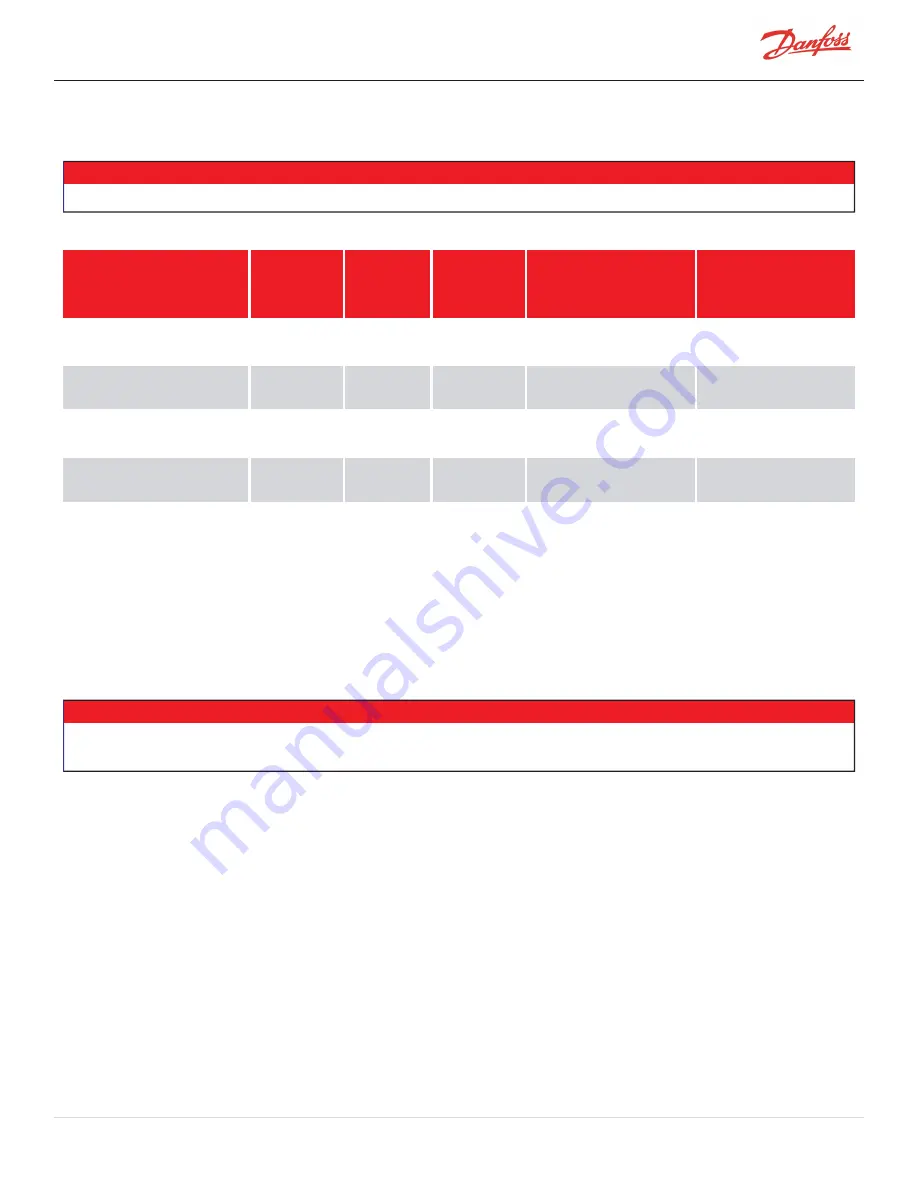
Chapter 16.0 Physical Data
This section contains data relative to compressor mounting, service clearance, and piping connections.
NOTE
The dimensions in the following figures show measurements in metric with imperial in parenthesis.
Table 16-1 Physical Dimensions
Model
Length
Width
Height
Shipping Weight
(Includes all shipping
material)
Compressor Total
Weight (Compressor
Only)
TTS300/TGS230
788 mm
(31.02")
518 mm
(20.4")
487 mm
(19.17)
134 kg (296 lbs)
123.4 kg (272 lbs)
TTS350/TGS310/TGS490
788 mm
(31.02")
518 mm
(20.4")
487 mm
(19.17")
143 kg (315 lbs)
132 kg (291 lbs)
TTS400/TGS390
788 mm
(31.02")
518 mm
(20.4")
487 mm
(19.17")
142 kg (312 lbs)
130.6 kg (288 lbs)
TTS700/TGS520
788 mm
(31.02")
518 mm
(20.4")
487 mm
(19.17")
144 kg (318 lbs)
132 kg (294 lbs)
TTH375/TGH285
932 mm
(36.7")
590 mm
(23.2")
487 mm
(19.17")
181 kg (400 lbs)
163.7 kg (361 lbs)
16.1 Clearance
Adequate clearance around the compressor is essential to facilitate maintenance and service. Removal of the
compressor top and service-side covers requires a minimum clearance of 600 mm (24”) and 406 mm (16”),
respectively.
