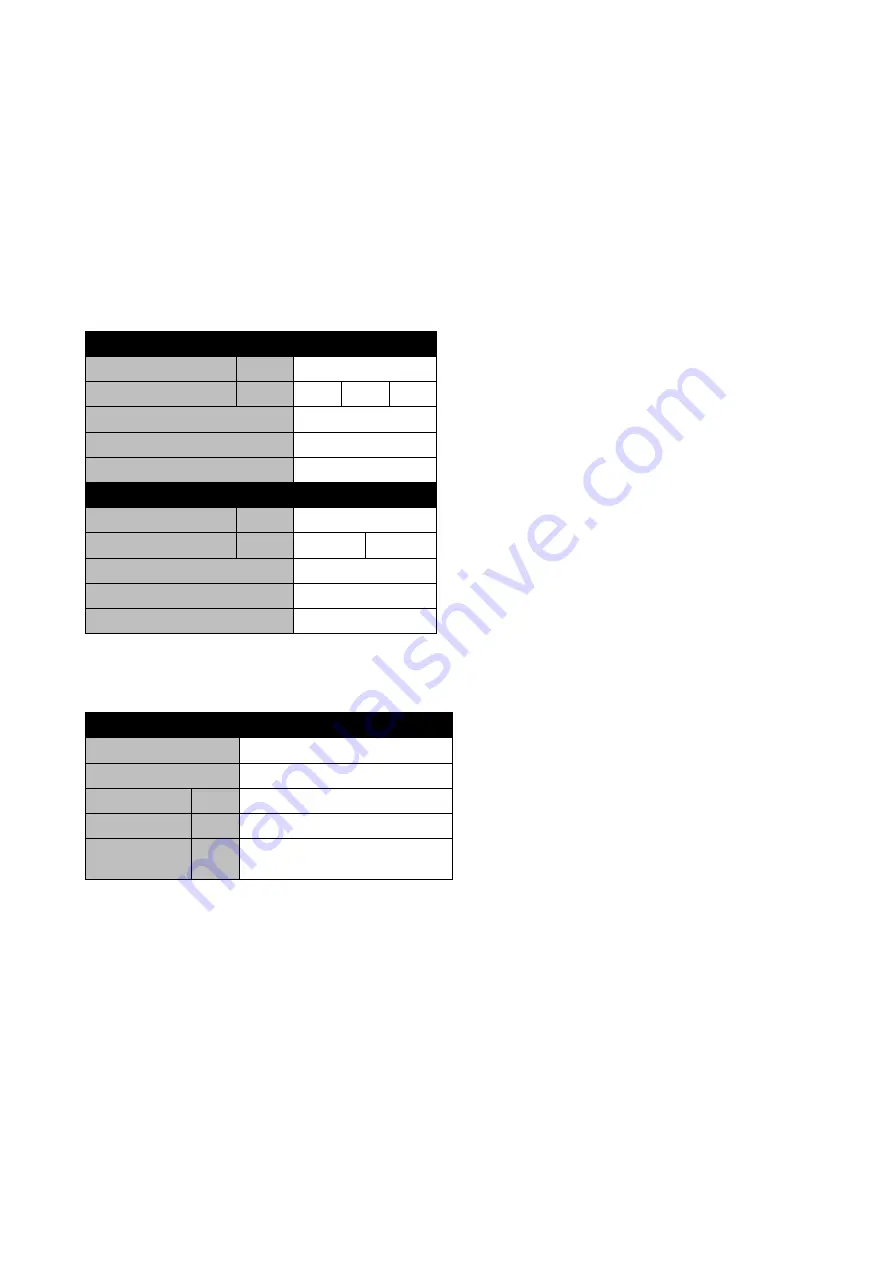
D-EIMHP01501-22_00EN
4/20
1. INTRODUCTION
The Daikin
EWWQ-KC
packaged water-cooled water chillers are designed for indoor installation and used for cooling and/or
heating applications. The units are available in 7 standard sizes with nominal cooling capacities ranging from 14 to 64 kW.
The
EWWQ
units can be combined with Daikin fan coil units or air handling units for air conditioning purposes. They can also
be used for supplying chilled water for process cooling.
The present installation manual describes the procedures for unpacking, installing, and connecting the
EWWQ
units.
This appliance is intended to be used by expert or trained users in shops, in light industry and on farms, or for commercial
use by lay persons.
Sound pressure level is less than 70 dB(A).
Table 1- Technical specifications (1)
General
EWWQ
014
025
033
Dimensions
HxWxD
(mm)
600x600x600
Machine Weight
(kg)
120
170
175
Connections
Water inlet
G1
Water outlet
G1
General
EWWQ
049
064
Dimensions
HxWxD
(mm)
600x600x1200
Machine Weight
(kg)
310
340
Connections
Water inlet
G 1-1/2
Water outlet
G 1-1/2
Table 2- Electrical specifications (1)
General
EWWQ
014-064
Power supply
Phase
3N~
Frequency
(Hz)
50
Voltage
(V)
400
Voltage
tolerance
(%)
±10