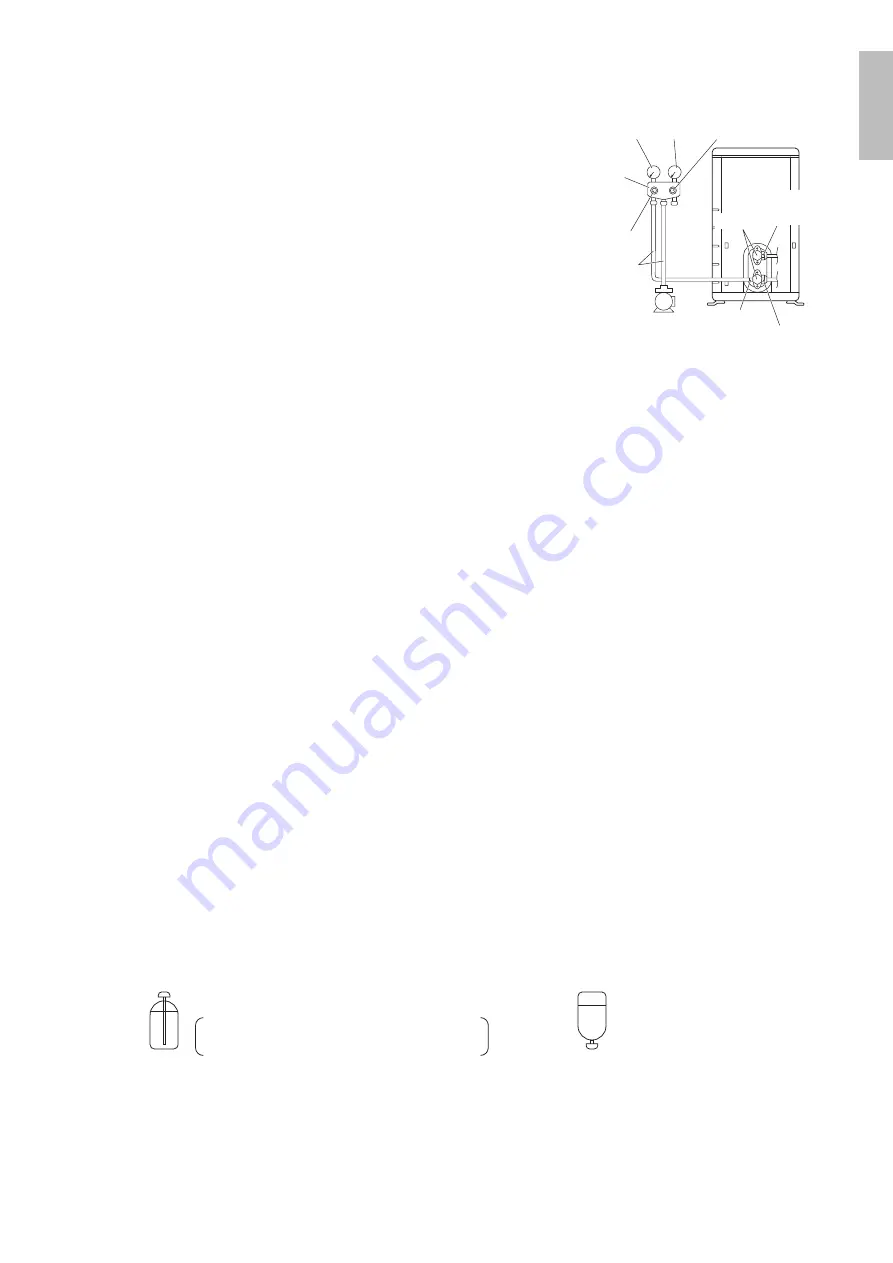
8
■
English
• When piping work is complete, it is necessary to perform a pressure test
and evacuate system with a vacuum pump.
• If using additional refrigerant, purge the air from the refrigerant pipes and
indoor unit using a vacuum pump, then charge additional refrigerant.
•
Use a hexagonal wrench (3/16 inch (4mm)) to operate the stop valve rod.
• All refrigerant pipe joints should be tightened with a torque wrench to the
specified tightening torque.
Compound
pressure gauge
Pressure
meter
High-pressure
valve
Low-pressure
valve
Vacuum pump
Service port
Liquid
stop
valve
Valve caps
Gas stop valve
Charging
hoses
Gauge
manifold
1) Pressurize the liquid pipe and gas pipe from the service ports of each stop valve to 550psi (3.8MPa) (do not pressurize
more than 550psi (3.8MPa)) for 1 hour minimum, 24 hours recommended. If there is a pressure drop, check for leaks,
make repairs and perform the pressure test again.
2) Connect the gauge manifold’s charging hose to the gas stop valve’s service port.
3) Fully open the low-pressure valve (Lo) on the gauge manifold and fully close the high-pressure valve (Hi).
(High-pressure valve will require no further operation.)
4)
Evacuate system using vacuum pump to below 500 microns for 1 hour minimum.
5) Close the low-pressure valve (Lo) on the gauge manifold and stop vacuum pumping.
(Maintain this condition for a few minutes to make sure that the compound pressure gauge pointer does not swing
back.)*
1
6) Remove the valve caps from the liquid stop valve and gas stop valve.
7)
To open the liquid stop valve, turn the rod of the valve 90° counter-clockwise using a hexagonal wrench.
Close it after 5 seconds, and check for gas leakage.
Using soapy water, check for gas leakage from the indoor unit’s flare and outdoor unit’s flare and valve rods.
After the check is complete, wipe all soapy water off.
8) Disconnect the charging hoses from the service port for the gas stop valve, then fully open the liquid and gas stop valves.
(Do not attempt to turn the valve rods further than they can go.)
9)
Tighten the valve caps and service port caps for the liquid and gas stop valves with a torque wrench to the specified
torques.
Refer to
“4. Refrigerant piping”
on page 6 for details.
*
1
If the compound pressure gauge pointer swings back, the refrigerant may have water content or there may be a loose
pipe joint.
Check all pipe joints and retighten nuts as needed, then repeat steps 3) through 5).
6.
Refilling refrigerant
Check the type of refrigerant to be used on the machine nameplate.
Precautions when adding R410A
Fill from the liquid pipe in liquid form.
R410A is a mixed refrigerant, so adding it in gas form may cause the refrigerant composition to change, preventing normal
operation.
•
Before filling, check whether the cylinder has a siphon attached or not. (It should have something like “liquid filling siphon
attached” displayed on it.)
Filling a cylinder with an attached siphon
Stand the cylinder upright when filling.
There is a siphon pipe inside, so the cylinder
need not be upside-down to fill with liquid.
Filling other cylinders
Turn the cylinder
upside-down when filling.
• Be sure to use the R410A tools to ensure pressure and to prevent foreign objects entering.
English
01_EN_3P572321-2.indd 8
2019/07/02 16:31:45