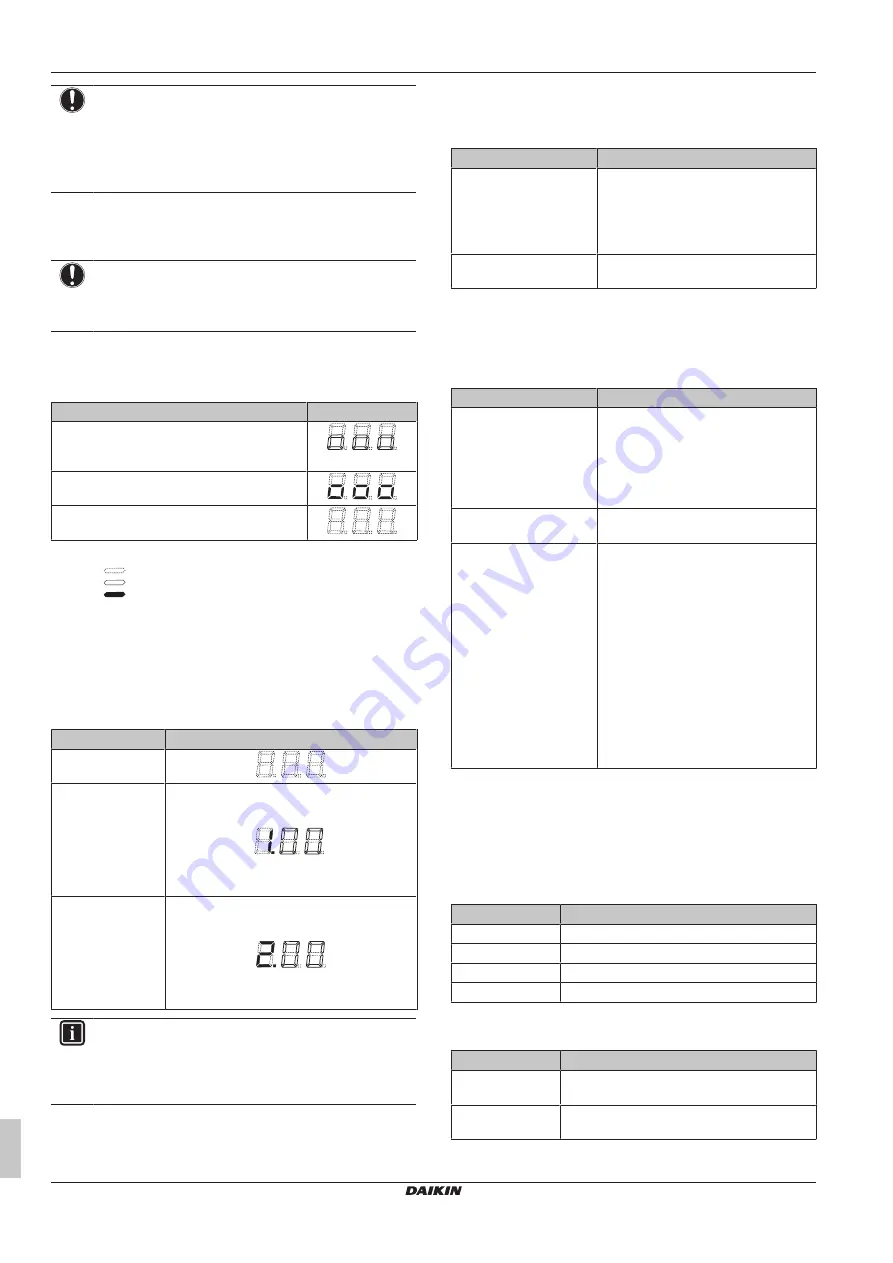
16 Configuration
Installation and operation manual
36
REYQ8~20+REMQ5U7Y1B
VRV IV+ heat recovery
4P546222-1B – 2020.10
NOTICE
Make sure that all outside panels, except for the service
cover on the electrical component box, are closed while
working.
Close the lid of the electrical component box firmly before
turning on the power.
16.1.4
To access mode 1 or 2
Initialisation: default situation
NOTICE
Be sure to turn ON the power 6 hours before operation in
order to have power running to the crankcase heater and
to protect the compressor.
Turn on the power supply of the outdoor unit and all indoor units.
When the communication between indoor units and outdoor unit(s) is
established and normal, the 7‑segment display indication state will
be as below (default situation when shipped from factory).
Stage
Display
When turning on the power supply: flashing as
indicated. First checks on power supply are
executed (1~2 min).
When no trouble occurs: lighted as indicated
(8~10 min).
Ready for operation: blank display indication as
indicated.
7‑segment display indications:
Off
Blinking
On
In case of malfunction, the malfunction code is displayed on the
indoor unit user interface and the outdoor unit 7‑segment display.
Solve the malfunction code accordingly. The communication wiring
should be checked at first.
Access
BS1 is used to switch between the default situation, mode 1 and
mode 2.
Access
Action
Default situation
Mode 1
Push BS1 one time.
7‑segment display indication changes to:
.
Push BS1 one more time to return to the
default situation.
Mode 2
Push BS1 for at least 5 seconds.
7‑segment display indication changes to:
Push BS1 one more time (shortly) to return to
the default situation.
INFORMATION
If you get confused in the middle of the process, push BS1
to return to the default situation (no indication on
7‑segment displays: blank, refer to
16.1.5
To use mode 1
Mode 1 is used to set basic settings and to monitor the status of the
unit.
What
How
Changing and accessing
the setting in mode 1
Once mode 1 is selected (push BS1
one time), you can select the wanted
setting. It is done by pushing BS2.
Accessing the selected setting's value is
done by pushing BS3 one time.
To quit and return to the
initial status
Press BS1.
16.1.6
To use mode 2
The master unit should be used to input field settings in
mode 2.
Mode 2 is used to set field settings of the outdoor unit and system.
What
How
Changing and accessing
the setting in mode 2
Once mode 2 is selected (push BS1 for
more than 5 seconds), you can select
the wanted setting. It is done by pushing
BS2.
Accessing the selected setting's value is
done by pushing BS3 1 time.
To quit and return to the
initial status
Press BS1.
Changing the value of the
selected setting in mode 2
▪ Once mode 2 is selected (push BS1
for more than 5 seconds) you can
select the wanted setting. It is done
by pushing BS2.
▪ Accessing the selected setting's value
is done by pushing BS3 1 time.
▪ Now BS2 is used to select the
required value of the selected setting.
▪ When the required value is selected,
you can define the change of value
by pushing BS3 1 time.
▪ Press BS3 again to start operation
according to the chosen value.
16.1.7
Mode 1: Monitoring settings
[1‑0]
Shows whether the unit you check is a master, slave 1 or slave 2
unit.
The master unit should be used to input field settings in
mode 2.
[1‑0]
Description
No indication
Undefined situation.
0
Outdoor unit is master unit.
1
Outdoor unit is slave 1 unit.
2
Outdoor unit is slave 2 unit.
[1‑1]
Shows the status of low noise operation.
[1‑1]
Description
0
Unit is currently not operating under low noise
restrictions.
1
Unit is currently operating under low noise
restrictions.
Summary of Contents for REYQ8U7Y1B
Page 51: ......