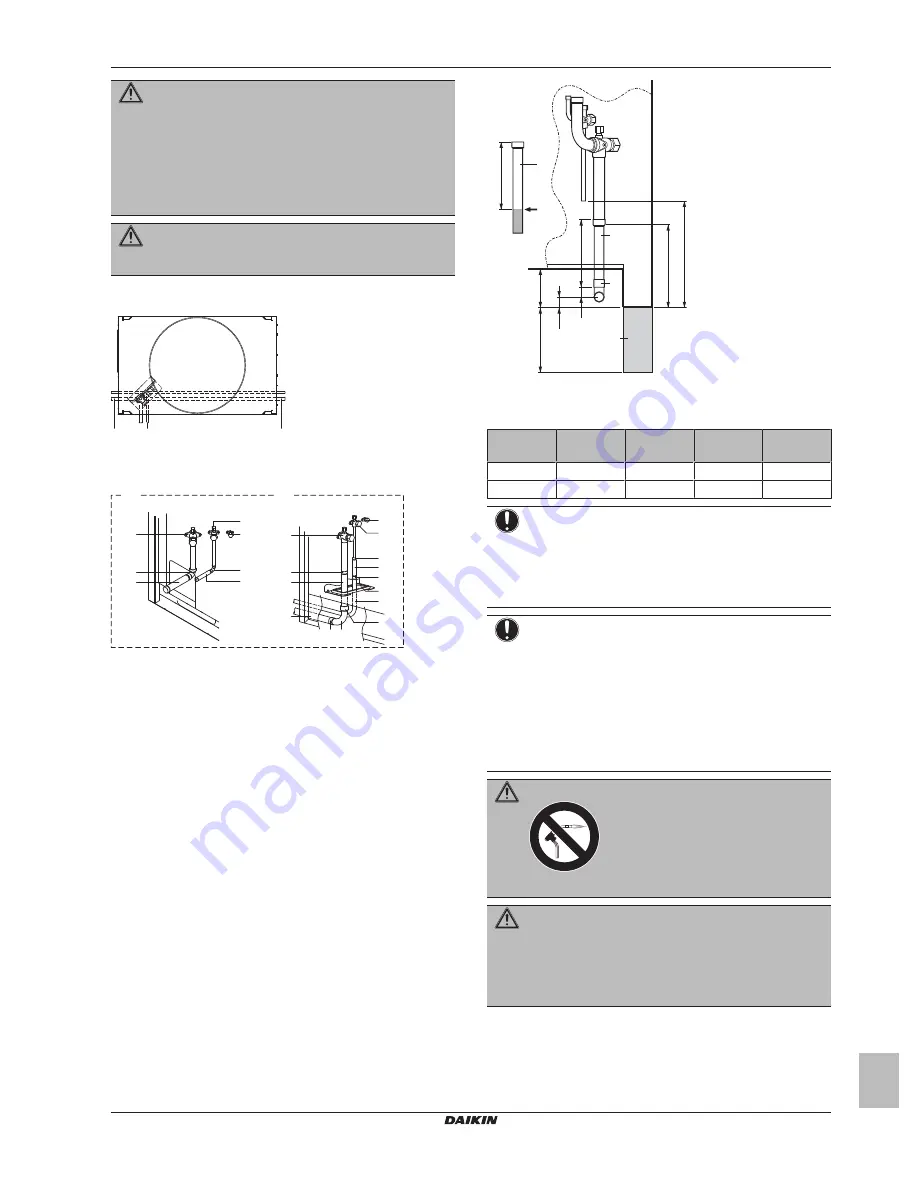
5 Installation
Installation and operation manual
15
SERHQ020~0 SEHVX20~64BAW
Split packaged air-cooled water chiller
4P508019-2B – 2018.01
WARNING
Take sufficient precautions in case of refrigerant leakage. If
refrigerant gas leaks, ventilate the area immediately.
Possible risks:
▪ Excessive refrigerant concentrations in a closed room
can lead to oxygen deficiency.
▪ Toxic gas may be produced if refrigerant gas comes
into contact with fire.
WARNING
NEVER directly touch any accidental leaking refrigerant.
This could result in severe wounds caused by frostbite.
The refrigerant piping can be installed from the front or from the side
of the unit (when taken out from the bottom) as shown in the figure.
a
b
c
a
Left-side connection
b
Front connection
c
Right-side connection
c
b
h
f
d
h
a
c
b
g
h
i
h
j
k
h
h
h
e
i
a
A
B
A
For front connection, remove the stop valve cover to
connect the refrigerant piping.
B
For side connection, remove the knockouts in the bottom
frame and route the piping under the bottom frame.
a
Gas pipe stop valve
b
Liquid pipe stop valve
c
Service port for adding refrigerant
d
Gas side accessory pipe (1)
e
Gas side accessory pipe (2)
f
Liquid side accessory pipe (1)
g
Liquid side accessory pipe (2)
h
Brazing
i
Gas side piping (field supply)
j
Liquid side piping (field supply)
k
Open the knockout holes with a hammer
Cutting the gas side accessory pipe
When connecting the refrigerant piping from the side, cut the gas
side accessory pipe as shown in the figure.
A
A
B
C
D
a
b
a
c
d
25
150
90
a
Gas side accessory pipe
b
Cut here
c
Gas side piping (field supply)
d
Unit base
Outdoor
unit
A
B
C
D
SERHQ020
156
23
192
247
SERHQ032
150
29
192
251
NOTICE
▪ When connecting the piping on site, be sure to use the
accessory piping.
▪ Make sure the onsite piping does not come into contact
with other piping, the bottom frame or side panels of
the unit.
NOTICE
Precautions when making knockout holes:
▪ Avoid damaging the casing.
▪ After making the knockout holes, we recommend you
remove the burrs and paint the edges and areas
around the edges using repair paint to prevent rusting.
▪ When passing electrical wiring through the knockout
holes, wrap the wiring with protective tape to prevent
damage.
WARNING
Never remove the pinched piping by brazing.
WARNING
Any gas or oil remaining inside the stop valve may blow off
the pinched piping.
Failure to observe the instructions in procedure below
properly may result in property damage or personal injury,
which may be serious depending on the circumstances.
Use the following procedure to remove the pinched piping:
1
Remove the valve lid and make sure that the stop valves are
fully closed.
Summary of Contents for SERHQ020BAW1
Page 56: ......
Page 57: ......
Page 58: ......
Page 59: ......
Page 60: ...4P508019 2B 2018 01 Copyright 2018 Daikin 4P508019 2 B 0000000...