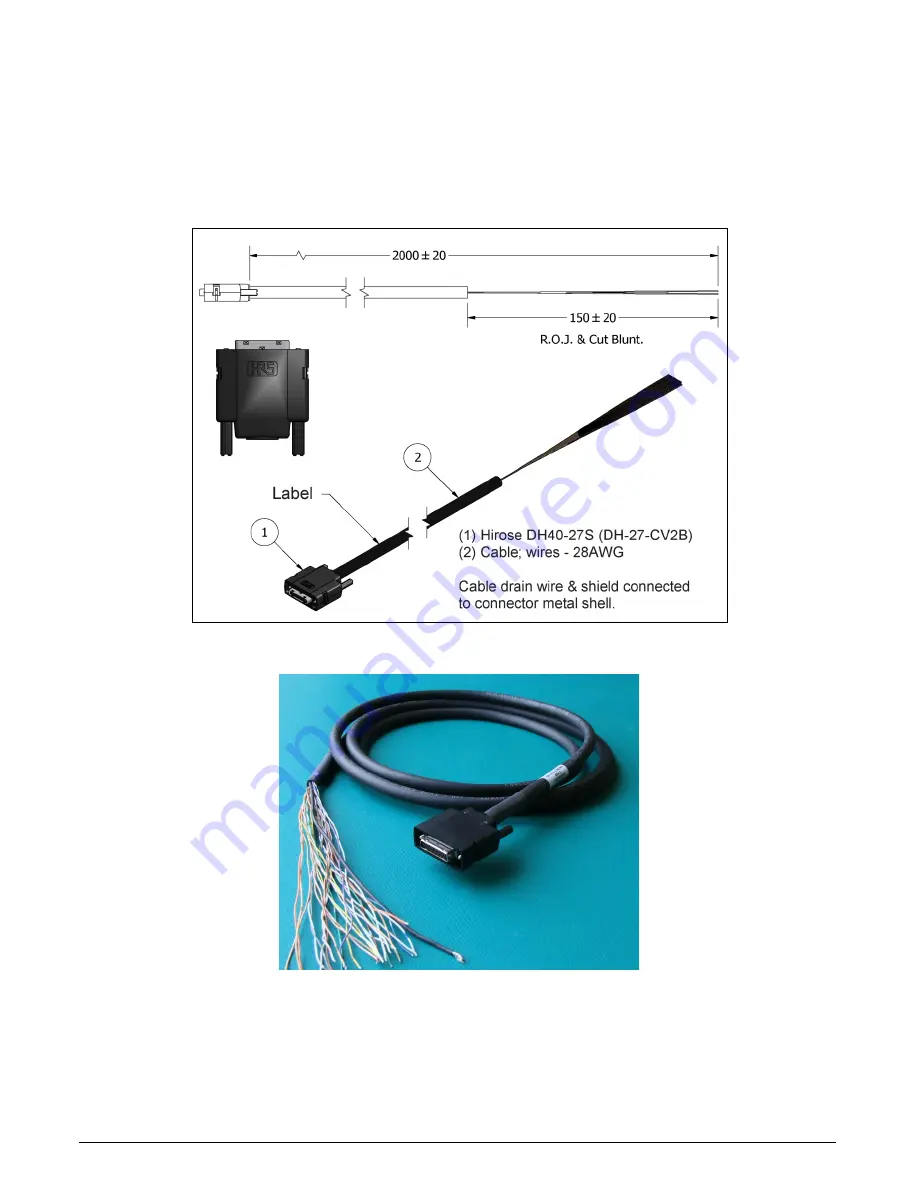
Xtium2-CXP PX8 User's Manual
Technical Specifications
•
121
DH40-27S Cable to Blunt End (OR-YXCC-27BE2M1, Rev B1)
Cable assembly consists of a 2000 mm (~6 ft.) blunt end cable to mate to Xtium external
connector J7. Note: The applicable wiring color-code table is included with the printed Product
Notice shipped with the cable package — no other wiring table should be used.
Important: The older cable part number OR-YXCC-27BE2M0 (rev.3) is obsolete. Do not use with
any Xtium series boards.
Figure 54: DH60-27P Cable No. OR-YXCC-27BE2M1 Detail
Figure 55: Photo of cable OR-YXCC-27BE2M1