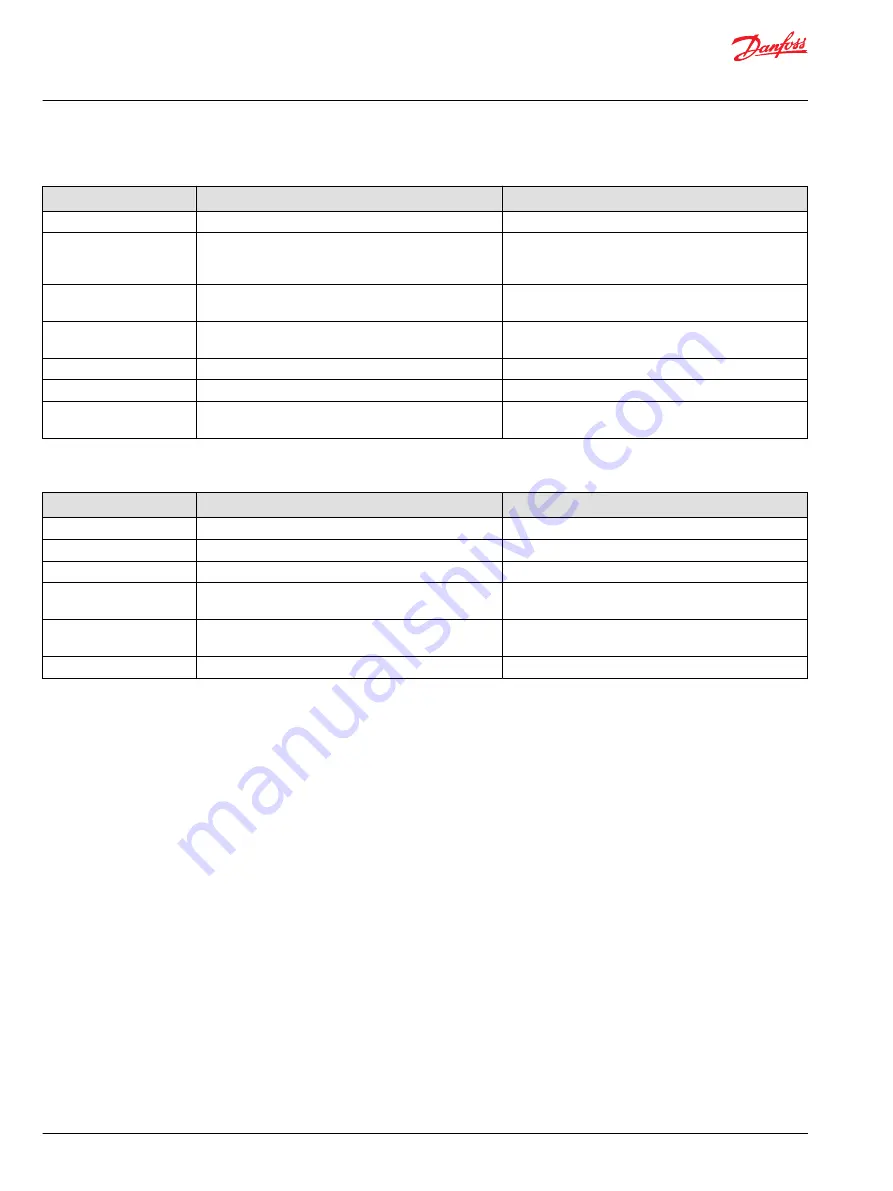
System Noise or Vibration
Item
Description
Action
Reservoir oil level
Low oil level leads to cavitation.
Fill reservoir.
Aeration of the oil/charge
inlet vacuum
Air in the system decreases efficiency of units and controls.
Air in the system is indicated by excessive noise in HST,
foaming in oil, and hot oil.
Find location where air is entering into the system and
repair. Check that inlet line is not restricted and is proper
size.
Cold oil
If oil is cold, it may be too viscous for proper function and
pump cavitates
Allow the oil to warm up to its normal operating
temperature with engine at idle speed.
Charge inlet vacuum
High inlet vacuum causes noise/cavitation.
Check that inlet line is not restricted and is proper size.
Check filter.
Shaft couplings
A loose shaft coupling causes excessive noise.
Replace loose shaft coupling.
Shaft alignment
Misaligned HST and prime mover shafts create noise.
Align shafts.
Charge check/HPRVs
Unusual noise may indicate sticking valves. Possible
contamination.
Clean/replace valves and test the unit.
Sluggish System Response
Item
Description
Action
Oil level in reservoir
Low oil level causes sluggish response.
Fill reservoir.
Charge check/HPRVs
Incorrect pressure settings affects system reaction time.
Replace charge check/HPRVs
Low prime mover speed
Low engine speed reduces system performance
Adjust engine speed.
Air in system
Air in system produces sluggish system response
Fill tank to proper level. Cycle system slowly for several
minutes to remove air from system.
Charge inlet vacuum
Inlet vacuum is too high resulting in reduced system
pressure.
Measure charge inlet vacuum. Inspect line for proper sizing.
Replace filter. Confirm proper bypass operation.
Control linkage
Linkage operating improperly
Repair or replace control linkage
Service Manual
LDU20/24 Closed Circuit Axial Piston Transmission
Troubleshooting
20 |
©
Danfoss | June 2021
AX152886481311en-000304