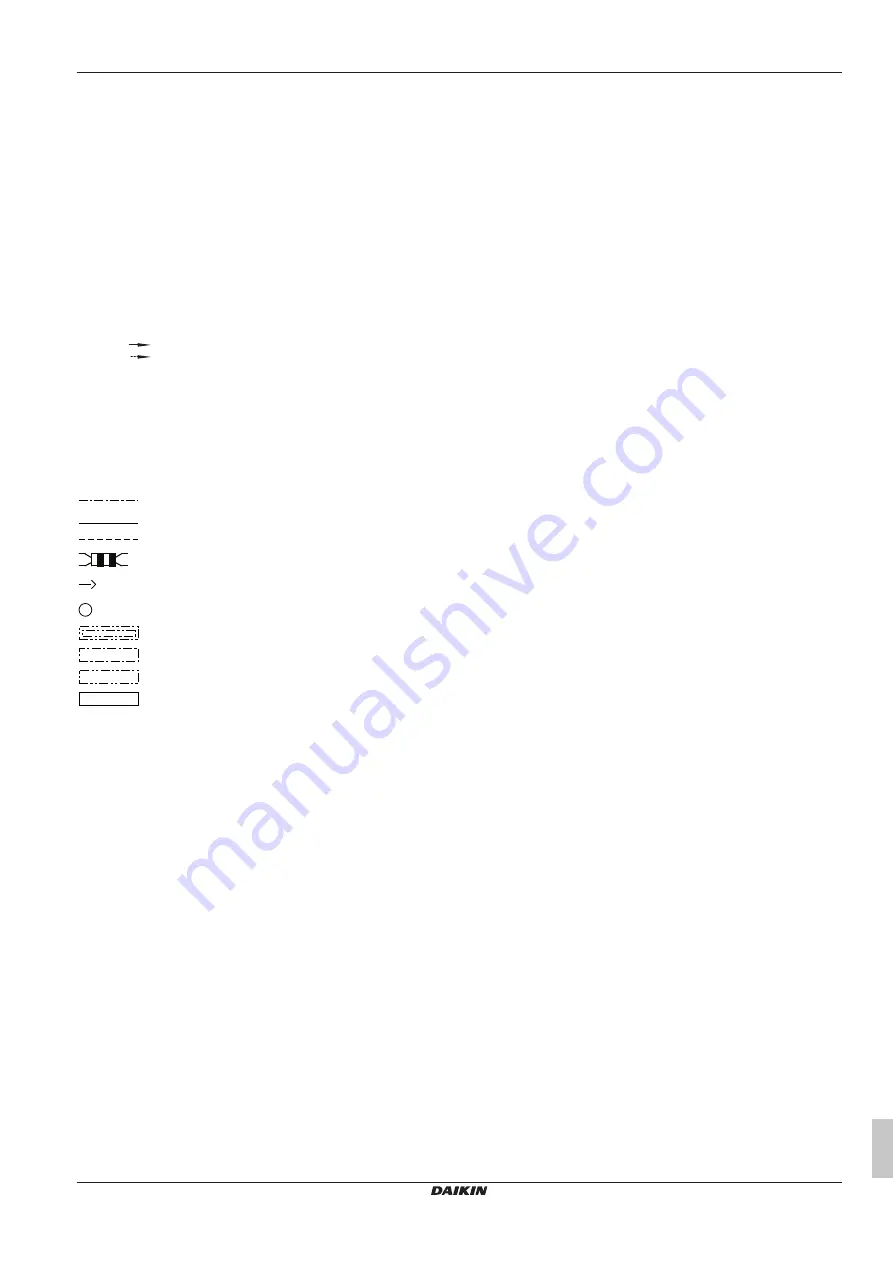
20 Technical data
Installation and operation manual
43
RK RKXYQ8T7Y1B
VRV IV compressor unit for indoor installation
4P499900-1B – 2021.12
g
Subcool heat exchanger
h
Pressure regulating valve
i
Capillary tube
j
Accumulator
k
Oil separator
l
Heat exchanger
M1C
Compressor
M1F~M3F
Fan motor
R1T (A)
Thermistor (air)
R2T (A)
Thermistor (gas)
R3T (A)
Thermistor (coil)
R21T (B)
Thermistor (discharge)
R3T (B)
Thermistor (suction accumulator)
R5T (B)
Thermistor (liquid)
R6T (B)
Thermistor (subcool heat exchanger gas)
R7T (B)
Thermistor (suction compressor)
S1NPH
High pressure sensor
S1NPL
Low pressure sensor
S1PH
High pressure switch
Y1E, Y2E
Electronic expansion valve
Y1S
Solenoid valve (4‑way valve)
Heating
Cooling
20.2
Wiring diagram: Compressor unit
The wiring diagram is delivered with the unit, located on the switch
box cover.
