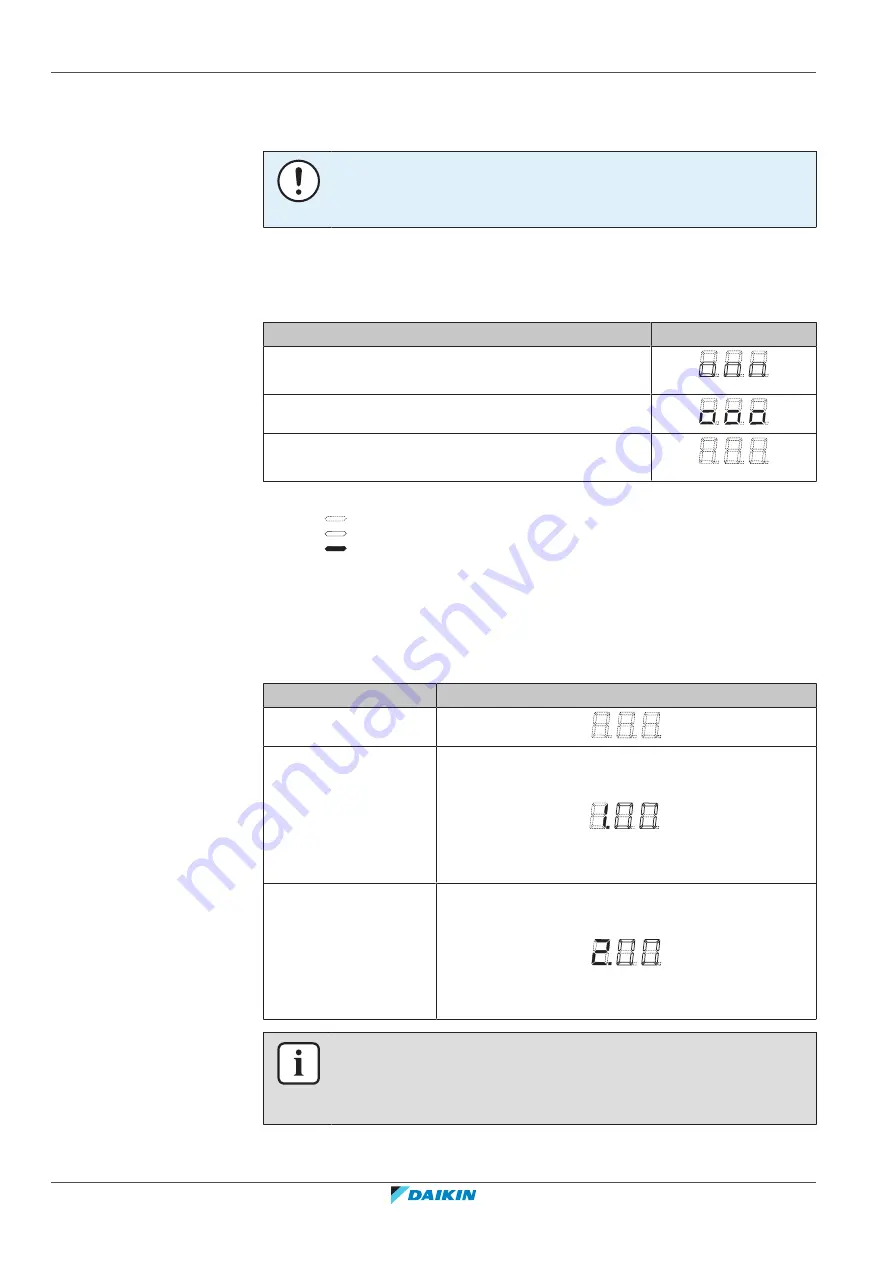
19
|
Configuration
Installer and user reference guide
124
RYYQ+RYMQ+RXYQ
VRV IV+ heat pump
4P546228-1C – 2021.11
19.2.4 To access mode 1 or 2
Initialisation: default situation
NOTICE
Be sure to turn ON the power 6 hours before operation in order to have power
running to the crankcase heater and to protect the compressor.
Turn on the power supply of the outdoor unit and all indoor units. When the
communication between indoor units and outdoor unit(s) is established and
normal, the 7‑segment display indication state will be as below (default situation
when shipped from factory).
Stage
Display
When turning on the power supply: flashing as indicated.
First checks on power supply are executed (1~2 min).
When no trouble occurs: lighted as indicated (8~10 min).
Ready for operation: blank display indication as
indicated.
7‑segment display indications:
Off
Blinking
On
In case of malfunction, the malfunction code is displayed on the indoor unit user
interface and the outdoor unit 7‑segment display. Solve the malfunction code
accordingly. The communication wiring should be checked at first.
Access
BS1 is used to switch between the default situation, mode 1 and mode 2.
Access
Action
Default situation
Mode 1
Push BS1 one time.
7‑segment display indication changes to:
.
Push BS1 one more time to return to the default
situation.
Mode 2
Push BS1 for at least 5 seconds.
7‑segment display indication changes to:
Push BS1 one more time (shortly) to return to the
default situation.
INFORMATION
If you get confused in the middle of the process, push BS1 to return to the default
situation (no indication on 7‑segment displays: blank, refer to
124].
Summary of Contents for RYYQ8U7Y1B
Page 174: ......
Page 175: ......
Page 176: ...4P546228 1C 2021 11 Copyright 2018 Daikin Verantwortung f r Energie und Umwelt...