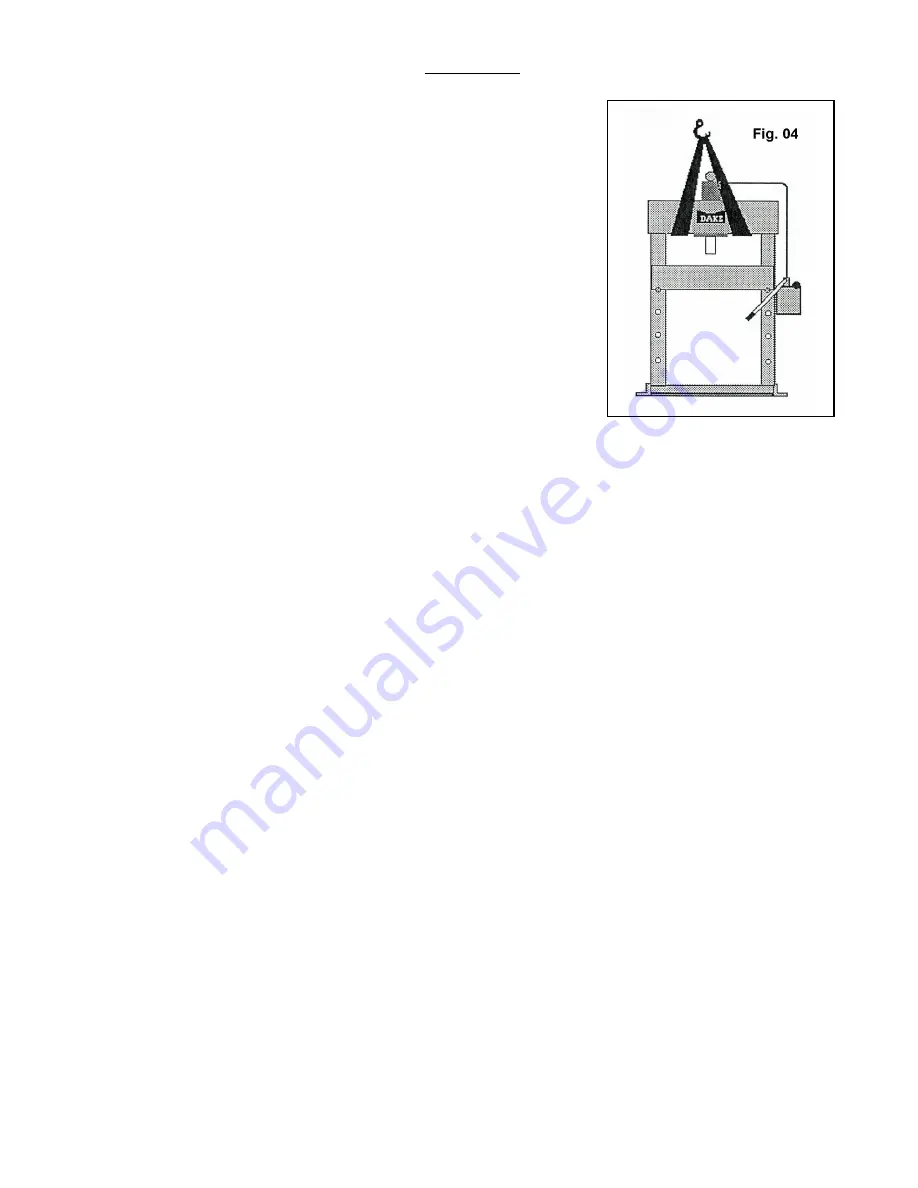
Force 10M /Force 20M13
13
06/10
Section 4.0
4.0 HANDLING, TRANSPORT AND POSITIONING
For handling the packed machine, as described above
(see section 3.0), it is necessary to use special lifting
equipment whose maximum lifting capacity must be no
lower than the total weight of the press.
THE TOTAL WEIGHT OF THE PRESS PLUS PACKING
IS SHOWN ON THE ADHESIVE TABS PLACED ON
THE PACKING AND ON THE ACCOMPANYING
DOCUMENTS.
For loading and unloading the machine, lifting straps are
to be used positioned as shown in Fig. 04.
4.1 NOTICES FOR HANDLING AND TRANSPORT
Loading and unloading will have to be done with lifting straps in conformity with and
according to the instructions of the above paragraph,
in addition check:
Check that the straps are made in conformity with safety regulations and they
have attached the relative plates certifying they are in conformity with the standards.
CHECK THAT THE MAXIMUM CAPACITY OF EACH STRAP IS GREATER
THAN THE TOTAL WEIGHT OF THE PRESS.
Check that the straps are in a good state of repair.
It is forbidden for things and/or persons to stand close to the machine, the
unloading or loading area, and the means of transport during the loading and
unloading phases.
Do not make any sudden movements with the lifting equipment while lifting or
lowering the load.
Pay the utmost attention during all handling operations so that the press and in
particular the hydraulic power unit does not get damaged.
Observe the in-house provisions concerning lifting and handling.
IT IS FORBIDDEN TO APPROACH OR PASS UNDER HANGING LOADS.
THE MANUFACTURER DECLINES ALL LIABILITY FOR ANY DAMAGE CAUSED
BY ANY ACTION DURING THE PHASE OF UNLOADING AND LOADING THE
PRESS.