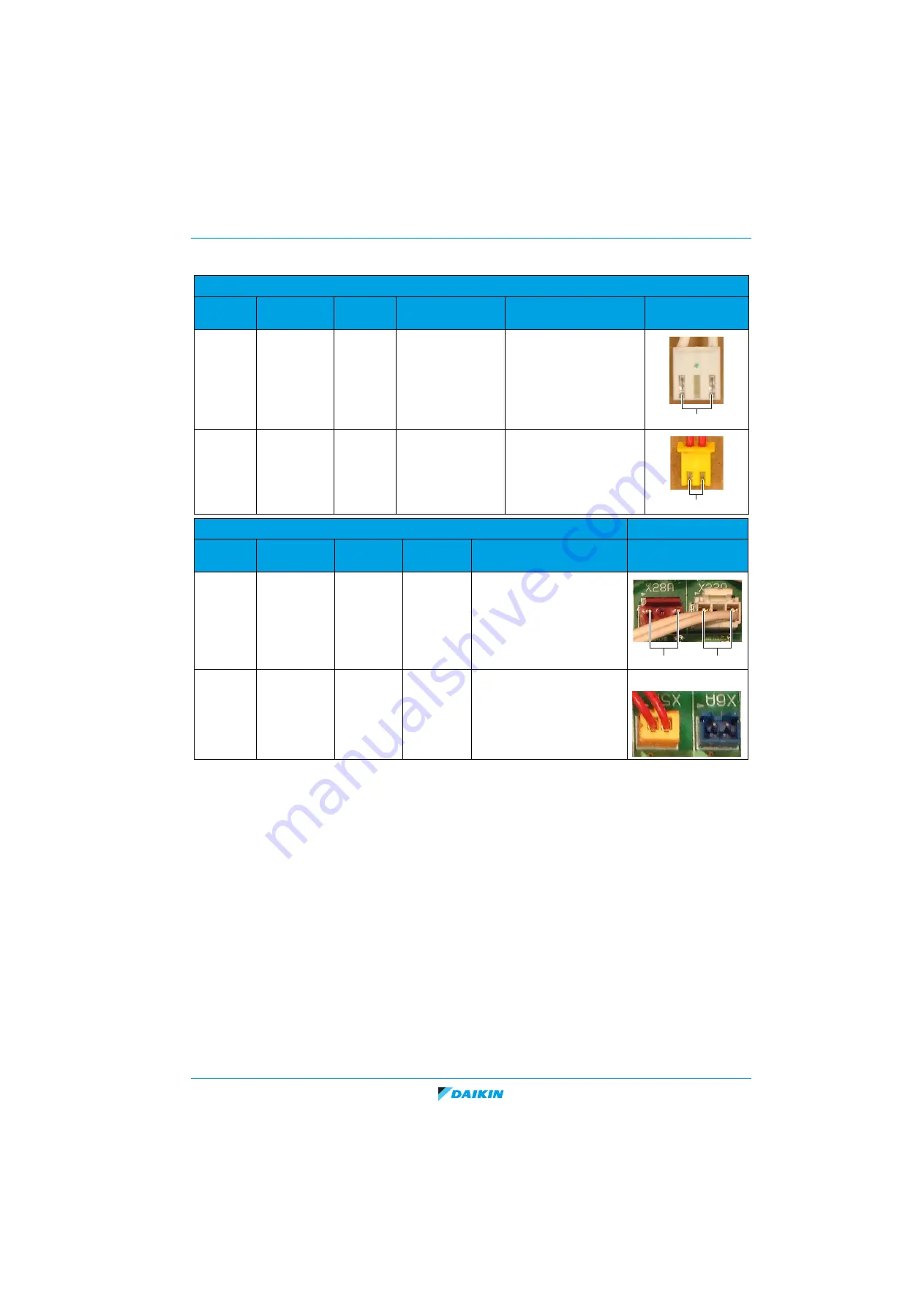
ESIE19-06
|
Part 2. Troubleshooting
2.4. Component checklist
21/01/20
|
Version 1.1
Page 35
Modular L Smart
2.4.1.2. Damper motor + limit switch
Disconnected from main PCB
Part
Connector
Check
method
Reference (kΩ)
Remark
Measure point
motor
X22A, X28A
resistance
12,3
white wires
limit switch
X15A, X6A
resistance
∞
:
damper position
Hex. & Byp.
while damper moving contact
closed 0 Ω
Connected - main PCB power on
Part
Connector
Check
method
Reference
(Volt)
Remark
Measure point
motor
X22A, X28A
ACV
230
permanent when energized
limit switch
X15A, X6A
DCV
16
depends on position damper:
• at HEX & Bypass: 16 VDC
• during change: 0 VDC
Nȍ
0Ω
230V
230V
+ -
+ -
Summary of Contents for Modular L Smart
Page 1: ...Service Manual Modular L Smart ESIE19 06 ...
Page 6: ...ESIE19 06 Page 6 21 01 20 Version 1 1 Modular L Smart ...
Page 16: ...ESIE19 06 Part 1 Introduction 1 4 How to use Page 16 21 01 20 Version 1 1 Modular L Smart ...
Page 59: ...ESIE19 06 Part 4 Maintenance 4 1 HRV unit 21 01 20 Version 1 1 Page 59 Modular L Smart ...
Page 60: ...ESIE19 06 Part 4 Maintenance 4 1 HRV unit Page 60 21 01 20 Version 1 1 Modular L Smart ...