Symbols:
X1M
Main terminal
Earth wiring
15
Wire number 15
Field wire
Field cable
**
/12.2
Connection ** continues on page 12 column 2
1
Several wiring possibilities
Option
Not mounted in switch box
Wiring depending on model
PCB
Legend for wiring diagram 5 HP:
A1P
Printed circuit board (main)
A2P
Printed circuit board (inverter)
BS*
Push button (A1P)
C*
Capacitor (A2P)
DS1
DIP switch (A1P)
F1U, F2U
Fuse (T 31.5 A / 250 V) (A1P)
F3U, F5U
Fuse (T 6.3 A / 250 V) (A1P)
H*P
LED (service monitor orange) (A1P)
HAP
Running LED (service monitor green) (A*P)
K1M
Magnetic contactor (A2P)
K1R
Magnetic relay (A*P)
L1R
Reactor
M1C
Motor (compressor)
M1F
Motor (fan)
PS
Switching power supply (A2P)
Q1DI
Earth leakage circuit breaker (field supply)
R*
Resistor (A2P)
R2T
Thermistor (discharge)
R3T
Thermistor (suction accumulator)
R4T
Thermistor (subcool heat exchanger gas)
R5T
Thermistor (suction compressor)
R7T
Thermistor (liquid)
R10T
Thermistor (fin)
S1NPL
Low pressure sensor
S1NPH
High pressure sensor
S1PH
High pressure switch
S*S
Cool/heat selector switch (optional)
V1R
IGBT power module (A2P)
V2R
Diode module (A2P)
X1M
Terminal strip (power supply)
X2M
Terminal strip (transmission wiring)
X*Y
Connector
Y3E
Electronic expansion valve
Y1S
Solenoid valve (4‑way valve)
Z*C
Noise filter (ferrite core)
Z*F
Noise filter (A1P)
Notes for 8 HP:
1
When using the optional adapter, refer to the installation
manual of the optional adapter.
2
Refer to the installation or service manual on how to use
BS1~BS3 push buttons, and DS1+DS2 DIP switches.
3
Do not operate the unit by short-circuiting protection device
S1PH.
4
For connection of INDOOR-OUTDOOR F1-F2 transmission
wiring, and OUTDOOR-OUTDOOR F1-F2 transmission
wiring, refer to the service manual.
Legend for wiring diagram 8 HP:
A1P
Printed circuit board (main)
A2P
Printed circuit board (noise filter)
A3P
Printed circuit board (inverter)
A4P
Printed circuit board (cool/heat selector)
BS*
Push button (mode, set, return) (A1P)
C*
Capacitor (A3P)
DS*
DIP switch (A1P)
E1HC
Crankcase heater
F*U
Fuse (T 3.15 A / 250 V) (A1P)
F3U
Field fuse
F400U
Fuse (T 6.3 A / 250 V) (A2P)
F410U
Fuse (T 40 A / 500 V) (A2P)
F411U
Fuse (T 40 A / 500 V) (A2P)
F412U
Fuse (T 40 A / 500 V) (A2P)
HAP
Running LED (service monitor green) (A1P)
K1M
Magnetic contactor (A3P)
K*R
Magnetic relay (A*P)
L1R
Reactor
M1C
Motor (compressor)
M1F
Motor (fan)
PS
Power supply (A1P, A3P)
Q1DI
Earth leakage circuit breaker (field supply)
Q1RP
Phase reversal detect circuit (A1P)
R21T
Thermistor (M1C discharge)
R3T
Thermistor (accumulator)
R5T
Thermistor (subcool liquid pipe)
R6T
Thermistor (heat exchanger gas pipe)
R7T
Thermistor (suction)
R*
Resistor (A3P)