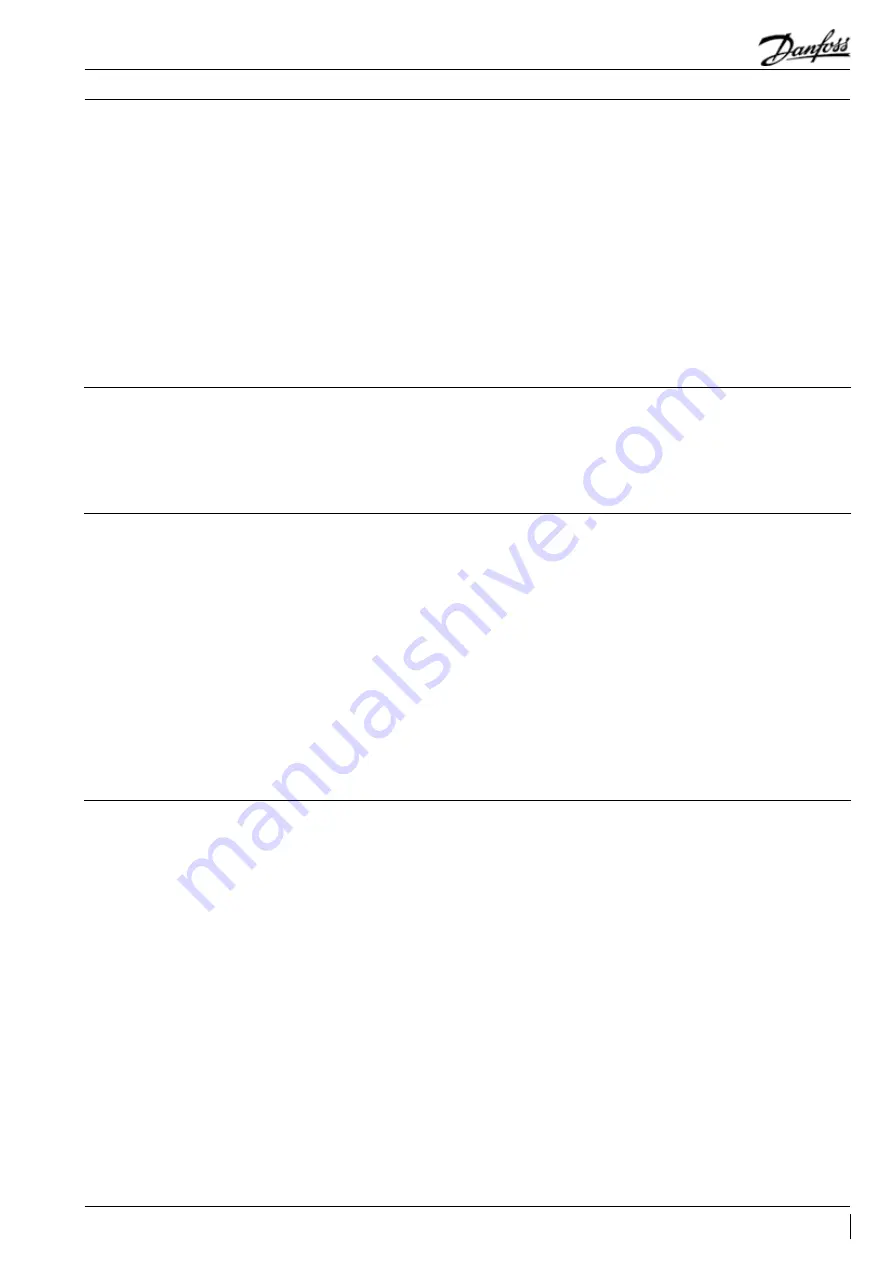
Installation and Operation
4.7 Refrigerant and oil
charge
4.8 Verification before
operating
4.9 First start-up
4.10 Verification of the unit
while operating
• Use individual protection equipment (IPE)
such as safety glasses and gloves.
• Never start the compressor under vacuum.
Keep the compressor switched off.
• Before performing the refrigerant charge,
verify if the oil level is between ¼ and ¾ on the
compressor oil display. If necessary, add oil to
the compressors, refer to the compressor’s label
for oil type.
• Only use the coolant for which the unit was
designed for.
• Perform the refrigerant charge in liquid phase
into the condenser and in the liquid receiver.
Make sure to perform a slow refrigerant
charge until it reaches 4-5 bar in systems
with R404A/507.
• Never put liquid refrigerant through the
suction line.
• Never use additive or oil mixtures.
• The remaining charge is carried out until the
installation has reached a stable nominal
condition level during the operation.
• Never leave the filling cylinder connected to
the system.
• Use safety devices according to locally
applicable regulations and security standards.
• Verify if all electrical connections are attached
correctly and in accordance with the local
regulations.
• Keep the crankcase heater switched on for at
least 12 hours before the system start-up, for the
guarantee of proper lubrication and elimination
of the liquid refrigerant from the compressor's
crankcase.
• Never switch on the unit without having
performed a refrigerant charge .
• All service valves must be in the open position.
See figure 5.
• Verify if the power supply is adequately
connected.
• Verify if the crankcase heater is working.
• Verify if the fan can rotate freely.
• Verify if high and low pressure are balanced.
• Energize the unit and verify the conformity of
the wiring, the tension in the terminals and the
phase sequence.
• The potential reverse rotation of a three-phased
compressor can be detected by no pressure
increase, an abnormal sound level of the
compressor and a lower energy consumption
than the one expected. In this case, immediately
switch off the unit and connect the phases to
their appropriate terminals.
• If the direction of rotation is correct, the indication
of low pressure on the low pressure gauge must
display a decreasing pressure and the indication
of high pressure in the high pressure measurer
must display an increasing pressure.
• The electronic buoys must comply with the
indication.
• Check the rotation direction of the fan. The air
must flow from the condenser to the fan (air
flow from bottom to top).
• Check the high pressure stabilization and the
power supply stability.
• Check the suction overheating to reduce the risk
of the return of liquid to the compressor.
• Observe the compressor oil level in the
beginning and during the operation to confirm
that the oil level remains visible.
• Verify all tubing with respect to unusual
vibration. The movements exceeding 1.5mm
require corrective measures, as the use of
fixation supports in the tubing.
• Before leaving the installation site, perform
a general inspection of the installation on
cleanliness, detection of noise and leakage.
• Record type and amount of refrigerant charge,
as well as operation conditions as reference for
future inspections. Use data check sheet
15
FRCC.PC.053.A1.02
Application Guide
Summary of Contents for Optyma Trio HU2900D50
Page 1: ...Optyma Trio Application Guide http RA danfoss com br...
Page 2: ......