NOTE
If insulators are used at the four mounting base points, the overall height of the compressor will change. Be sure to measure accordingly
based on the insulator used.
M-AP-001-EN Rev. S-9/8/2021 Page 95 of 136
Summary of Contents for Turbocor TTS Series
Page 2: ...THIS PAGE INTENTIONALLY LEFT BLANK Page 2 of 136 M AP 001 EN Rev S 9 8 2021...
Page 8: ...Page 8 of 136 M AP 001 EN Rev S 9 8 2021 THIS PAGE INTENTIONALLY LEFT BLANK...
Page 10: ...Page 10 of 136 M AP 001 EN Rev S 9 8 2021 THIS PAGE INTENTIONALLY LEFT BLANK...
Page 20: ...Figure 2 2 Compressor Nomenclature Page 20 of 136 M AP 001 EN Rev S 9 8 2021...
Page 24: ...Page 24 of 136 M AP 001 EN Rev S 9 8 2021 THIS PAGE INTENTIONALLY LEFT BLANK...
Page 40: ...Page 40 of 136 M AP 001 EN Rev S 9 8 2021 THIS PAGE INTENTIONALLY LEFT BLANK...
Page 44: ...Page 44 of 136 M AP 001 EN Rev S 9 8 2021 THIS PAGE INTENTIONALLY LEFT BLANK...
Page 52: ...Page 52 of 136 M AP 001 EN Rev S 9 8 2021 THIS PAGE INTENTIONALLY LEFT BLANK...
Page 54: ...Page 54 of 136 M AP 001 EN Rev S 9 8 2021 THIS PAGE INTENTIONALLY LEFT BLANK...
Page 66: ...Page 66 of 136 M AP 001 EN Rev S 9 8 2021 THIS PAGE INTENTIONALLY LEFT BLANK...
Page 68: ...Page 68 of 136 M AP 001 EN Rev S 9 8 2021 THIS PAGE INTENTIONALLY LEFT BLANK...
Page 70: ...Page 70 of 136 M AP 001 EN Rev S 9 8 2021 THIS PAGE INTENTIONALLY LEFT BLANK...
Page 72: ...Page 72 of 136 M AP 001 EN Rev S 9 8 2021 THIS PAGE INTENTIONALLY LEFT BLANK...
Page 74: ...Page 74 of 136 M AP 001 EN Rev S 9 8 2021 THIS PAGE INTENTIONALLY LEFT BLANK...
Page 80: ...Page 80 of 136 M AP 001 EN Rev S 9 8 2021 THIS PAGE INTENTIONALLY LEFT BLANK...
Page 94: ...Page 94 of 136 M AP 001 EN Rev S 9 8 2021 THIS PAGE INTENTIONALLY LEFT BLANK...
Page 110: ...Page 110 of 136 M AP 001 EN Rev S 9 8 2021 THIS PAGE INTENTIONALLY LEFT BLANK...
Page 112: ...Page 112 of 136 M AP 001 EN Rev S 9 8 2021 THIS PAGE INTENTIONALLY LEFT BLANK...
Page 114: ...Page 114 of 136 M AP 001 EN Rev S 9 8 2021 THIS PAGE INTENTIONALLY LEFT BLANK...
Page 126: ...Page 126 of 136 M AP 001 EN Rev S 9 8 2021 THIS PAGE INTENTIONALLY LEFT BLANK...
Page 128: ...Figure B 2 Grounding Diagram Page 128 of 136 M AP 001 EN Rev S 9 8 2021...
Page 132: ...Page 132 of 136 M AP 001 EN Rev S 9 8 2021 THIS PAGE INTENTIONALLY LEFT BLANK...
Page 134: ...Page 134 of 136 M AP 001 EN Rev S 9 8 2021 THIS PAGE INTENTIONALLY LEFT BLANK...