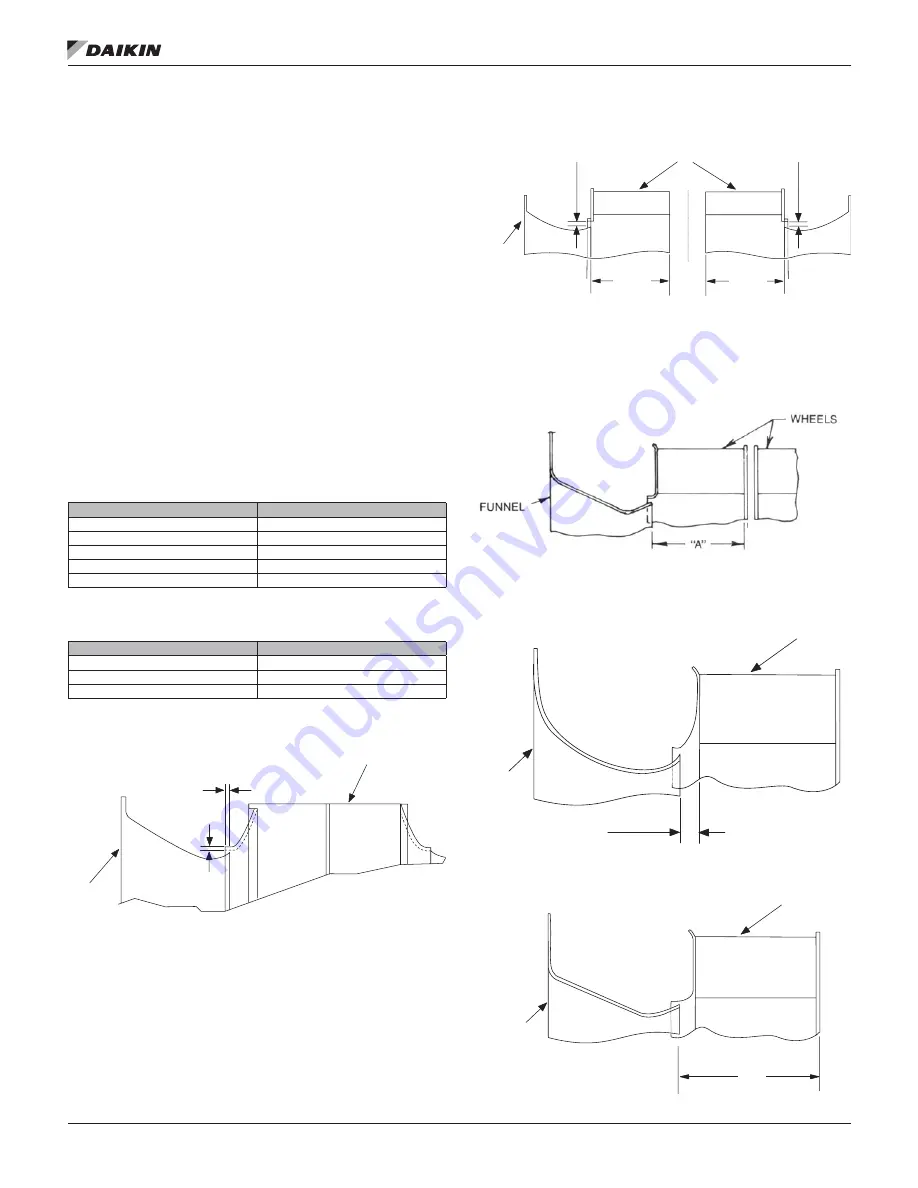
IM 926-3 • ROOFPAK APPLIED SYSTEMS 112 www.DaikinApplied.com
Maintenance and Service
Supply Fan Wheel-to-Funnel Alignment
If the unit is equipped with an airfoil or backward curved supply
fan, the fan wheel-to-funnel alignment must be as shown in
,
,
,
, and
to obtain proper air delivery and operating clearance. If
necessary, adjustments are made as follows:
1.
Verify that the fan shaft has not moved in its bearings.
2.
Loosen the fan hub setscrews and move the wheel(s)
along the shaft as necessary to obtain the correct
dimension shown in
.
3.
Retighten the setscrews to the torque specification given
in Table 30 on page 113. Tighten the setscrews over the
keyway first; tighten those at 90 degrees to the keyway
last.
4.
Verify that the radial clearance around the fan is uniform.
Radial clearance can be adjusted by slightly loosening
the funnel hold-down fasteners, shifting the funnel as
required, and retightening the fasteners.
Table 31: 27" to 40" DWDI Airfoil Wheel-to-Funnel
Relationship
Wheel diameter (inches)
“A” [+0 .3/ – 0 .0] inches (mm)
27
9.9 (246)
30
10.6 (269)
33
11.7 (297)
36
13.1 (333)
40
14.5 (368)
Table 32: 40", 44” and 49” SWSI Airfoil Wheel-to-Funnel
Relationship
Wheel diameter (inches)
“A” inches (mm)
40
0.62 (15.75)
44
16.21 (411.7)
49
17.81 (452.4)
Figure 122: 20" DWDI Airfoil Wheel-to-Funnel (015C to
030C)
Figure 123: 24" DWDI Backward Curved Wheel-to-Funnel
(036C, 040C)
Figure 124: 27" to 40" DWDI Airfoil Wheel-to-Funnel
Alignment
Figure 125: 40" SWSI Airfoil Wheel-to-Funnel Alignment
(RDT 045 to 075)
Figure 126: 44" and 49" SWSI airfoil Wheel-to-Funnel
Alignment
Summary of Contents for RoofPak RCS Series
Page 129: ......