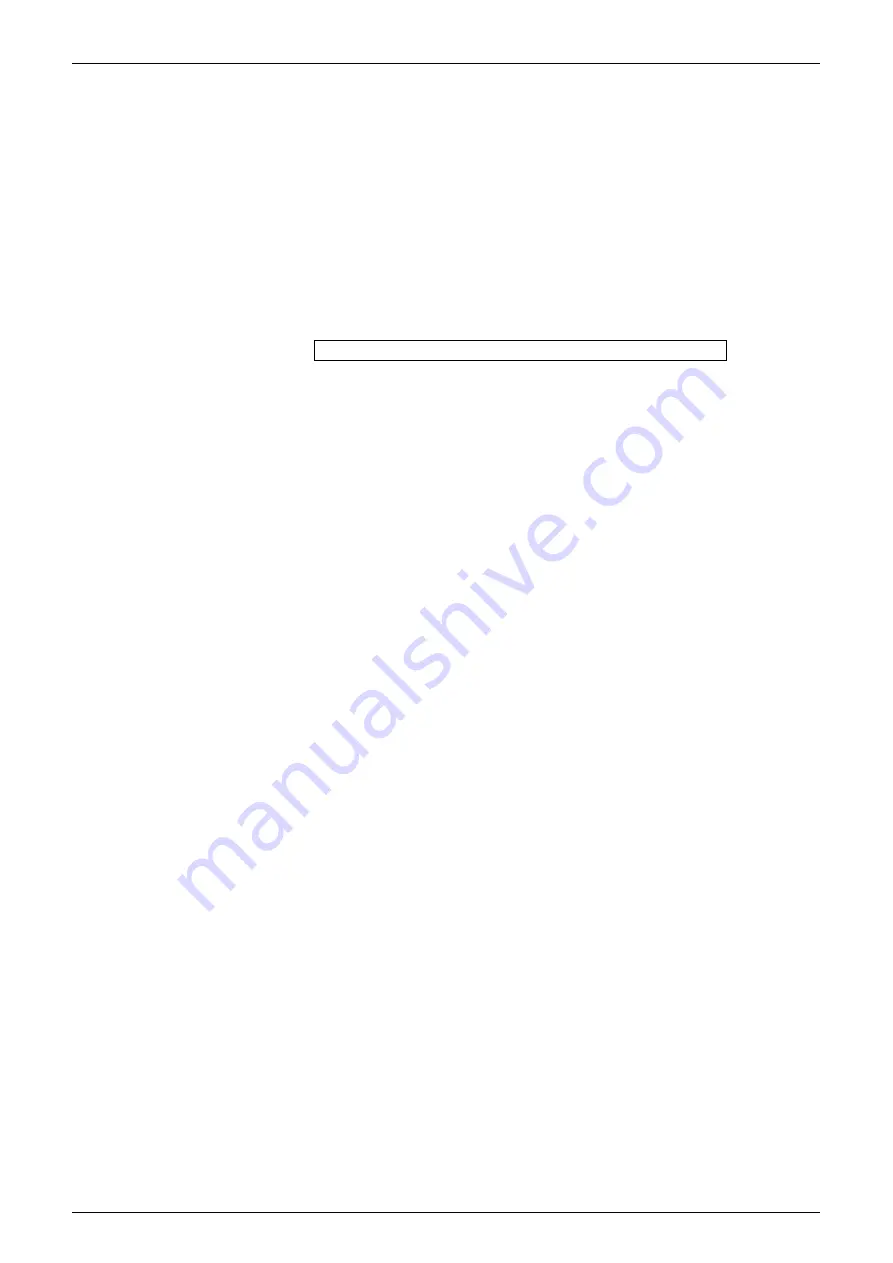
Si50-203
Overhaul
Semi-Hermetic Single Screw Compressor Version III
3
2.
Overhaul
Generally, maintenance and inspection of equipment are important in preventing their failure
and damage to them. Equipment, even without defective structure or components, gradually
age and wear over long years of operation. For example, screw compressors, despite their
apparent good operating condition, may face such problems as decreasing insulation resistance
of the motor, oil deterioration, and worn and fatigued bearings during long periods of operation.
Most of such changes with time are invisible from the outside in many cases, and it is only after
an accident that they are noticed. For this reason, in the case of equipment required to be
highly reliable, it is most important to grasp their wear condition precisely and take necessary
measures against accidents if they are to maintain proper operating conditions for expanding
service life.
Overhaul interval: 40,000 hours or 7 years, whichever comes first.
Summary of Contents for ZH(C)3LSF
Page 48: ...Si50 203 ii Index...