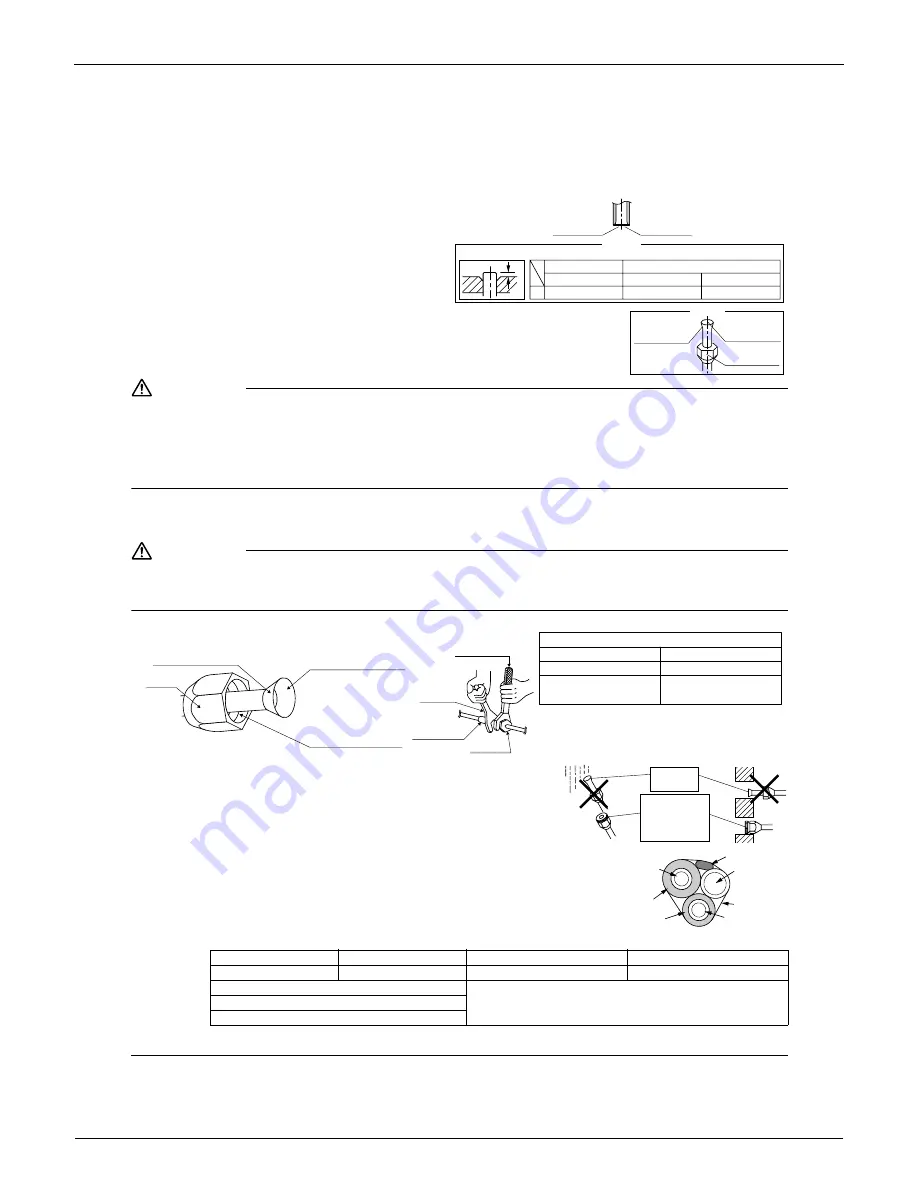
Installation Manual
EDUS04-906
30
Room Air Conditioners H-Series
11
Refri
g
erant Pipin
g
Work
1.
Flarin
g
the pipe end.
1) C
u
t the pipe end
w
ith a pipe c
u
tter.
2) Remo
v
e
bu
rrs
w
ith the c
u
t s
u
rface facing do
w
n
w
ard
so that the chips do not enter the pipe.
3) P
u
t the flare n
u
t on the pipe.
4) Flare the pipe.
5) Check that the flaring is properly made.
WARNING
1) Do not
u
se mineral oil on flared part.
2) Pre
v
ent mineral oil from getting into the system as this
w
o
u
ld red
u
ce the lifetime of the
u
nits.
3)
N
e
v
er
u
se piping
w
hich has
b
een
u
sed for pre
v
io
u
s installations. Only
u
se par ts
w
hich are deli
v
ered
w
ith the
u
nit.
4) Do ne
v
er install a drier to this R410A
u
nit in order to g
u
arantee its lifetime.
5) The drying material may dissol
v
e and damage the system.
6) Incomplete flaring may ca
u
se refrigerant gas leakage.
2.
Refri
g
erant pipin
g
.
CAUTION
1) Use the flare n
u
t fixed to the main
u
nit t o pre
v
ent aging and deterioration.
2) To pre
v
ent gas leakage, apply refrigeration oil only to the inner s
u
rface of the flare. (Use refrigeration oil for R410A.)
3) Use tor
qu
e
w
renches
w
hen tightening the flare n
u
ts to pre
v
ent damage to the flare n
u
ts and gas leakage.
Align the centers of
b
oth flares and tighten the flare n
u
ts 3 or 4 t
u
rns
b
y hand. Then tighten them f
u
lly
w
ith the tor
qu
e
w
renches.
2-1. Caution on pipin
g
handlin
g
.
1) Protect the open end of the pipe against d
u
st and moist
u
re.
2) All pipe
b
ends sho
u
ld
b
e as gentle as possi
b
le. Use a pipe
b
ender for
b
ending.
2-2. Selection of copper and heat insulation materials.
