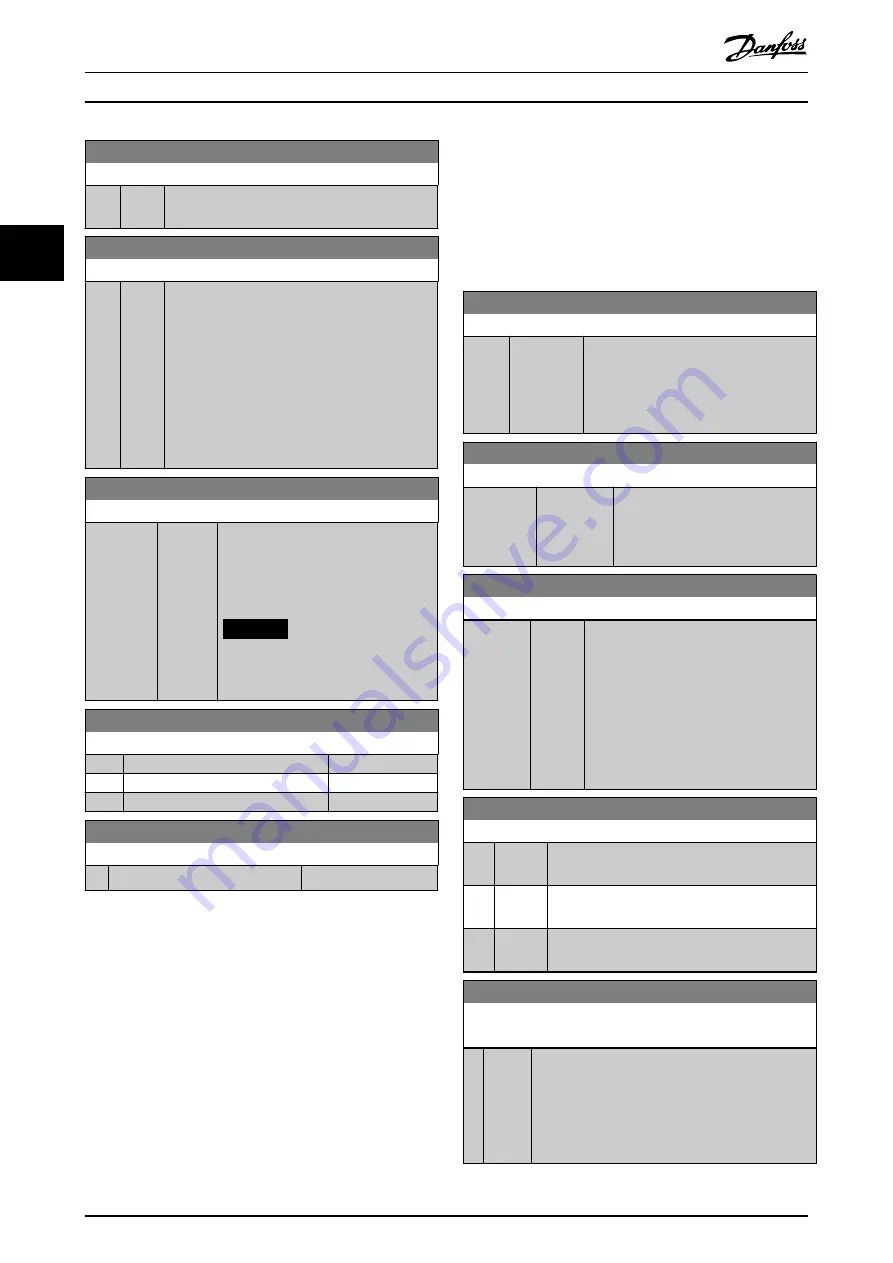
14-24 Trip Delay at Current Limit
Range:
Function:
set the parameter to 60 s. Thermal monitoring of
the frequency converter remains active.
14-25 Trip Delay at Torque Limit
Range:
Function:
60 s
*
[0 -
60 s]
Enter the torque limit trip delay in s. When the
output torque reaches the torque limits
(
parameter 4-16 Torque Limit Motor Mode
and
parameter 4-17 Torque Limit Generator Mode
), a
warning is triggered. When the torque limit
warning has been continuously present for the
period specified in this parameter, the frequency
converter trips. Disable the trip delay by setting
the parameter to 60 s. Thermal monitoring of the
frequency converter remains active.
14-26 Trip Delay at Inverter Fault
Range:
Function:
Size related
*
[ 0 - 35
s]
When the frequency converter detects
an overvoltage in the set time, trip is
effected after the set time.
If value is 0, protection mode is
disabled.
NOTICE
Disable protection mode in
hoisting applications.
14-28 Production Settings
Range:
Function:
0
*
[No action]
1
[Service reset]
[2]
Set Production Mode
14-29 Service Code
Range:
Function:
0
*
[-2147483647 - 2147483647 ]
For internal use only.
3.14.3 14-3* Current Limit Control
The frequency converter features an integral current limit
controller, which is activated when the motor current, and
thus the torque, is higher than the torque limits set in
parameter 4-16 Torque Limit Motor Mode
and
parameter 4-17 Torque Limit Generator Mode
.
When the current limit is reached during motor operation
or regenerative operation, the frequency converter tries to
reduce torque below the preset torque limits as quickly as
possible without losing control of the motor.
While the current control is active, the frequency converter
can only be stopped by setting a digital input to
[2] Coast
inverse
or
[3] Coast and reset inv.
Any signals on terminals
18–33 are not active until the frequency converter is no
longer near the current limit.
By using a digital input set to
[2] Coast inverse
or
[3] Coast
and reset inv.
, the motor does not use the ramp-down
time, since the frequency converter is coasted. If a quick
stop is necessary, use the mechanical brake control
function along with an external electro-mechanical brake
attached to the application.
14-30 Current Lim Ctrl, Proportional Gain
Range:
Function:
100 %
*
[0 - 500 %] Enter the proportional gain value for the
current limit controller. Selection of a high
value makes the controller react faster. Too
high a setting leads to controller
instability.
14-31 Current Lim Ctrl, Integration Time
Range:
Function:
Size related
*
[0.002 - 2 s] Controls the current limit control
integration time. Setting it to a lower
value makes it react faster. A setting
too low leads to controller instability.
14-32 Current Lim Ctrl, Filter Time
Range:
Function:
Size
related
*
[1 -
100 ms]
Controls the current limit control low-pass
filter.
This makes it possible to react to peak
values or to average values. When
selecting average values, it is sometimes
possible to run with higher output current
and instead trip on the hardware limit for
current. However, the control reacts slower
as it does not react on immediate values.
14-35 Stall Protection
Option:
Function:
Parameter 14-35 Stall Protection
is active in flux
mode only.
[0]
Disabled Disables stall protection in field weakening flux
mode and might cause the motor to be lost.
[1]
*
Enabled Enables stall protection in field weakening flux
mode.
14-36 Field-weakening Function
Select the field weakening function mode in flux mode.
Range:
Function:
0
*
[Auto] In this mode, the frequency converter calculates the
optimal torque output.
Measured DC-link voltage determines the phase-to-
phase motor voltage. Magnetizing reference is based
on the actual voltage and utilizes the information
about the model of the motor.
Parameter Descriptions
VLT
®
AutomationDrive FC 301/302
196
Danfoss A/S © 10/2018 All rights reserved.
MG33MP02
3
3
Summary of Contents for VLT AutomationDrive FC 302
Page 2: ......