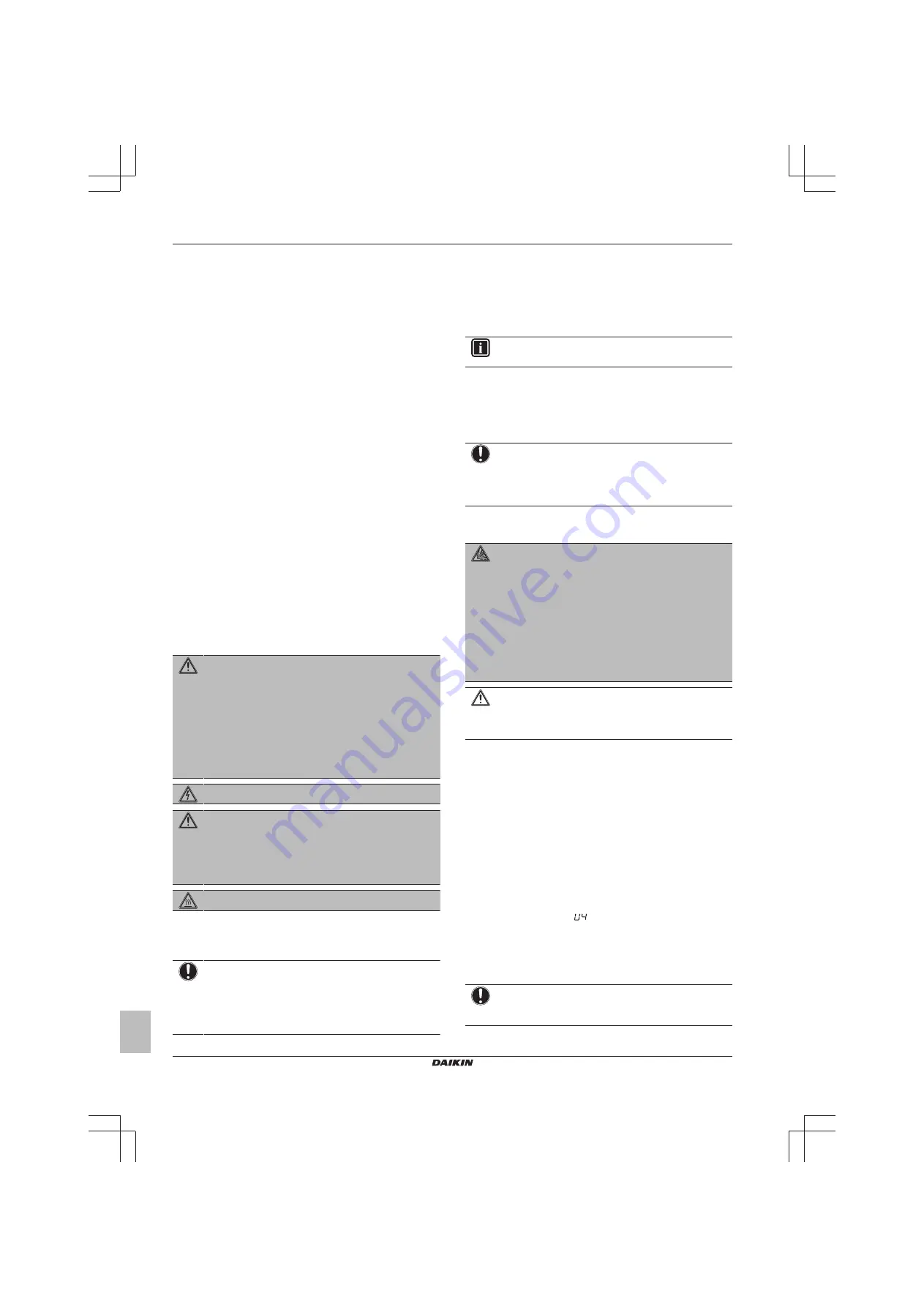
10 Troubleshooting
Installer reference guide
26
RZASG71~Y1
Sky Air Advance-series
4P486047-1 – 2017.04
6
Never directly connect power supply cables to compressors (U,
V, W). This can result in a compressor burnout.
