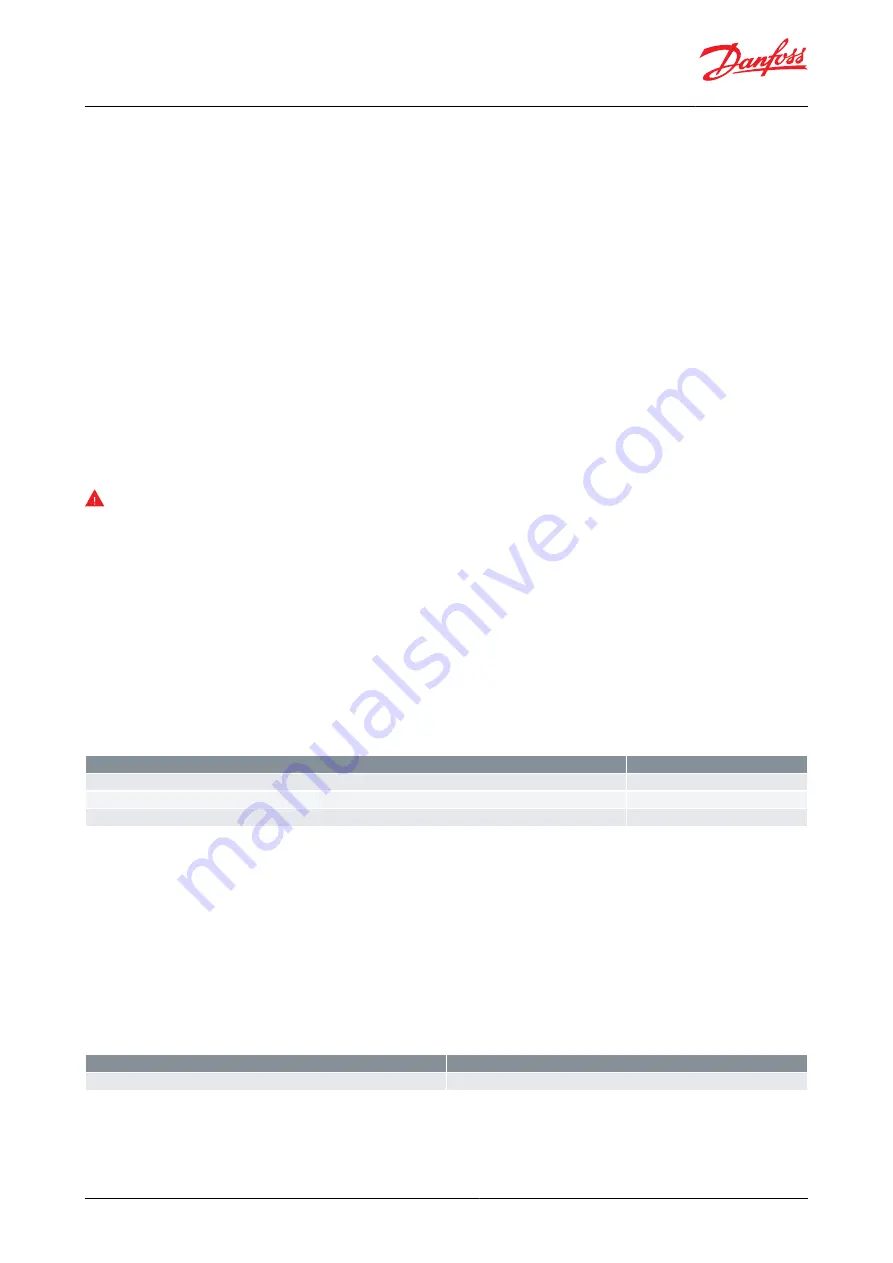
1.
2.
• Apply heat evenly to area
A
until the brazing temperature is reached. Move the torch to area
B
and apply heat
evenly until the brazing temperature has been reached there as well, and then begin adding the brazing material.
Move the torch evenly around the joint, in applying only enough brazing material to flow the full circumference of
the joint.
• Move the torch to area
C
only long enough to draw the brazing material into the joint, but not into the
compressor.
• Remove all remaining flux once the joint has been soldered with a wire brush or a wet cloth. Remaining flux would
cause corrosion of the tubing.
In addition, for discharge connections equipped with a non return valve integrated in discharge fitting the direction
of the torch has to be as described on the picture, and maximum brazing time should be less than 2 minutes to
avoid NRVI damages.
Ensure that no flux is allowed to enter into the tubing or compressor. Flux is acidic and can cause substantial
damage to the internal parts of the system and compressor.
The polyolester oil used in CH compressors is highly hygroscopic and will rapidly absorb moisture from the air. The
compressor must therefore not be left open to the atmosphere for a long period of time. The compressor fitting
plugs shall be removed just before brazing the compressor. The compressor should always be the last component
brazed into the system
Before eventual unbrazing the compressor or any system component, the refrigerant charge must be removed
from both the high- and low-pressure sides. Failure to do so may result in serious personal injury. Pressure gauges
must be used to ensure all pressures are at atmospheric level.
For more detailed information on the appropriate materials required for brazing or soldering, please contact the
product manufacturer or distributor. For specific applications not covered herein, please contact Danfoss for further
information.
System pressure test and leak detection
System pressure test
Always use an inert gas such as nitrogen for pressure testing. Never use other gasses such as oxygen, dry air or
acetylene as these may form an inflammable mixture. Do not exceed the following pressures:
Table 13:
CH290 /CH485
Maximum compressor test pressure (low side)
34.3 bar (g)
Maximum compressor test pressure (high side)
53.6 bar (g)
Maximum pressure difference between high and low side of the compressor
37 bar (g)
Pressurize the system on HP side first then LP side to prevent rotation of the scroll. Never let the pressure on LP side
exceed the pressure on HP side with more than 5 bar.
On CH models which have an internal non return valve in discharge fitting, we advise to pressurize the system not
quicker than 4.8 bar/s to allow pressure equalization between LP and HP side over scroll elements.
Leak detection test
Leak detection must be carried out using a mixture of nitrogen and refrigerant or nitrogen and helium, as indicated
in the table below. Never use other gasses such as oxygen, dry air or acetylene as these may form an inflammable
mixture. Pressurize the system on HP side first then LP side.
Table 14:
Leak detection with refrigerant
Leak detection with a mass spectrometer
Nitrogen and R410A
Nitrogen and Helium
NOTE:
Leak detection with refrigerant may be forbidden in some countries. Check local regulations.
The use of leak detecting additives is not recommended as they may affect the lubricant properties.
© Danfoss | Climate Solutions | 2022.09
AB236986442743en-000501 | 43
Scroll compressors, CH290 and CH485 | Application