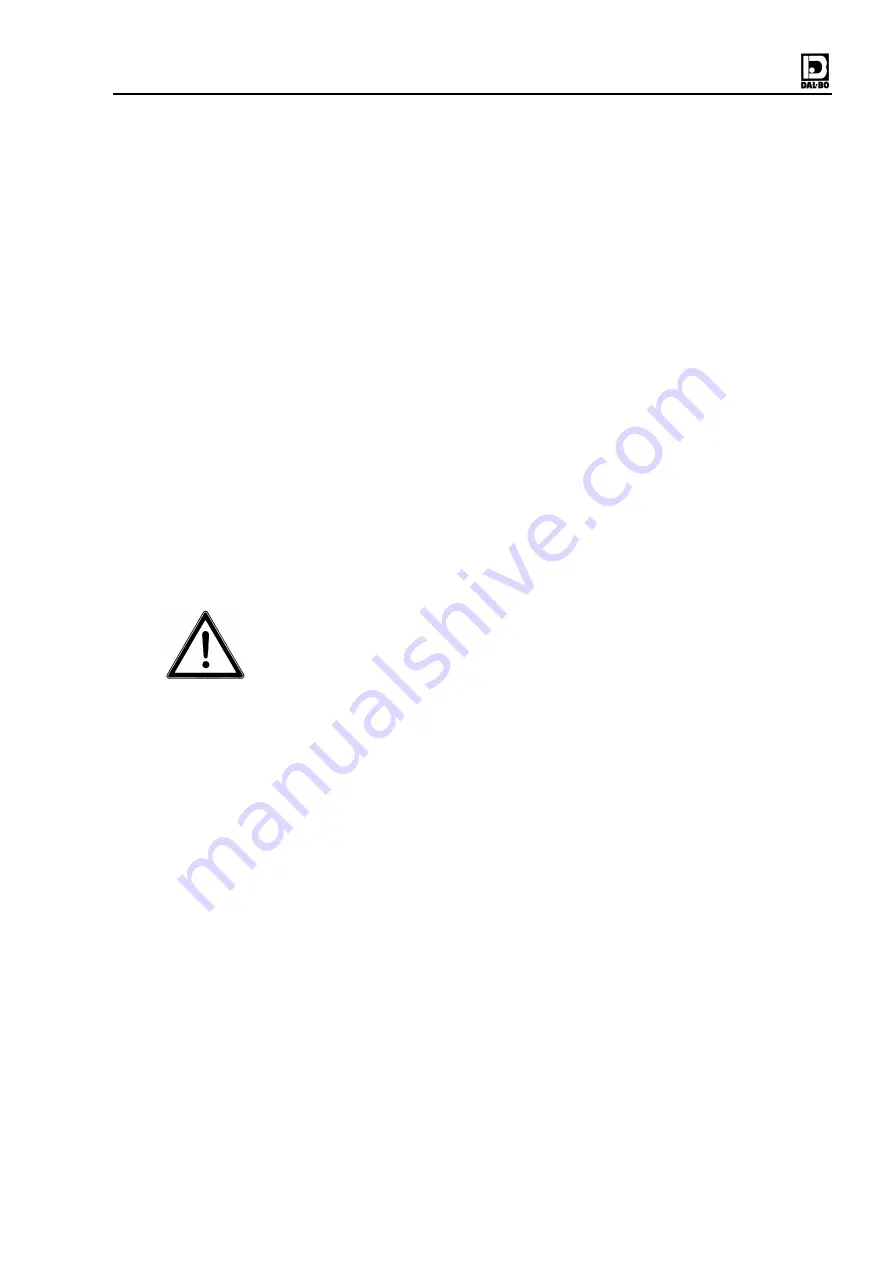
MaxiDisc
Side 11
How to Use This Manual
If the order of points described under the main subject areas of the manual
seems confusing or illogical, refer to the Table of Contents where all subject
headings can be found.
The main points of the operator’s manual are placed into five main categories:
Safety
Set-up and Operation
Options
Maintenance
Repairs
The following safety alert symbols are used throughout this manual to indi-
cate:
Points that are extremely important for the function and life of the machin-
ery.
Points that involve safety.
Delivery
MaxiDisc is delivered fully assembled on a flatbed lorry. The implement may
be partially disassembled for export.
If the MaxiDisc needs to be lifted, it is recommended that you lift with straps
around the middle section, raising the machine so that it hangs in balance.
Summary of Contents for MaxiDisc
Page 1: ...MaxiDisc GB 400 500 600 cm Nr 80005 80010 80020 Serial no 580 xxx ...
Page 2: ......
Page 4: ......
Page 37: ...MaxiDisc Side 37 Hydraulic System Diagram ...
Page 38: ...MaxiDisc Side 38 Spare Parts ...