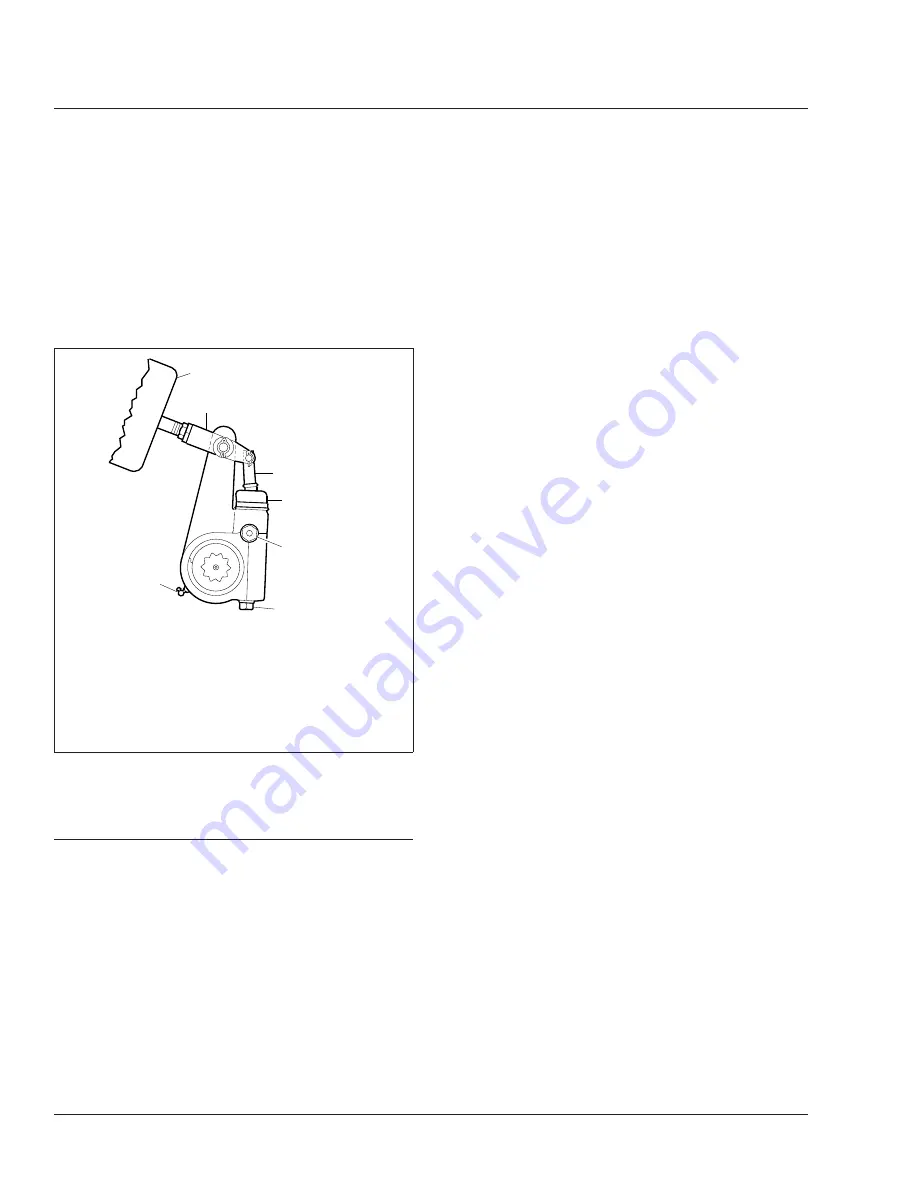
For slack adjusters with grease fittings and for oper-
ating temperatures below –40°F (–40°C) and above
–65°F (–54°C), use an NLGI Grade 2 synthetic oil,
clay-base grease.
Lubricate the slack adjuster at the grease fitting until
grease is forced past the pressure-relief capscrew or
past the gear splines around the inboard snap ring.
See
42–08 Air Dryer AD–9, AD–IP,
AD–IS/DRM Check
IMPORTANT: Review the warranty policy before
performing any intrusive maintenance proce-
dures. An extended-warranty may be voided if
intrusive maintenance is performed during this
period.
Because no two vehicles operate under identical
conditions, maintenance and maintenance intervals
will vary. Experience is a valuable guide in determin-
ing the best maintenance interval for any one particu-
lar operation.
Every 900 operating hours, or 25,000 miles (40 225
km), or 3 months:
1.
Check for moisture in the air brake system by
opening reservoir drain valves and checking for
the presence of water. If moisture is present, the
desiccant cartridge may require replacement;
however, the following conditions can also cause
water accumulation and should be considered
before replacing the desiccant:
1.1
An outside air source has been used to
charge the system. This air did not pass
through the drying bed.
1.2
Air usage is exceptionally high and not
normal. This may be due to high air sys-
tem leakage.
1.3
In areas where more than a 30-degree
range of temperature occurs in one day,
small amounts of water can temporarily
accumulate in the air brake system due to
condensation. Under these conditions, the
presence of small amounts of moisture is
normal.
NOTE: A small amount of oil in the system is
normal and should not be considered as a rea-
son to replace the desiccant cartridge. Some oil
at the dryer exhaust is normal.
2.
Visually check for physical damage such as
chaffed or broken air and electrical lines and bro-
ken or missing parts.
3.
Check mounting bolts for tightness. Torque 30 to
35 lbf·ft (41 to 47 N·m).
4.
Perform the operational and leakage tests listed
below.
Operational and Leakage Tests
1.
Check all lines and fittings leading to and from
the air dryer for leakage and integrity. Repair any
leaks found.
2.
Build system pressure to governor cutout, and
note that the dryer purges with an audible es-
cape of air. Watch the system pressure and note
the pressure fall-off for a 10-minute period. If the
pressure drop exceeds 1 psi/minute from either
service reservoir for a single vehicle; or 3
psi/minute for a tractor trailer, inspect the vehicle
air systems for sources of leakage, and repair
f420012a
10/20/93
1
2
3
4
5
6
7
1.
Brake Chamber
2.
Clevis
3.
Actuator Rod
4.
Boot
5.
Pressure-Relief Capscrew, Gasket, Pawl Spring,
and Pawl
6.
Manual Adjusting Nut
7.
Grease Fitting (or plug)
Fig. 8, Meritor Automatic Slack Adjuster
Brakes
42
Business Class M2 Maintenance Manual, November 2015
42/8
Property of American Airlines