9.3
Checklist for yearly maintenance
of the outdoor unit
Check the following at least once a year:
▪ Outdoor unit heat exchanger.
The heat exchanger of the outdoor unit can get blocked up due to
dust, dirt, leaves, etc. It is recommended to clean the heat
exchanger yearly. A blocked heat exchanger can lead to too low
pressure or too high pressure leading to worse performance.
10
Troubleshooting
10.1
Overview: Troubleshooting
In case of problems:
▪ See
"7.5 Error codes when performing a test run" on page 24
.
▪ See the service manual.
This section provides useful information for diagnosing and
correcting certain problems which may occur with the unit. This
troubleshooting and related corrective actions may only be carried
out by the installer or service agent.
Before troubleshooting
Carry out a thorough visual inspection of the unit and look for
obvious defects such as loose connections or defective wiring.
10.2
Precautions when troubleshooting
WARNING
▪ When carrying out an inspection on the switch box of
the unit, always make sure that the unit is disconnected
from the mains. Turn off the respective circuit breaker.
▪ When a safety device was activated, stop the unit and
find out why the safety device was activated before
resetting it. NEVER bridge safety devices or change
their values to a value other than the factory default
setting. If you are unable to find the cause of the
problem, call your dealer.
DANGER: RISK OF ELECTROCUTION
WARNING
Prevent hazard due to the inadvertent resetting of the
thermal cut-out: this appliance must NOT be supplied
through an external switching device, such as a timer, or
connected to a circuit that is regularly turned ON and OFF
by the utility.
DANGER: RISK OF BURNING
11
Disposal
NOTICE
Do not try to dismantle the system yourself: the dismantling
of the system, treatment of the refrigerant, oil and other
parts must comply with applicable legislation. Units must
be treated at a specialised treatment facility for reuse,
recycling and recovery.
11.1
Overview: Disposal
Typical workflow
Disposing of the system typically consists of the following stages:
1
Pumping down the system.
2
Bringing the system to a specialized treatment facility.
INFORMATION
For more details, see the service manual.
11.2
About pump down
The unit is equipped with an automatic pump down function, with
which you can collect all refrigerant from the system into the outdoor
unit.
NOTICE
The outdoor unit is equipped with a low pressure switch or
a low pressure sensor to protect the compressor by turning
it OFF. NEVER short-circuit the low pressure switch during
pump down operation.
11.3
To pump down
DANGER: RISK OF EXPLOSION
Pump down – Refrigerant leakage.
If you want to pump
down the system, and there is a leakage in the refrigerant
circuit:
▪ Do NOT use the unit's automatic pump down function,
with which you can collect all refrigerant from the
system into the outdoor unit.
Possible consequence:
Self-combustion and explosion of the compressor
because of air going into the operating compressor.
▪ Use a separate recovery system so that the unit's
compressor does NOT have to operate.
CAUTION
Do not use the unit's automatic pump down function if the
total piping length exceeds the chargeless length. A
fraction of the refrigerant could be left in the circuit.
1
Turn ON the main power supply switch.
2
Make sure the liquid stop valve and the gas stop valve are
open.
3
Press the pump down button (BS2) for at least 8 seconds. BS2
is located on the PCB in the outdoor unit (see wiring diagram).
Result:
The compressor and outdoor unit fan start
automatically, and the indoor unit fan might start automatically.
4
±2 minutes after the compressor started, close the
liquid stop
valve
. If it is not closed properly during compressor operation,
the system cannot be pumped down.
5
Once the compressor stops (after 2~5 minutes), close the
gas
stop valve
within 3 minutes after the compressor has stopped.
Result:
The pump down operation is finished. The user
interface may display "
" and the indoor pump may continue
operating. This is NOT a malfunction. Even if you press the ON
button on the user interface, the unit will NOT start. To restart
the unit, turn OFF the main power supply switch and turn it ON
again.
6
Turn OFF the main power supply switch.
NOTICE
Make sure to reopen both stop valves before restarting the
unit.
Summary of Contents for Sky Air Advance Series
Page 31: ......