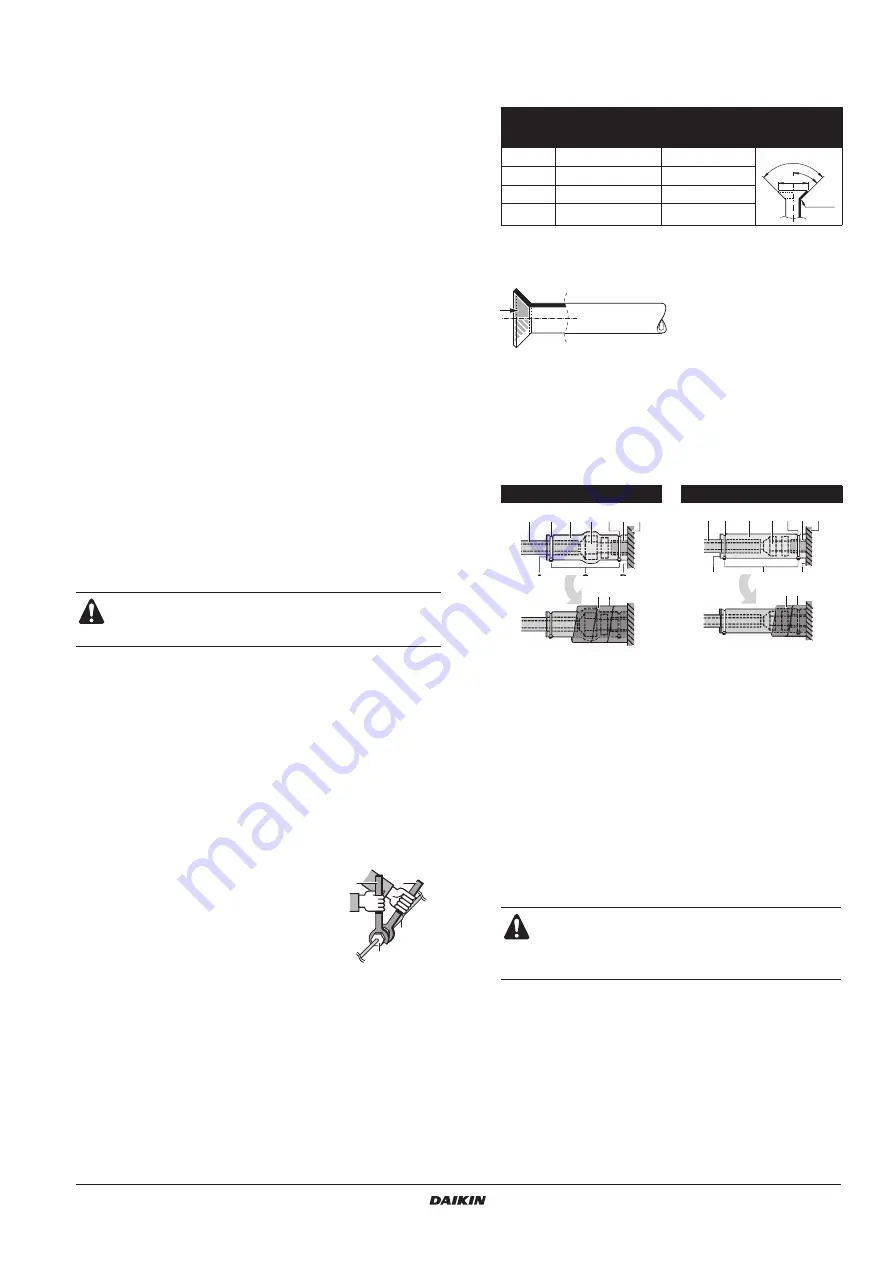
FXMQ50-125P7VEB9
VRV System air conditioners
3P468515-4 – 12.2016
Installation and operation manual
4
I
NDOOR
UNIT
INSTALLATION
When installing optional accessories (except for the air inlet panel),
read also the installation manual of the optional accessories.
