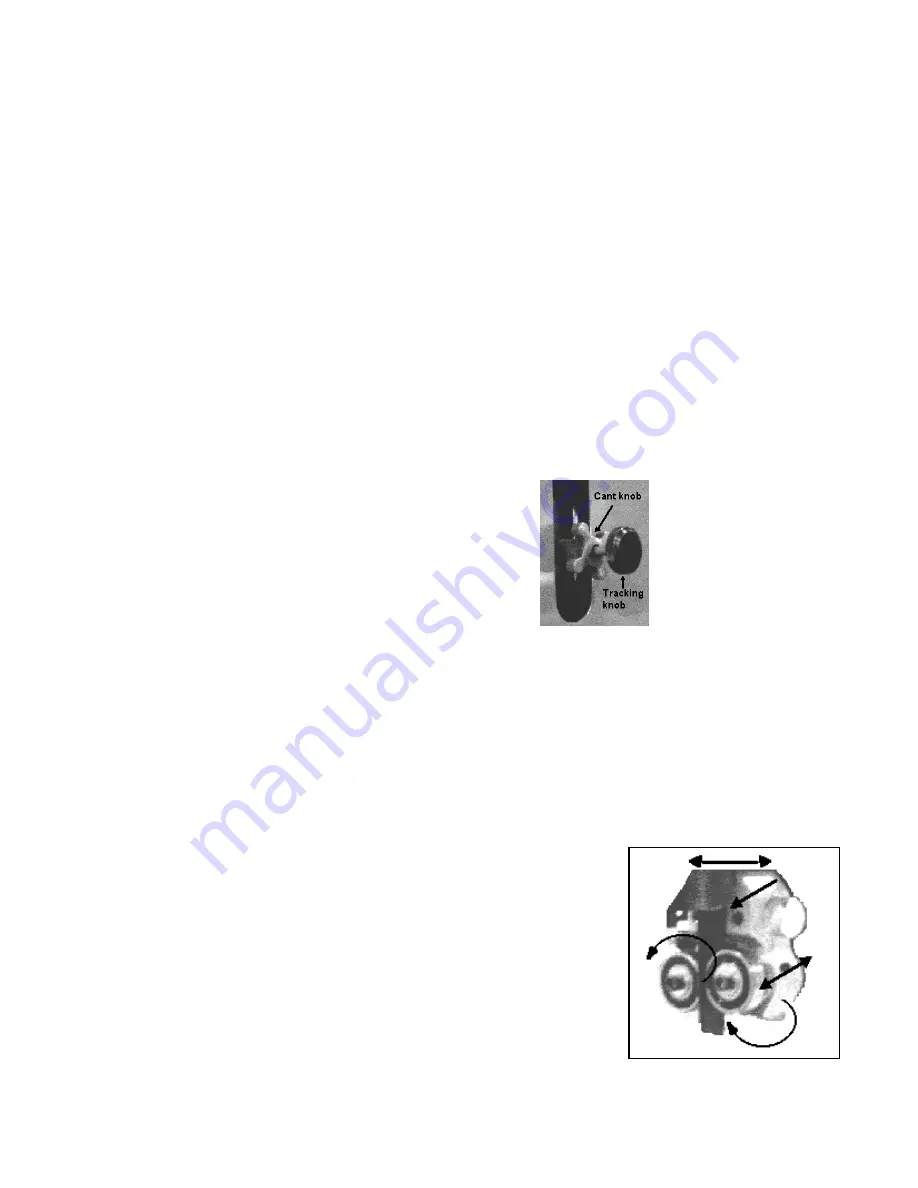
4/29/03
Model Trademaster
Section I -
11
to the degree needed and the miter gauge to the angle needed. When cutting angles or
compound miters, always slow the table feed down.
Notes: When bundle cutting always secure pieces together to prevent parts moving
during the cutting process.
When contour cutting always lock table, and use the narrowest blade possible for the
application, to prevent undo stress to the blade.
Blade tracking and guide adjustments
When a new blade is installed blade tracking may be necessary. The blade should run
as close to center of the band wheel as possible, if the blade is not centered the blade
must be tracked in.
1. Tension blade to manufactures recommendations. (It is better to be over tight than
not tight enough).
2. On the rear of the machine behind the upper wheel loosen the cant knob.
3. Adjust the center-tracking knob in or out to track the blade. Note: Make only half
turns at a time, and jog the machine as you go to check tracking.
4. After tracking is completed tighten cant knob.
Blade guide adjustment should be done from time
To time to insure the blade is being properly supported.
The guides are adjustable in five different ways.
1. The roller adjustment to loosen from the blade.
2. The roller adjustment to tighten against the blade.
3. The roller adjustment in and out for blade widths.
4. The top roller in / out side to side for support of the blades back, for centering blade
groove.
The blade must run straight through the guides without any twist or misalignment from
the upper to the lower guides. The top roller has a shallow groove in it and the
back edge of the blade is to run through this groove. The roller can be moved left or
right by loosening the setscrew and shifting the roller. The top and bottom must be in
line with each other. The back of the blade should just touch this roller. If it does not or
is too close where it bows the blade outward it must be adjusted. By loosening the
setscrew, the knurled knob can be turned to make this adjustment.
The lower rollers can be adjusted to put pressure on the blade
sides. This is done by loosening the setscrews and rotating the
eccentric axle. There should be approx. .004 of gap between
these rollers and the blade.
If you change the blade width the lower rollers (both on upper
and lower guide sets) must be adjusted accordingly. By
loosening the setscrews move the rollers so they are just
behind the blades teeth gullets. The roller must not contact the
set of the teeth.
Note: Keep the guides clean and free from chips.