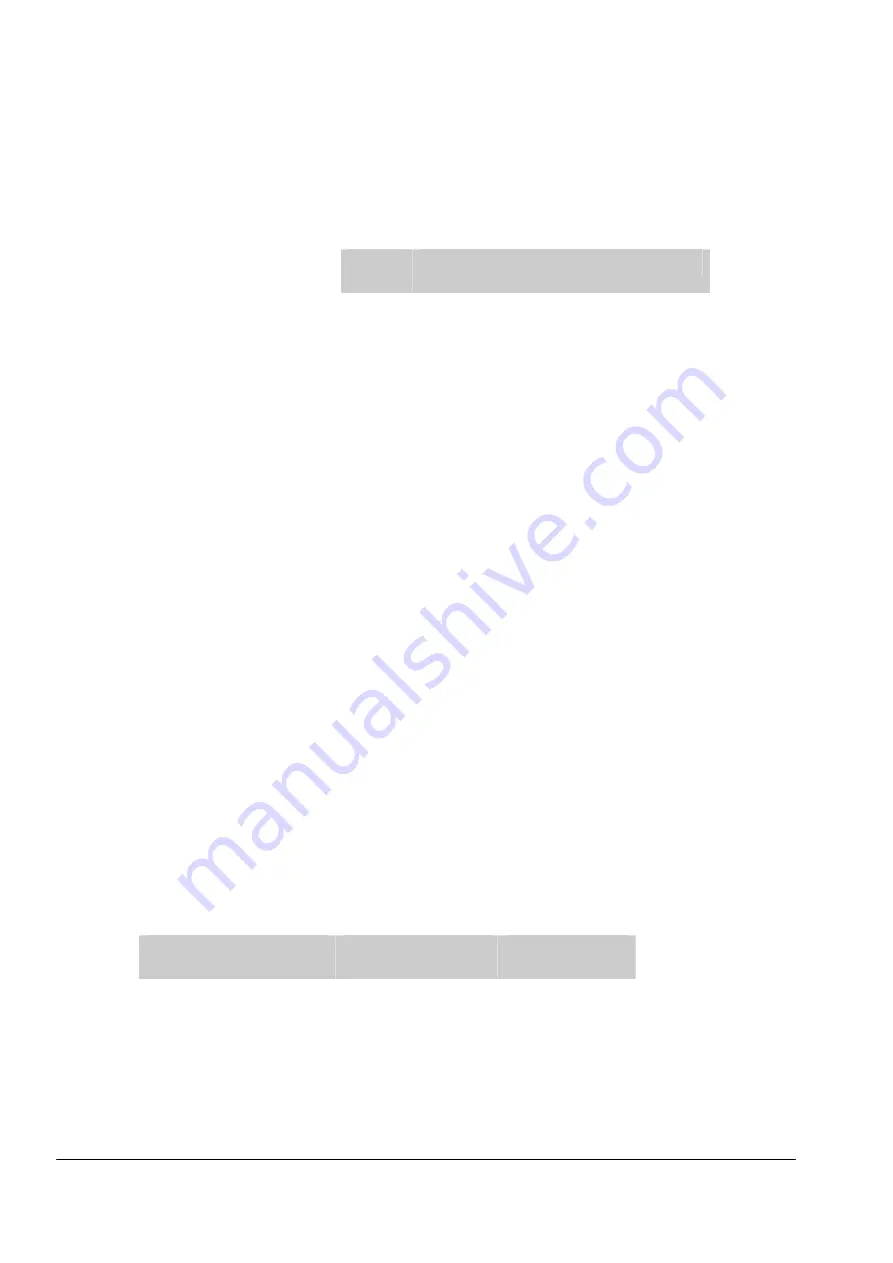
26.04.2005
AC SuperDrive specifications
humidity of 95%.
H
UMIDITY
100% condensing according to IEC68-2-30, Db
C
OOLING
AC S
UPER
D
RIVE WITH FINS
.
6 m/s forced air cooling between fins required for
one hour driving current ratings listed
ACS
Size
Thermal resistance
°
C/W
xx10 0.12
xx15 0.087
xx20 0.067
Cooling
AC SuperDrive flat.
xx25 0.055
8.8 EMC
E
LECTROMAGNETIC
COMPATIBILITY
According to European standard EN12895, Industrial
Trucks (radiated immunity, emission, ESD)
E
LECTRICAL FAST
TRANSIENT
/
BURST
EN61000-4-4 level 2
8.9 S
AFETY AND TESTING STANDARDS COMPLIANCE
S
AFETY
, I
NDUSTRIAL
T
RUCKS
EN
1175-1
B
ASIC
E
NVIRONMENTAL
T
ESTING
P
ROCEDURES
IEC 68-2-30 Damp Heat Cycle
P
ROTECTION CLASS
IP 54 Test IEC 60529 (with mating connector
K1 installed)
8.10 M
ECHANICAL TESTS
V
IBRATION
IEC 68-2-64, test FH, level 2
B
UMP
IEC 68-2-29, test EB
S
HOCK
IEC 68-2-27, test EA
8.11 P
HYSICAL CHARACTERISTICS
8.11.1 W
EIGHT
AC SuperDrive Model
Finned heatsink
Weight Kg
Flat heatsink
Weight Kg
ACSxx 10
4.2
4.3
ACSxx 15
5.9
6.1
ACSxx 20
7.7
8.0
ACSxx 25
9.4
9.7
User's Guide 1.0
Item No.
89Y05120A
95
Summary of Contents for SuperDrive ACS24 Series
Page 12: ......
Page 34: ......
Page 38: ......
Page 79: ...26 04 2005 Troubleshooting guide User s Guide 1 0 Item No 89Y05120A 79...
Page 81: ...26 04 2005 Troubleshooting guide User s Guide 1 0 Item No 89Y05120A 81...
Page 82: ...Troubleshooting guide 26 04 2005 Item No 89Y05120A User s Guide 1 0 82...
Page 92: ......