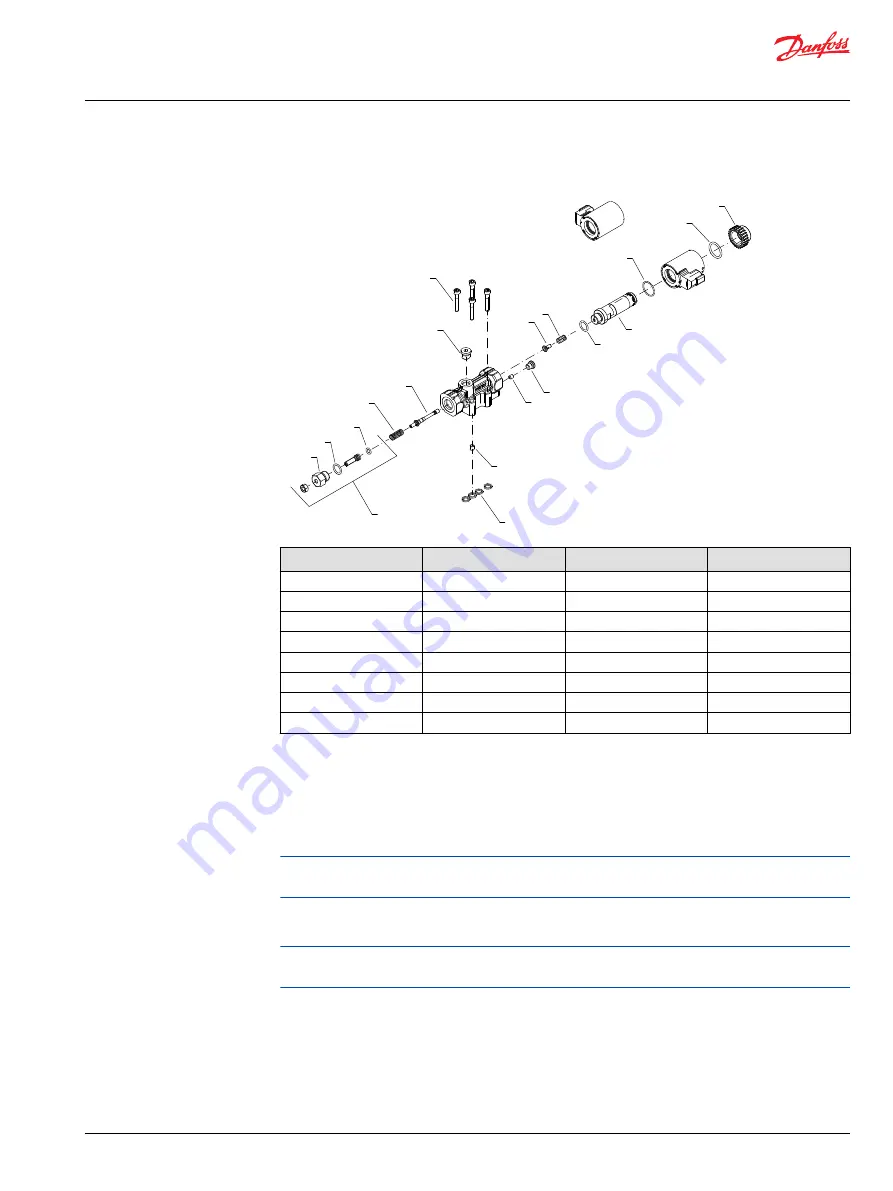
10. Remove servo control orifice (G020).
P109024
Left coil orientation
Right coil orientation
C129
H030
*QC120
C124
C123
G020
QC135
QC130
QC125
C300
C107
C122
C125
C128B
C128A
C128
*C200
C120
C128C
* Included in overhaul seal kit
Item
Description
Wrench size
Torque
G020
Servo control orifice
3 mm internal hex
2.7 N•m [2 lbf•ft]
H030
Gain orifice
2,5 mm internal hex
2.7 N•m [2 lbf•ft]
C129
Plug 5/16"
1/8“ internal hex
6.2 N•m [4.67 lbf•ft]
C107
Plug 7/16"
3/16" internal hex
13.7 N•m [9.9 lbf•ft]
C128C
Nut 9/16"
17 mm exter hex
23.7 N•m [17.5 lbf•ft]
C120
Solenoid cartridge
17 mm exter hex
25.75 N•m [19 lbf•ft]
QC125
Coil plastic nut
26 mm 12 pt socket
3.5 N•m [2 lbf•ft]
C300
Screws
4 mm internal hex
6.5 N•m [4.75 lbf•ft]
Cylinder block Kit disassembly
Disassemble the cylinder block kit
1. Pull to remove the slipper retainer (K049) with the pistons (K050) from the cylinder kit.
The pistons are not selectively fitted, however units with high hourly usage may develop wear
patterns. Number the pistons and bores for reassembly if they are to be reused.
2. Remove the ball guide (K047).
3. Remove the 3 pins (K046).
Most repairs do not require block spring removal. Perform this procedure only if you suspect
problems with the block spring.
Repair Instructions
Series 45 Frame K2 Axial Piston Pumps
Disassembly
©
Danfoss | April 2017
AX00000305en-US0101 | 17