•
W
hen
u
sing commercial copper pipes and fittings, o
b
ser
v
e the follo
w
ing:
1) Ins
u
lation material: Polyethylene foam
Heat transfer rate: 0.041 to 0.052
W
/mK (0.024 to 0.030 Bt
u
/fth°F (0.035 to 0.045 kcal/mh°C))
Choose heat ins
u
lation materials that are designed for H
V
AC
u
se.
2) Be s
u
re to ins
u
late
b
oth the gas and li
qu
id piping and to pro
v
ide ins
u
lation dimensions as
b
elo
w
.
3) Use separate thermal ins
u
lation pipes for gas and li
qu
id refrigerant pipes.
Gas side
Li
qu
id side
Gas pipe thermal ins
u
lation
Li
qu
id pipe thermal ins
u
lation
O.D. 3/
8
inch (9.5mm)
O.D. 1/4 inch (6.4mm)
I.D. 0.472-0.590 inch (12-15mm)
I.D. 0.315-0.393 inch (
8
-10mm)
Minim
u
m
b
end radi
u
s
Thickness 0.393 inch (10mm) Min.
1-3/16 inch (30mm) or more
Thickness 0.031 inch (0.
8
mm) (C1220T-O)
Set exactly at the position sho
w
n
b
elo
w
.
A
Flaring
Die
A
0-0.020 inch (0-0.5mm)
Cl
u
tch-type
Flare tool for R410A
0.039-0.059 inch (1.0-1.5mm)
Cl
u
tch-type (Rigid-type)
0.059-0.079 inch (1.5-2.0mm)
W
ing-n
u
t type (Imperial-type)
Con
v
entional flare tool
(C
u
t exactly at
right angles.)
Remo
v
e
bu
rrs
Check
Flare’s inner
s
u
rface m
u
st
b
e fla
w
-free.
The pipe end m
u
st
b
e e
v
enly flared in
a perfect circle.
Make s
u
re that the
flare n
u
t is fitted.
24.1-29.4 ft·l
b
f
(32.7-39.9
N
·m)
10.4-12.7 ft·l
b
f
(14.2-17.2
N
·m)
Flare n
u
t tightening tor
qu
e
Gas side
Li
qu
id side
3/
8
inch (9.5mm)
1/4 inch (6.4mm)
Do not apply refrigeration
oil to the o
u
ter s
u
rface.
Flare n
u
t
Apply refrigeration oil to the
inner s
u
rface of the flare.
Do not apply refrigeration
oil to the flare n
u
t a
v
oid
tightening
w
ith o
v
er tor
qu
e.
[Apply oil]
Tor
qu
e
w
rench
Piping
u
nion
Flare n
u
t
Spanner
[Tighten]
W
all
If no flare cap is
a
v
aila
b
le, co
v
er
the flare mo
u
th
w
ith tape to keep
dirt or
w
ater o
u
t.
Be s
u
re to
place a cap.
Rain
Ins
u
lation tape
Li
qu
id pipe ins
u
lation
Inter-
u
nit
w
iring
Gas pipe ins
u
lation
Gas pipe
Drain hose
Li
qu
id pipe
Summary of Contents for Quaternity FTXG09HVJU
Page 1: ...EDUS04 906_a H Series Heat Pump...
Page 44: ...EDUS04 906 Operation Manual Room Air Conditioners H Series 43 Ground terminal...
Page 45: ...Operation Manual EDUS04 906 44 Room Air Conditioners H Series DRY button...
Page 46: ...EDUS04 906 Operation Manual Room Air Conditioners H Series 45...
Page 47: ...Operation Manual EDUS04 906 46 Room Air Conditioners H Series...
Page 48: ...EDUS04 906 Operation Manual Room Air Conditioners H Series 47...
Page 50: ...EDUS04 906 Operation Manual Room Air Conditioners H Series 49...
Page 51: ...Operation Manual EDUS04 906 50 Room Air Conditioners H Series...
Page 52: ...EDUS04 906 Operation Manual Room Air Conditioners H Series 51...
Page 55: ...Operation Manual EDUS04 906 54 Room Air Conditioners H Series...
Page 56: ...EDUS04 906 Operation Manual Room Air Conditioners H Series 55 1 8 F 1 C 3 6 F 2 C...
Page 57: ...Operation Manual EDUS04 906 56 Room Air Conditioners H Series...
Page 58: ...EDUS04 906 Operation Manual Room Air Conditioners H Series 57 COOLING or DRY COOLING mode or...
Page 59: ...Operation Manual EDUS04 906 58 Room Air Conditioners H Series...
Page 60: ...EDUS04 906 Operation Manual Room Air Conditioners H Series 59...
Page 61: ...Operation Manual EDUS04 906 60 Room Air Conditioners H Series...
Page 62: ...EDUS04 906 Operation Manual Room Air Conditioners H Series 61...
Page 63: ...Operation Manual EDUS04 906 62 Room Air Conditioners H Series...
Page 64: ...EDUS04 906 Operation Manual Room Air Conditioners H Series 63...
Page 65: ...Operation Manual EDUS04 906 64 Room Air Conditioners H Series...
Page 66: ...EDUS04 906 Operation Manual Room Air Conditioners H Series 65...
Page 67: ...Operation Manual EDUS04 906 66 Room Air Conditioners H Series...
Page 68: ...EDUS04 906 Operation Manual Room Air Conditioners H Series 67...
Page 69: ...Operation Manual EDUS04 906 68 Room Air Conditioners H Series...
Page 70: ...EDUS04 906 Operation Manual Room Air Conditioners H Series 69 3P226009 1...
Page 79: ...Optional Accessories EDUS04 906 78 Room Air Conditioners H Series...