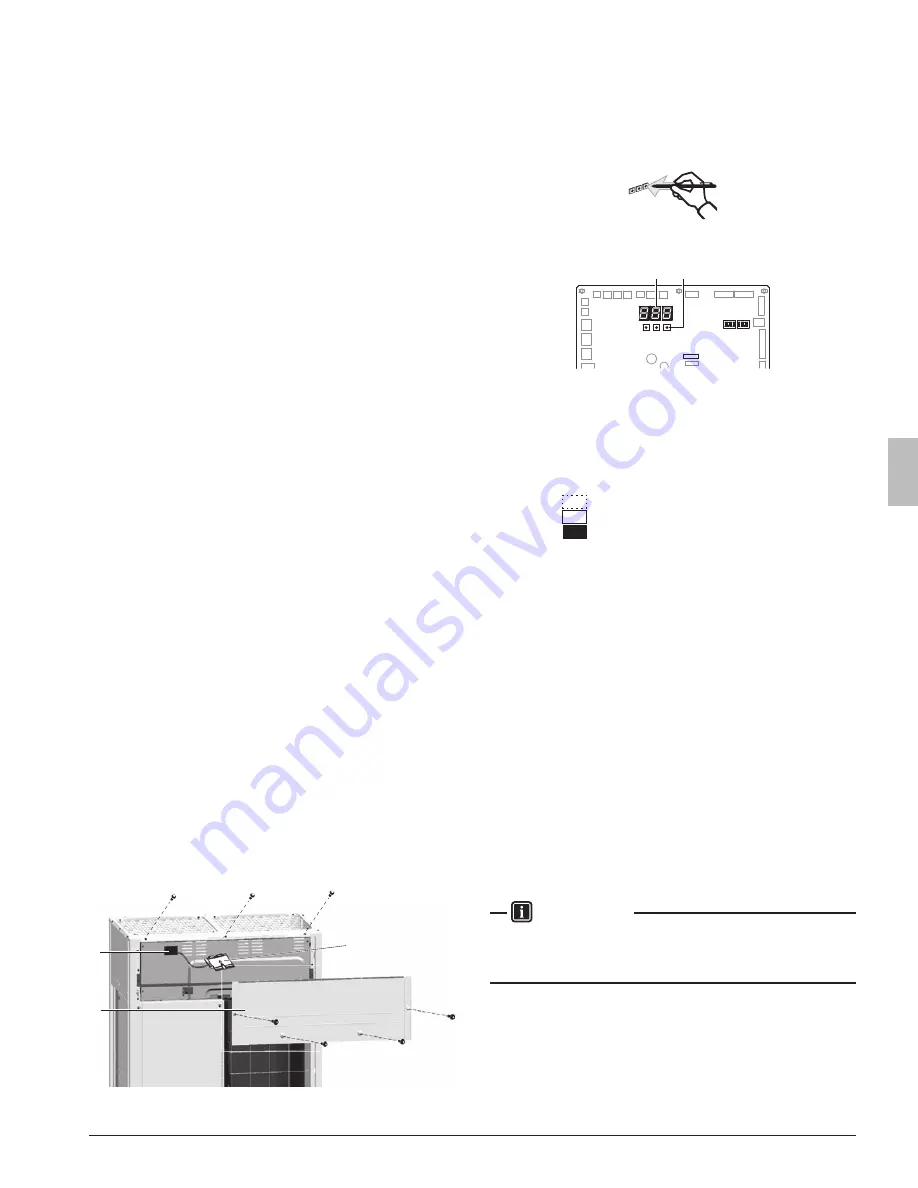
24
English
12 . Checking of device and installation conditions
Be sure to check the followings.
For those doing electrical work
1
Make sure there is no faulty transmission wiring or loosening of a
nut.
See 9.4. Transmission wiring connection procedure on page 20.
2
Make sure there is no faulty power wiring or loosening of a nut.
See 9.5. Power wiring connection procedure on page 21.
3
Has the insulation of the main power circuit deteriorated?
Measure the insulation and check the insulation is above regular
value in accordance with relevant local and national regulations.
For those doing pipe work
1
Make sure piping size is correct.
See 7.2. Selection of piping material on page 9 and 7.4. Selec
-
tion of refrigerant branch kits on page 10.
2
Make sure insulation work is done.
See 11. Pipe insulation.
3
Make sure there is no faulty refrigerant piping.
See 8. Precautions on refrigerant piping on page 14.
13 .
Making field settings
To continue the configuration of the outdoor units, it is required to give
some input to the printed circuit board of the unit. This chapter will
describe how manual input is possible by operating the push buttons/
DIP switches on the printed circuit board and reading the feedback
from the 7 segment displays.
For VRV Aurora series it is alternatively possible to make several
commissioning field settings through a personal computer interface
(for this, option 999482P3 is required). The installer can prepare the
configuration (off-site) on PC and afterwards upload the configuration
to the system. How to connect the cable is described in
13.3. Connecting the PC configurator to the outdoor unit on
page 26.
The contents of the actual settings is discussed and explained in 15.2.
Monitoring function and field settings on page 31.
13 .1 . Accessing the push buttons on the printed circuit
board
It is not required to open the complete control box to access the
push buttons on the printed circuit board and read out the 7 segment
display (s).
To access you can remove the front panel (see figure). Now you can
open the inspection door of the control box cover (see figure). You can
see 3 push buttons and 3 seven-segment displays and DIP switches.
3
1
2
1 Front panel
2 Inspection door
3 Main printed circuit board with 3 seven-segment display
and 3 push buttons
Operate the switches and push buttons with an insulated stick (such
as a closed ballpoint pen) to avoid touching of live parts.
Location of the segment displays, buttons and DIP switches:
BS1 BS2
DS1 DS2
BS3
X27A
1
2
BS1
for changing setting mode
BS2, BS3
for changing field setting
DS1, DS2
DIP switches
1
7 segment displays (3
×
)
2
Push buttons
Segment display indications:
Off
Blinking
On
13 .2 . Operating the push buttons and DIP switches on
the printed circuit board
13 .2 .1 . Operating the push buttons
By operating the push buttons it is possible to:
•
Perform special actions (automatic refrigerant charging, test run, etc).
• Perform field settings (demand operation, low noise, etc).
Below procedure explains how to operate the push buttons to reach
the required mode in the menu, select the correct setting and modify
the value of the setting. This procedure can be used any time special
settings and regular field setting are discussed in this manual (see
15.2. Monitoring function and field settings on page 31).
Setting definition: [A-B]=C; A=mode; B=setting; C=setting value. A, B
and C are numerical values for field settings. Parameter C has to be
defined. It can be a chosen from a set (0, 1, 2, 3, 4, 5, …) or regarded
as an ON/OFF (1 or 0) depending on the contents. This is informed
when the field setting is explained (see 15.2. Monitoring function and
field settings on page 31).
INFORMATION
During special operation (e.g., automatic refrigerant charging, test
run, etc.) or when an malfunction happened, information will contain
letters and numerical values.
Functions of the push button switches which are located on the
main printed circuit board (A1P)
Turn on the power supply of the outdoor unit and all indoor units.
When the communication between indoor units and outdoor unit (s) is
established and normal, the segment indication state will be as follows
(default situation when shipped from factory):
01_EN_3P477778-3C.indb 24
2/8/2018 14:31:37
Summary of Contents for VRV Aurora RXLQ120TATJU
Page 49: ...3P477778 3C EM17A024 1801 HT...