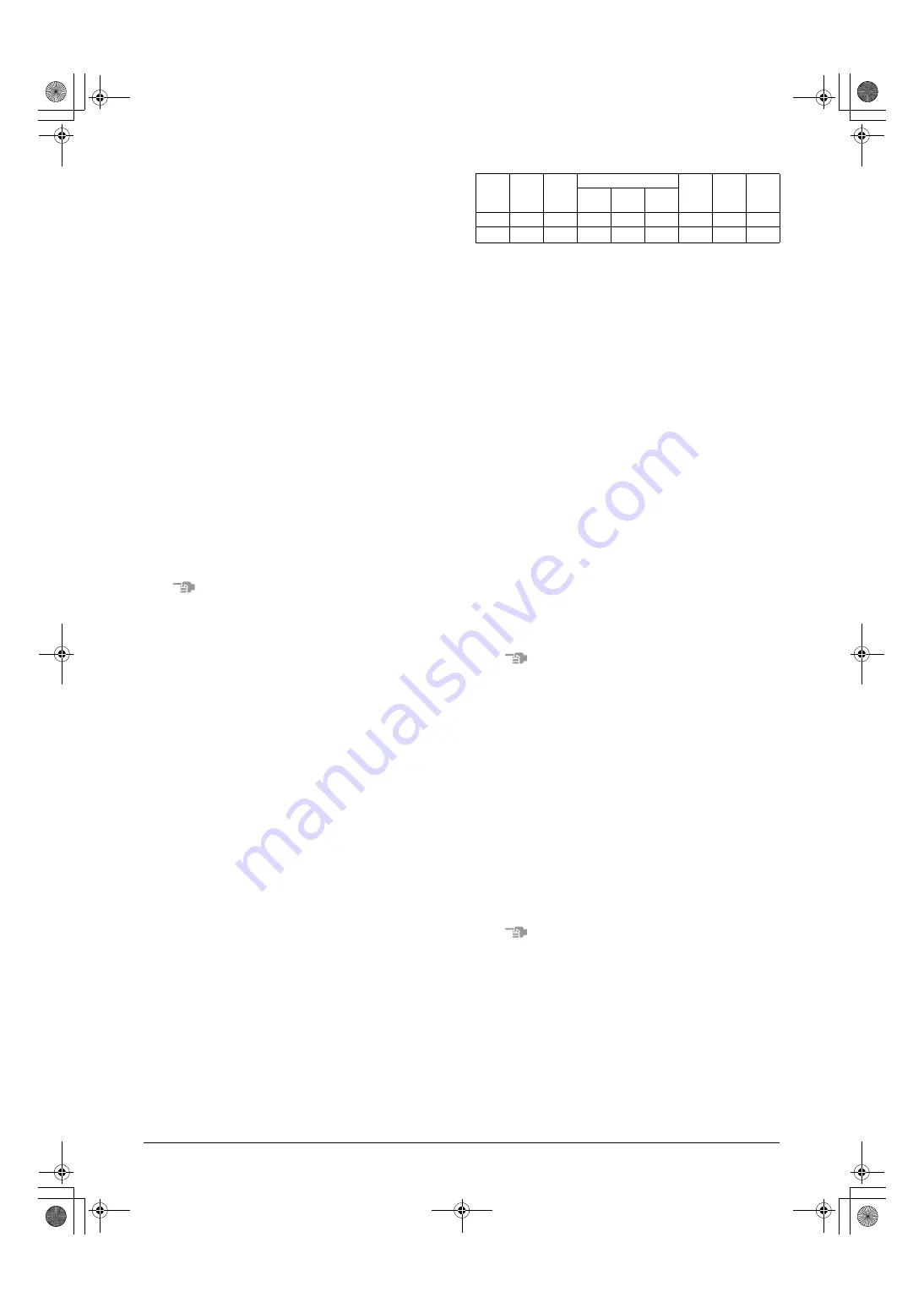
English
14
3.
Open the valve B (
See the figure 30
. The valve A,C and the liquid
pipe, suction gas pipe, HP/LP gas pipe shutoff valves must be left
closed), and charge the refrigerant of the “additional charging
amount” from the liquid side shutout valve service port.
(Refer to figure 30)
1.
Measuring device
2.
R410A tank (with siphon)
3.
Charge hose
4.
Refrigerant charge port
5.
HP/LP gas pipe shutoff valve
6.
Suction gas shutoff valve
7.
Liquid pipe shutoff valve
8.
Valve A
9.
Valve B
10.
Valve C
11.
Outdoor unit
12.
To BS, indoor unit
13.
Field pipings
14.
Refrigerant flow
15.
Shutoff valve
16.
Service port
4.
If the “additional charging amount” was charged fully, close the
valve B and go to step 6.
If the “additional charging amount” was not charged fully, close
the valve B and go to step 5.
5.
Perform the refrigerant charging operation following [Refrigerant
charging operation procedure] as shown below, and charge the
remaining refrigerant of the “additional charging amount”. For per-
forming the refrigerant charging operation the push button on the
PC-board (A1P) of outdoor unit are use. (See the figure 29) In
addition, the refrigerant are charged from the refrigerant charge
port via the valve A. (See the figure 31)
For operating the push button and opening and closing the valve,
follow the work procedure.
