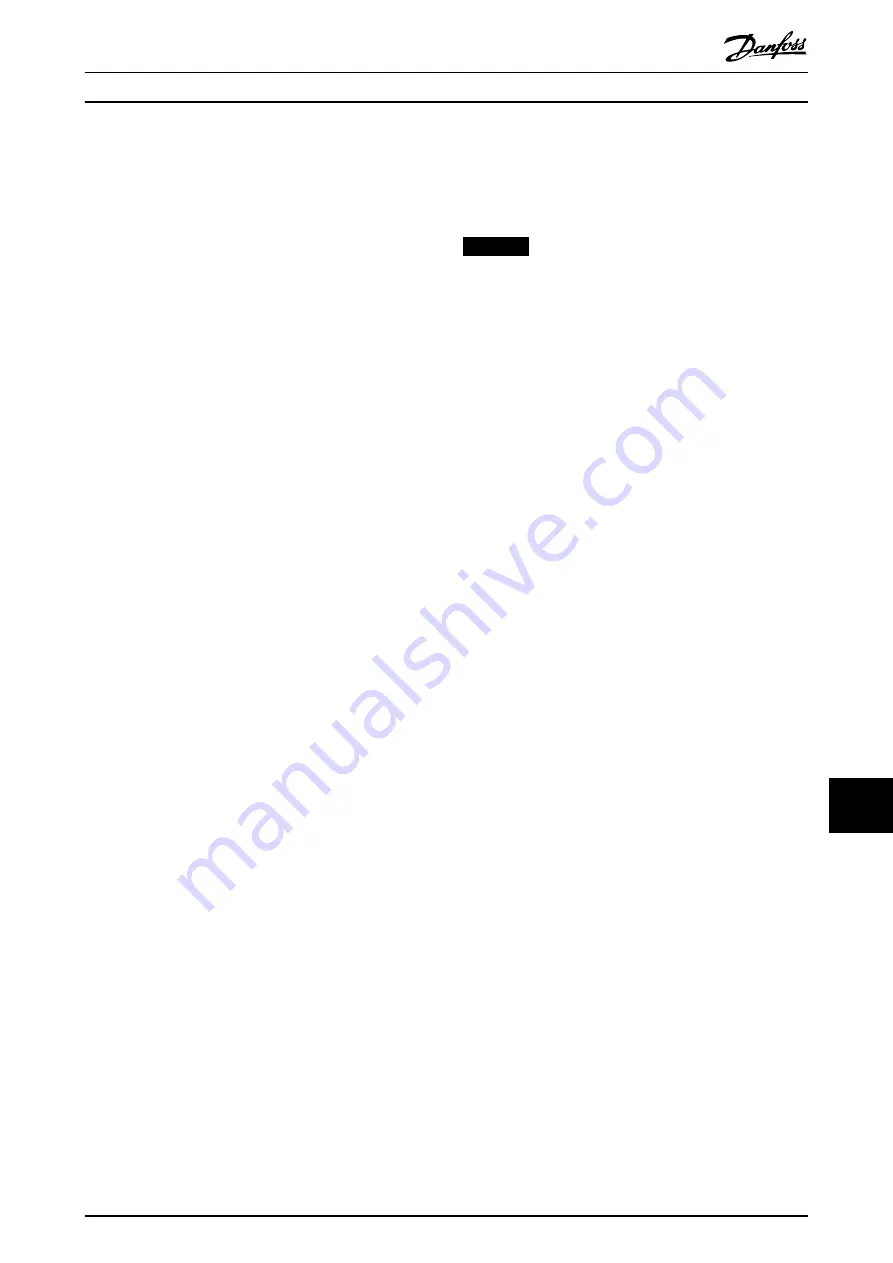
13.2.2 Control Card and Control Card Mounting Plate
The control card does not need to be disassembled before the control card mounting plate is removed from the drive. To
remove or replace the control card mounting plate with the card attached, use the following steps. See
Disassembly
1.
Open the front panel door or remove the front
cover, depending on the type of enclosure.
2.
In IP21/IP54 units, unplug the LCP cable.
3.
Unplug the USB connector, if present.
4.
Remove any customer control wiring from the
control card and option cards.
5.
Remove 4 screws (T20) from the corners of the
control card mounting plate.
6.
Unplug the ribbon cable connecting the control
card and power card. To release the cable, press
out on the clasps at each end of the cable
connector on the power card.
NOTICE
UNIQUE TORQUE VALUES
Tighten screws (T20) to the non-standard torque value
specified in the following steps. Tighten remaining
fasteners according to
.
Reassembly
1.
Attach the ribbon cable connecting the control
card to the power card. Click shut the clasps on
each end of the cable connector.
2.
Secure 4 screws (T20) at the corners of the
control card mounting plate. Torque to 2.27 Nm
(20.1 lb-in).
3.
Reconnect any customer control wiring to the
control card and option cards.
4.
In IP21/IP54 units, connect the LCP cable.
5.
Connect the USB, if present.
6.
Reattach the front cover, if present depending on
the enclosure.
E1h–E4h Drive Disassembly a...
Service Guide
MG94A502
Danfoss A/S © 02/2019 All rights reserved.
261
13
13