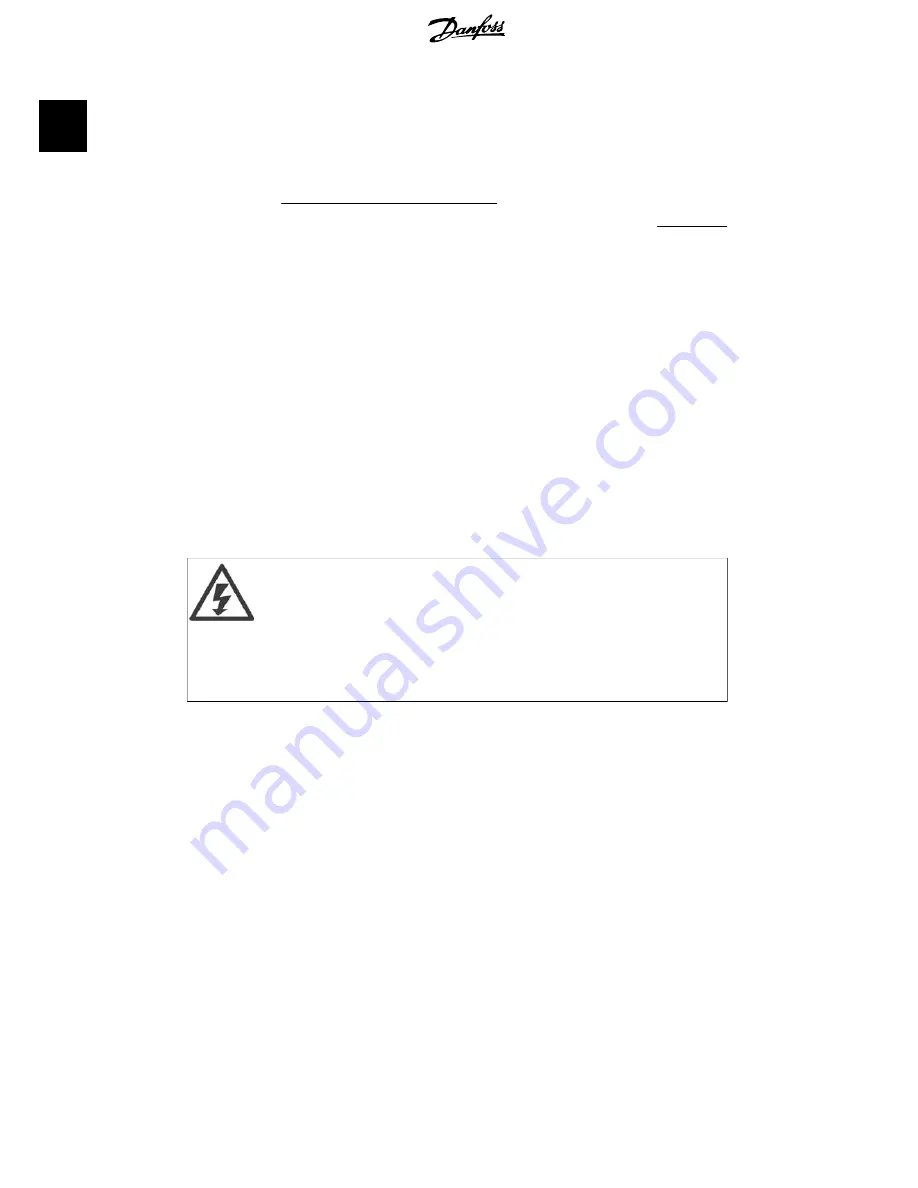
1.1.3. Warning Against Unintended Start
1.
The motor can be brought to a stop by means of digital commands, bus commands,
references or a local stop, while the frequency converter is connected to mains.
If personal safety considerations make it necessary to ensure that no unintended start
occurs, these stop functions are not sufficient.
2.
While parameters are being changed, the motor may start. Consequently, the stop key
[STOP/RESET] must always be activated, following which data can be modified.
3.
A motor that has been stopped may start if faults occur in the electronics of the frequency
converter, or if a temporary overload or a fault in the supply mains or the motor con-
nection ceases.
1.1.4. Installation of Mechanical Brake (VLT 5000 and VLT 5000
FLUX)
Do not connect a mechanical brake to the output from the frequency converter before the relevant
parameters for brake control have been defined. (Select output in parameters 319, 321, 323 or
326 and cut-in current and frequency in parameters 223 and 225).
1.1.5. Use on Isolated Mains
See section RFI Switch in the Operating Instructions regarding use on isolated mains. It is im-
portant to follow the recommendations regarding installation on IT mains, including isolated delta
systems, since sufficient protection of the complete installation must be observed. Not taking care
using relevant monitoring for IT mains may result in damage.
Warning:
Touching the electrical parts may be fatal - even after the equipment has been dis-
connected from mains.
Also make sure that other voltage inputs have been disconnected, such as external
24 V DC, load-sharing (linkage of DC intermediate circuit), as well as the motor
connection for kinetic back-up.
D1 and D2 enclosures: Wait at least 20 minutes.
E1 enclosures: Wait at least 46 minutes.
1. General Information
VLT
®
5000/6000/8000
High Power Installation Guide
4
MI.90.J2.02 - VLT
®
is a registered Danfoss trademark
1