Note
The refrigerant will be charged about 30kg in one hour at outdoor
temp. 30°C DB (12kg at 0°C DB).
(Refer to figure 31)
1.
Measuring device
2.
R410A tank (with siphon)
3.
Charge hose
4.
Refrigerant charge port
5.
HP/LP gas pipe shutoff valve
6.
Suction pipe shutoff valve
7.
Liquid pipe shutoff valve
8.
Valve A
9.
Valve B
10.
Valve C
11.
Outdoor unit
12.
To BS, indoor unit
13.
Field pipings
14.
Refrigerant flow when charging
15.
Shutoff valve
16.
Service port
[Refrigerant Charging Operation Procedure]
(1) Open the liquid pipe, suction gas pipe, HP/LP gas pipe and equal-
izer pipe shutoff valves (The valve A~C must be closed. The valve
A~C means the valves in the figure 31.)
(2) • Close the EL. COMPO. BOX (1) (right) lid and all front panel
except on the side of the EL. COMPO. BOX (1) (right) (*1) and
turn the power to the outdoor unit and all connected indoor
units. (*2)
• After H2P stop blinking (about 12 minutes after turning on the
power), check LED displays as shown in Table : Display of nor-
mal system and the system is normal state.
If H2P is blinking, check the malfunction code in the remote
controller, and correct the malfunction in accordance with
[Remote controller display malfunction code] in chapter 11-2-2.
(*1) Lead the refrigerant charge hose etc from the pipe intake. All
front panels must be closed at the procedure (3).
(*2) • If you perform the refrigerant charging operation within the
refrigerant system that have the power off unit, the operation
cannot finish properly.
For confirming the number of the outdoor and indoor units with
the power on, see [How to check how many units are con-
nected] in chapter 11-1.
• To energize the crankcase heater, make sure to turn on for 6
hours before starting operation.
Table : Display of normal system
(3) Charge the remained refrigerant by additional refrigerant charg-
ing operation of service mode.
About the method of additional refrigerant charging operation,
refer to the [Service Precaution] labe (lower) attached on the EL.
COMPO. BOX lid of the outdoor unit.
(Refer to figure 32)
1.
EL. COMPO.BOX (1) (right) lid
2.
EL. COMPO.BOX (2) (left)
3.
[Service Precaution] label (upper)
4.
[Service Precaution] label (lower)
(4) Close the valve A if the “additional charging amount” of refrigerant
was charged, and push the RETURN button (BS3) once.
6.
After completing the additional refrigerant charging, record the
charging amount on the accessory “REQUEST FOR THE INDI-
CATON” label (Installation records) and adhere it to the back side
of the front panel. Also, record the factory charged refrigerant
amount, additional refrigerant amount in the field and total refrig-
erant amount of the system to “ADDITIONAL REF. CHARGE”
label and adhere in the proximity of the refrigerant charge port.
About “ADDITIONAL REF. CHARGE” label, refer to [Important
information regarding the refrigerant used] in
“1-2 Special notice
of product”
.
11-2-2 Procedure of check operation
•
Check operation perform the following work. Do the check opera-
tion following below.
Otherwise, malfunction code “U3” will be displayed in the remote
controller and nomal operation can not be carried out.
Check of shutoff valve opening
Check of miswiring
Judgment of piping length
Check of refrigerant overcharge
Note
•
Check operation can not carried out at outdoor temp. less than –5°C.
Perform the check operation at day or time that outdoor temp. is –5°C
or more.
[Check Operation Procedure]
(1) Close the EL. COMPO. BOX (1) lid and all front panels except as
the side of the EL. COMPO. BOX (1) and turn on the power to the
outdoor unit and all connected BS, indoor units. (Be sure to turn
the power on at least 6 hours before operation in order to have
power running to the crank case heater.)
(2) Make the onsite settings as needed using the push button (BS1-
BS5) on the outdoor unit PC-board (A1P) with the power on. (See
“12. ONSITE SETTINGS”
)
(3) Perform the check operation following the Check Operation Method of
the [Service Precautions] label (lower) on the EL. COMPO. BOX (1)
lid (see figure 32). The system operation for about 40~60 minutes and
automatically stops the check operation.
If the malfunction code is not displayed in the remote controller after
the system stop, check operation is completed. Normal operation will
be possible after 5 minutes. If the malfunction code is displayed in the
remote controller, correct the malfunction following [Remote controller
displays malfunction code] and perform the check operation again.
Note
For interrupting the check operation, push RETURN button (BS3).
SERV.
MONI-
TOR
MODE
TEST/
HWL
C/H SELECTOR
L.N.O.P DEMAND MULTI
IND
MASTER SLAVE
HAP
H1P
H2P
H3P
H4P
H5P
H6P
H7P
H8P
j
h
h
i
h
h
h
h
h
01_EN_3P201178-3B.fm Page 14 Friday, May 18, 2007 5:21 PM