Depending on the field conditions, it may be easier to install optional
accessories before the indoor unit is installed.
1
Install the indoor unit temporarily.
-
Attach the hanger bracket to the suspension bolt. Be sure to
fix it securely by using a nut and washer from the upper and
lower sides of the hanger bracket.
2
Check if the unit is horizontally levelled.
-
Do not install the unit tilted. The indoor unit is equipped with a
built-in drain pump and float switch. (If the unit is tilted against
condensate flow, the float switch may malfunction and cause
water to drip.)
-
Check if the unit is levelled at all four corners with a water
level or a water-filled vinyl tube as shown in
3
Tighten the upper nut.
R
EFRIGERANT
PIPING
WORK
For refrigerant piping of outdoor unit, refer to the installation manual
supplied with the outdoor unit.
Before rigging tubes, check which type of refrigerant is used.
■
Use a pipe cutter and flare suitable for the used refrigerant.
■
To prevent dust, moisture or other foreign matter from infiltrating
the tube, either pinch the end, or cover it with tape.
■
Use copper alloy seamless pipes (ISO 1337).
■
The outdoor unit is charged with refrigerant.
■
To prevent water leakage, execute heat insulation work
completely on both sides of the gas and liquid piping. When
using a heat pump, the temperature of the gas piping can reach
up to approximately 120°C, use insulation which is sufficiently
heat resistant.
■
Be sure to use both a spanner and torque wrench together when
connecting or disconnecting pipes to/from the unit.
■
Do not mix anything other than the specified refrigerant, such as
air, etc..., inside the refrigerant circuit.
■
Use annealed material only for flare connections.
■
Refer to
for the dimensions of flare nut spaces and the
appropriate tightening torque. (Overtightening may damage the
flare and cause leaks.)
Table 1
■
When connecting the flare nut, coat the flare inner surface with
ether oil or ester oil and initially tighten 3 or 4 turns by hand
before tightening firmly.
■
If the refrigerant gas leaks during the work, ventilate the area. A
toxic gas is emitted by the refrigerant gas being exposed to a fire.
■
Make sure there is no refrigerant gas leak. A toxic gas may be
released by the refrigerant gas leaking indoor and being
exposed to flames from an area heater, cooking stove, etc.
■
Finally, insulate as shown in the figures below.
Piping insulation procedure
1
Nut (field supply)
2
Washer for hanger bracket (supplied with the unit)
3
Tighten (double nut)
1
Water level
2
Vinyl tube
All field piping must be provided by a licensed refrigeration
technician and must comply with the relevant local and
national codes.
1
Torque wrench
2
Spanner
3
Piping union
4
Flare nut
1
2
4
3
Pipe
gauge
(mm)
Tightening torque
(N•m)
Flare dimension
A (mm)
Flare shape
Ø6.4
15~17
8.7~9.1
Ø9.5
33~39
12.8~13.2
Ø12.7
50~60
16.2~16.6
Ø15.9
63~75
19.3~19.7
Gas piping
Liquid piping
1
Piping insulation material (field supply)
2
Flare nut connection
3
Insulation for fitting (delivered with the unit)
4
Piping insulation material (main unit)
5
Main unit
6
Clamp (field supply)
7
Medium 1 sealing pad for gas piping (delivered with the unit)
Medium 2 sealing pad for liquid piping (delivered with the unit)
A
Turn seams up
B
Attach to base
C
Tighten the part other than the piping insulation material
D
Wrap over from the base of the unit to the top of the flare nut
connection
For local insulation, be sure to insulate local piping all
the way into the pipe connections inside the unit.
Exposed piping may cause condensation or may
cause burns when touched.
R=0.4~0.8
45
° ±
2
90
°±
2
A
A
B
D
C
7
1
2
3
4
5
6
6
A
B
C
1
2
3
4
5
6
6
D
7