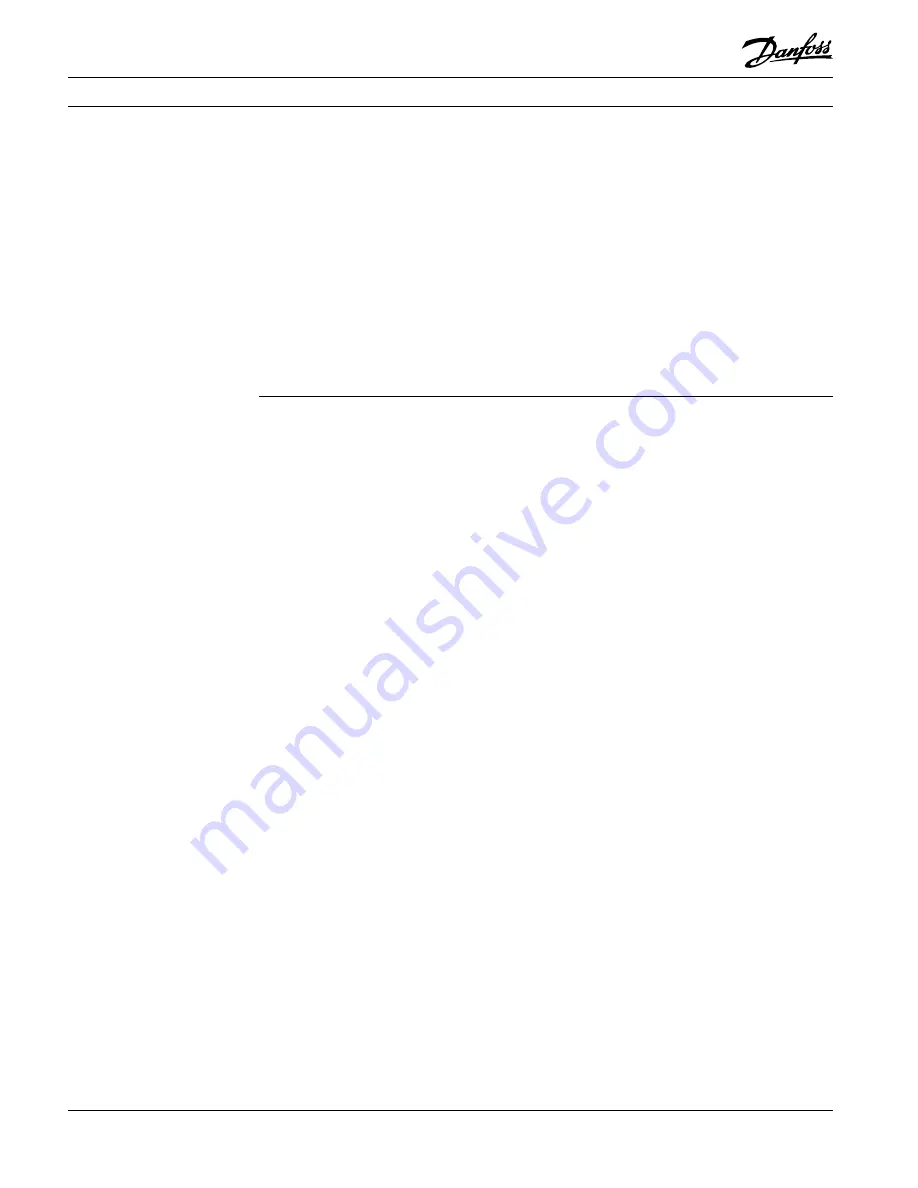
Specific application recommendations
Low ambient operations
Low ambient start-up
Under cold ambient conditions (<32°F), upon
start-up the pressure in the condenser and,
if present, the receiver may be so low that
a sufficient pressure differential across the
expansion device cannot be developed to
properly feed the evaporator. As a result, the
compressor may go into a deep vacuum, which
can lead to compressor failure due to internal
arcing and instability in the scroll members.
Under no circumstances should the compressor
be allowed to operate under vacuum. The
low-pressure control must be set in accordance
with the table section "High and low pressure
protection" in order to prevent this from
happening.
Early feeding of the evaporator and
management of the discharge pressure could
help to attenuate these effects.
Low pressure differentials can also cause
the expansion device to «hunt» erratically,
which might cause surging conditions within
the evaporator, with liquid spillover into the
compressor. This effect is most pronounced
during low load conditions, which frequently
occur during low ambient conditions.
The Danfoss SM/SY/SZ scroll compressor requires
a minimum pressure differential of 87 to 102 psi
between the suction and discharge pressures
to force the orbiting scroll down against the
oil film on the thrust bearing. Anything less
than this differential and the orbiting scroll
can lift up, causing a metal-to-metal contact.
It is therefore necessary to maintain sufficient
discharge pressure in order to ensure this
pressure differential. Care should be taken during
low ambient operations when heat removal
from air-cooled condensers is greatest and
head pressure control may be required for low
ambient temperature applications. Operation
under low pressure differential may be observed
by a significant increase in the sound power level
generated by the compressor.
It is recommended that the unit be tested and
monitored at minimum load and low ambient
conditions as well. The following considerations
should be taken into account to ensure proper
system operating characteristics.
Expansion device: The expansion device
should be sized to ensure proper control of
the refrigerant flow into the evaporator. An
oversized valve may result in erratic control.
This consideration is especially important in
manifolded units where low load conditions may
require the frequent cycling of compressors.
This can lead to liquid refrigerant entering the
compressor if the expansion valve does not
provide stable refrigerant super-heat control
under varying loads.
The superheat setting of the expansion device
should be sufficient to ensure proper superheat
levels during low loading periods. A minimum of
9 °F stable superheat is required.
Head pressure control under low ambient
conditions: Several possible solutions are
available to prevent the risk of compressor to
vacuum and low pressure differential between
the suction and discharge pressures.
In air-cooled machines, cycling the fans with
a head pressure controller will ensure that the
fans remain off until the condensing pressure
has reached a satisfactory level. Variable speed
fans can also be used to control the condensing
pressure. In water-cooled units, the same can
be performed using a water regulator valve
that is also operated by head pressure, thereby
ensuring that the water valve does not open until
the condensing pressure reaches a satisfactory
level.
The minimum condensing pressure must be
set at the minimum saturated condensing
temperature shown in the application envelopes.
Under very low ambient conditions, in which
testing has revealed that the above procedures
might not ensure satisfactory condensing and
suction pressures, the use of a head pressure
control valve is recommended. Note: This
solution requires extra refrigerant charge, which
can introduce other problems. A non-return
valve in the discharge line is recommended and
special care should be taken when designing the
discharge line.
For further information, please contact Danfoss.
Low ambient application
Application guidelines
36
FRCC.PC.003.A5.22