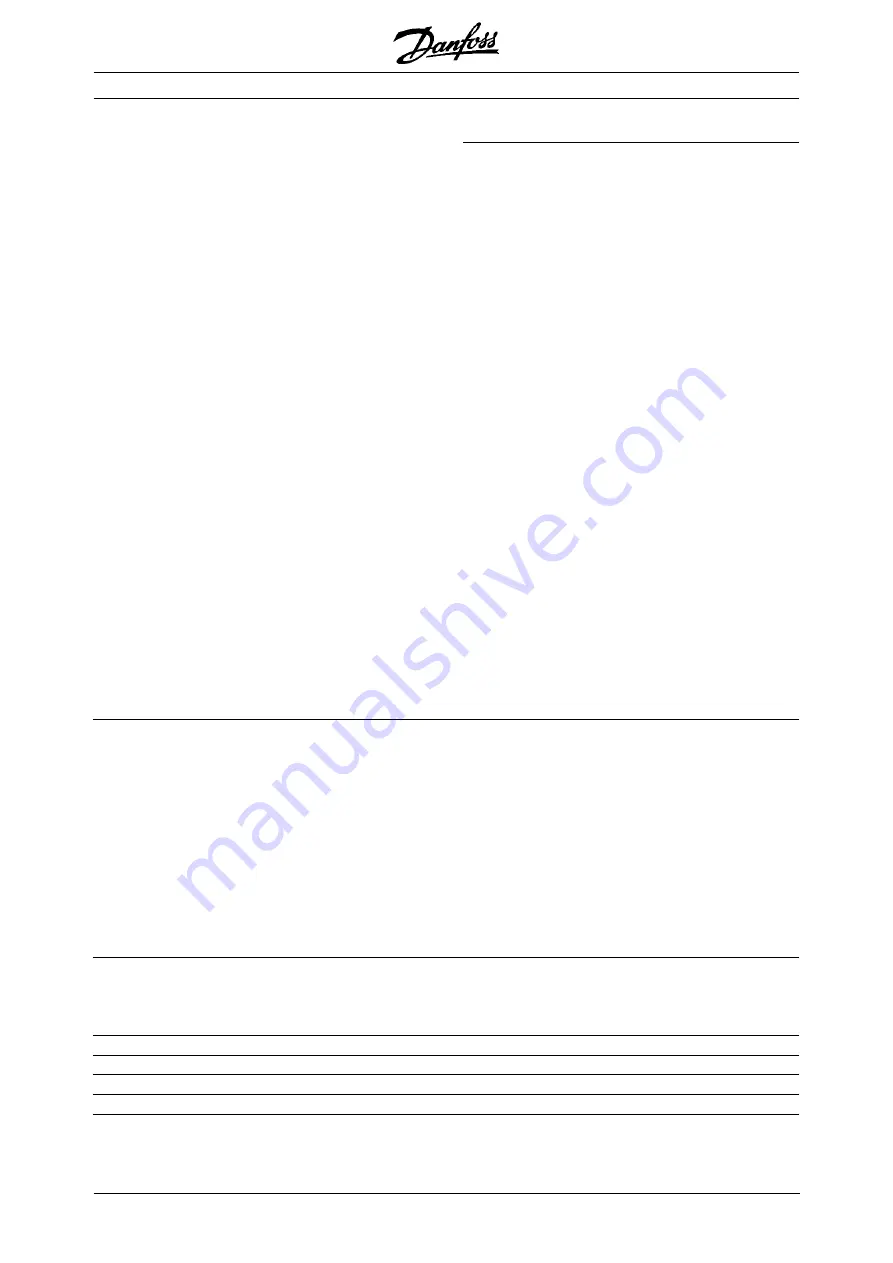
FCM 300 PROFIBUS / VLT 2800 PROFIBUS
MG.90.A2.02 – VLT is a registered Danfoss trademark
5
The PROFIBUS Interface
■
Master controlled Variable Speed Drives (VSD)
The PROFIBUS Field-bus was designed to give you
unprecedented flexibility and command over your
VSD controlled system. The PROFIBUS will perform
as an integrated part of your VLT VSD, giving you
access to all parameters relevant to your application.
The VSD will always act as a slave, and together with
a master it can exchange a multitude of information
and commands. Control signals such as
speed
reference
,
start / stop
of motor,
reverse
operation,
etc. are transmitted from the master in the form of a
telegramme. The VSD acknowledges receipt by
transmitting status signals, such as
running
,
on
reference
,
motor stopped
and so on to the master.
The VSD may also transmit fault indications, alarms
and warnings to the master, such as
Overcurrent
or
Phaseloss
.
The PROFIBUS communicates according to the
PROFIBUS Protocol Standard DIN 19245 parts 1 and
3
. This means that it can communicate with all
masters that comply with this standard, but it does
not necessarily mean that all services available in the
PROFIBUS standard are supported. The
VDI / VDE
3689 PROFIBUS Profile for Variable Speed Drives
is a
subset of PROFIBUS which only supports the
services relevant to speed control applications.
PROFIDRIVE
is an implementation of VDI / VDE 3689
profile created by DANFOSS and a number of other
companies.
Communication partners
In a control system the VSD will always act as a slave,
and as such it may communicate with a single master
or multiple masters depending on the nature of the
application. A master may be a PLC or a PC that is
equipped with a PROFIBUS communication card.
■
Physical layer
The field of application of a field-bus system is
primarily determined by the transmission media and
the physical bus interface selected. The type of bus
cable required for the application and its installation
(physical layer) are particularly important factors, in
addition to the required transmission reliability of the
physical level.
Though a fundamental feature of the PROFIBUS stan-
dard is the possibility of specifying several different
physical interfaces, the standard, at the time of
printing, has allowed for one universal specification
only, namely the EIA Standard RS 485-A, which has
found acceptance both in the field of factory automa-
tion and in several areas of the processing industry.
■
Cable lengths/number of nodes
The maximum cable length in one segment is
depending on the transmission speed. The total cable
length includes drop cables if any. A drop cable is the
connection from the main bus cable to each node if a
T-connection is used instead of connecting the main
bus cable directly to the nodes, see drop cable
length. The table below shows the maximum allowed
cable length and maximum number of nodes/VLT’s
with 1, 2, 3 and 4 bus segments.
Note that a repeater is a node in both of the two
segments it connects. The number of VLT is based on
a single master system. If there are more masters the
number of VLT must be reduced correspondingly.
Max. total bus cable lenght
1 segment:
2 segments:
3 segments:
4 segments:
32 nodes
64 nodes
96 nodes
128 nodes
Transmission
(31 VLT)
(1 repeater, 61 VLT)
(2 repeaters, 91 VLT)
(3 repeaters, 121 VLT)
speed
[m]
[m]
[m]
[m]
9.6-187.5 kBaud
1000
2000
3000
4000
500 kBaud
400
800
1200
1600
1.5 MBaud
200
400
600
800
3 MBaud
100
200
300
400