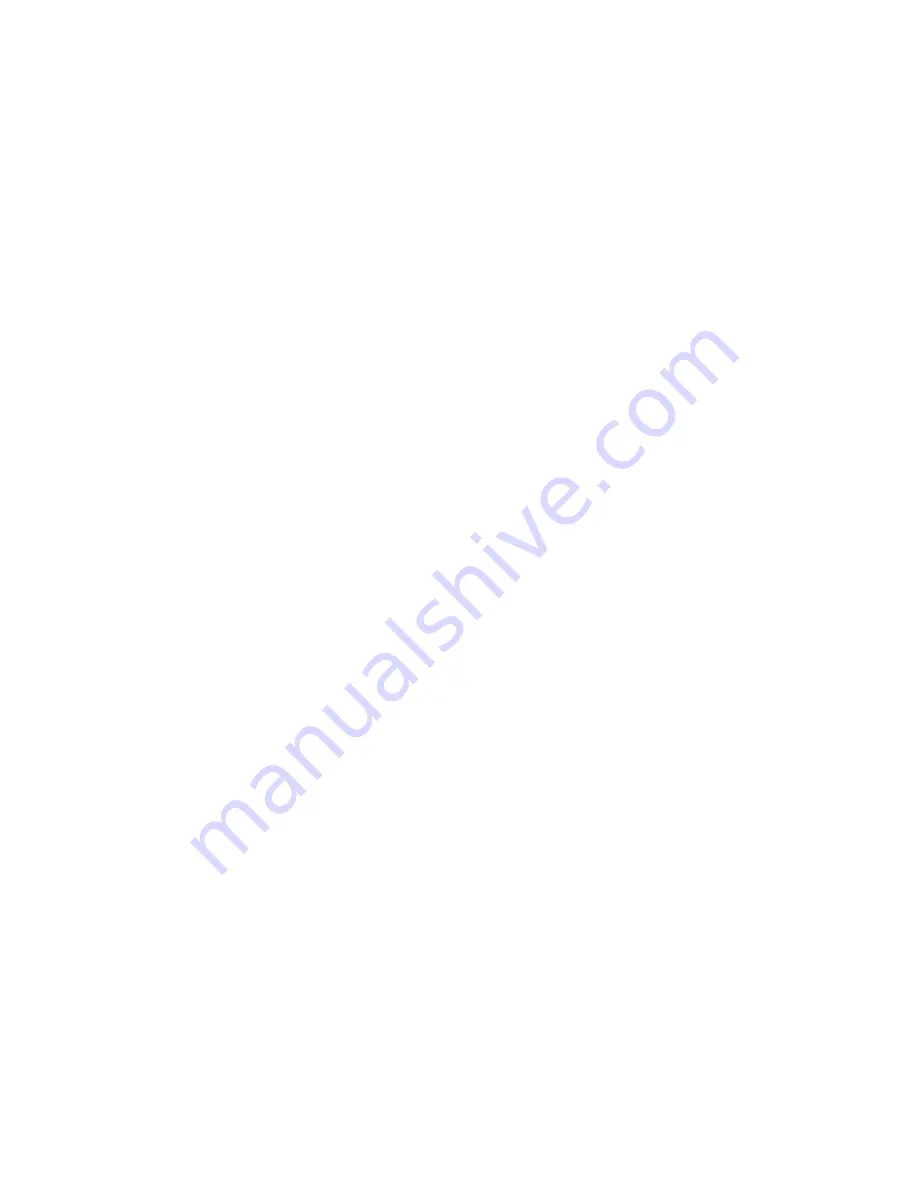
3
properly and perform its intended function. Check for alignment of moving parts, binding of
moving parts. Breakage of parts or mountings and any other conditions that affect its
operation.
SAFETY
1.
Keep guards in place and in working order.
2.
Remove adjusting key and wrenches. Be in the habit of checking to see that keys and
adjusting wrenches are removed from tool before turning it on.
3.
Keep work area clean. Cluttered areas and benches invite accidents.
4.
Do not use in dangerous environments. Do not use power tools in damp or wet
locations or expose them to rain. Keep work area well light.
5.
Do not force tool. It will do the job better and safer at the rate for which it was
designed.
6.
Use the right tool. Do not force the tool, or use the machine to do a job for which it was
not designed.
7.
Wear proper apparel. No loose clothing, gloves, necktie, rings or other jewelry to get
caught in moving parts. Non-slip footwear is recommended. Wear protective hair covering
to contain long hair.
8.
Always use safety glasses. Also use face or dust mask if cutting operation is dusty.
9.
Secure work. Use clamps or a vise to hold work. Do not hold part with hands.
10. Do not overreach. Keep proper footing and balance at all times.
11. Maintain tools with care. Keep tools sharp and clean for best and safest performance.
12. Disconnect drill press from power before servicing, when changing accessories such
as bits, cutter …etc.
13. Never stand on machine, or serious injury could occur.
14.
Never leave machine running unattended.
15.
Be sure drill bit or cutter tool is securely locked in the chuck. Do not hold part to be
machined in hand.
16.
Never place your fingers in a position where they could contact the drill or other cutting
tool if the work piece should unexpectedly shift.
17.
Never perform any operation by moving the head or table with respect to one another.
Do not switch machine on or start any operation before checking that the head and table
lock handles are clamped tight to column, and head and table support collars are correctly
positioned.
WARNING!!!
Extension cords and surge protectors are not recommended for this product.
Ground fault circuit interrupters (GFCI) should not be used. DO NOT TAMPER
WITH WIRING OR SETTINGS INSIDE THE FREQUENCY DRIVE.
Summary of Contents for SB-250V
Page 16: ...14 See page 18...
Page 23: ...21 ELECTRICAL DIAGRAM...