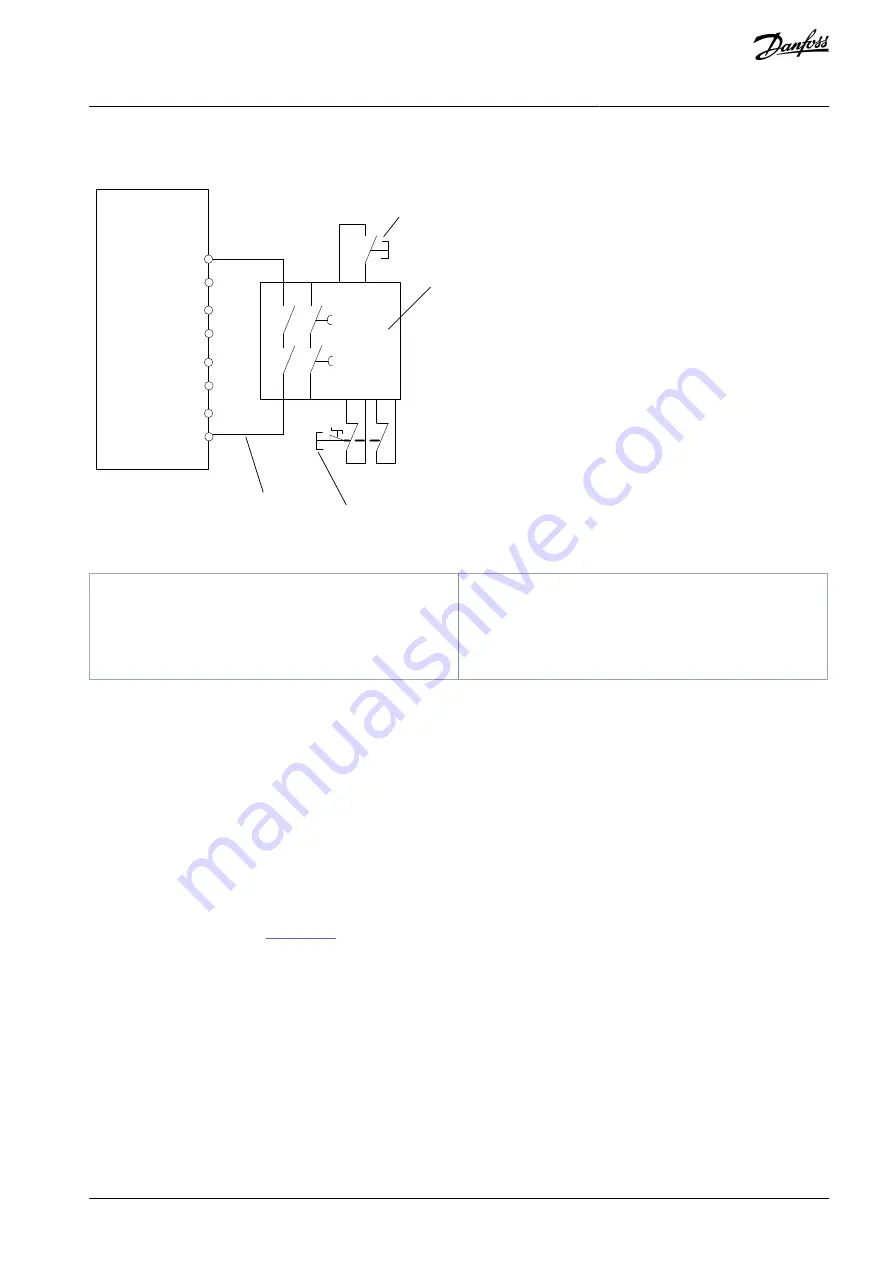
•
•
•
•
•
•
•
•
5.3 Emergency Stop of Drive with STO Using Safety Relay - Category 3, PL d, SIL2
e3
0b
g7
75
.1
1
12
37
3
2
FC
4
1
Illustration 6: Installation Example Achieving a Stop Category 0 (EN 60204-1) with Safety Cat. 3/PL "d" (ISO 13849-1) or SIL2 (EN 62061 and IEC
61508)
1
Safety relay (Category 3, PL d, SIL 2)
2
Emergency stop button
3
Reset button
4
Short-circuited protected cable (if not inside installa-
tion IP54 cabinet). See ISO 13489-2, Table D.4 for fur-
ther information
Safety function
If there is an emergency, the emergency stop device is activated. The STO function of the drive is activated. Following a stop or
emergency stop command, the drive is halted.
Design features
The circuit can be used up to Category 3, PL s (ISO 13849-1) or SIL2 (EN 62061 and IEC 61508).
For PL d, the complete safety functions have to be calculated (MTTFd).
Use the basic safety principles.
The device used for activation of STO and safety relay must be suitable for the selected category PL and SIL.
When implementing the emergency stop, pay attention to the following tips:
Any non-safety related standards should be fulfilled for the application and its components.
The application designer is responsible for selecting suitable components.
The cable shown as bold in
has to be short-circuit protected according to ISO 13849-2 table D.4.
To fulfill PL d, the MTTFd and DC for the whole safety function have to be calculated.
This setup can be used if a dual positive switching device is used. Depending on the safety relay, it is also possible to connect sever-
al activation devices to 1 STO.
Implementation of SISTEMA using Danfoss VLT library
As an example, use the subsystem "VLT® AutomationDrive FC 302/FCD 302 Safe Torque Off (Terminal 37)". There is no need for
editing all the parameters which are set in the library.
AQ313340186453en-00101 / 130R0544 | 17
Danfoss A/S © 2021.03
Application Examples
Safe Torque Off
Operating Guide