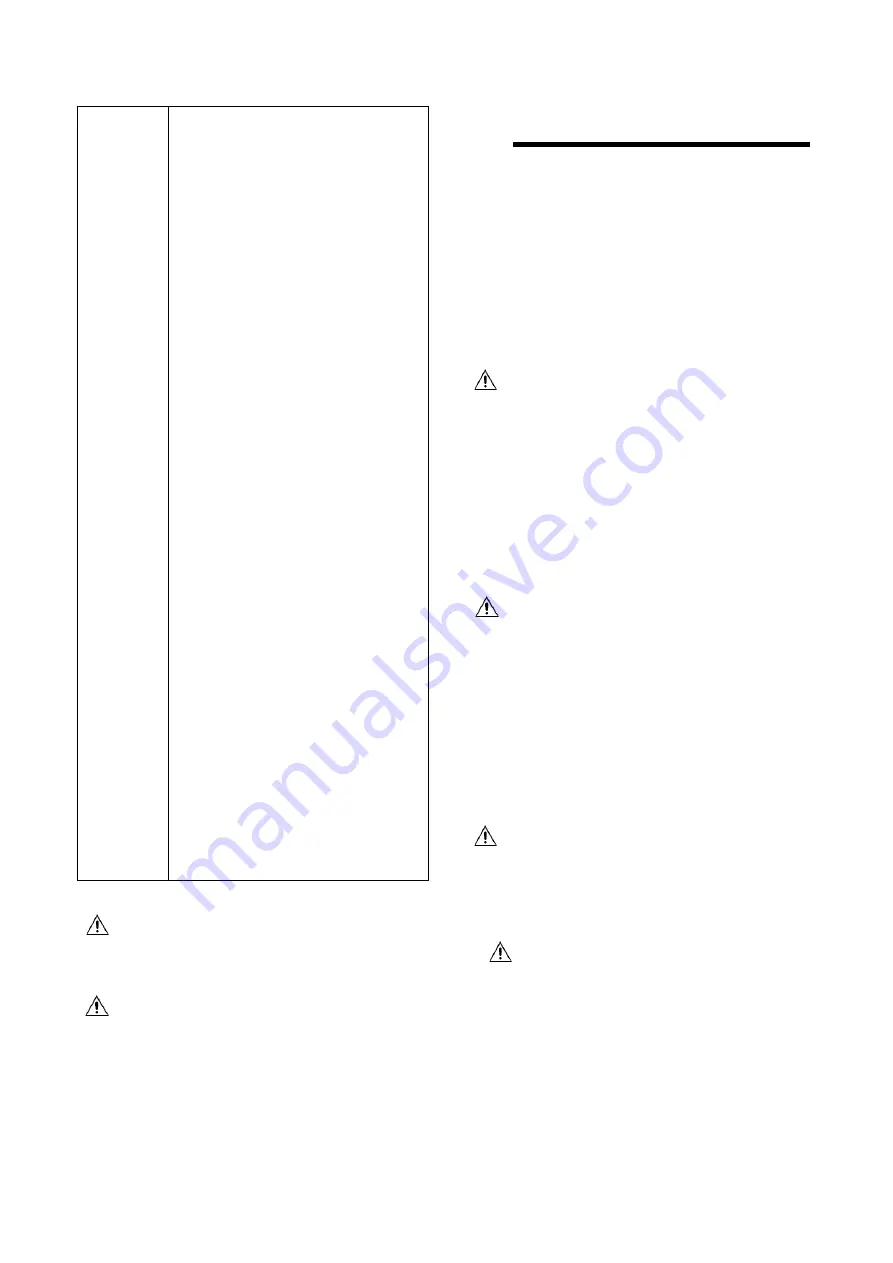
D-EIMWC01008-16EU - 11/20
refrigerating
system
The following precautions should be taken before
working on the refrigerant circuit:
— obtain permit for hot work (if required);
— ensure that no flammable materials are
stored in the work area and that no ignition
sources are present anywhere in the work
area;
— ensure that suitable fire extinguishing
equipment is available;
— ensure that the work area is
properly
ventilated
before working on the refrigerant
circuit or before welding, brazing or soldering
work;
— ensure that the leak detection equipment
being used is non-sparking, adequately
sealed or intrinsically safe;
— ensure that all maintenance staff have
been instructed.
The following procedure should be followed
before working on the refrigerant circuit:
1.
remove refrigerant (specify the residual
pressure);
2.
purge circuit with
inert gas
(e.g.
nitrogen);
3.
evacuate to a pressure of 0,3 (abs.) bar
(or 0,03 MPa);
4.
purge again with
inert gas
(e.g.
nitrogen);
5.
open the circuit.
The area should be checked with an appropriate
refrigerant detector prior to and during any hot work
to make the technician aware of a potentially
flammable atmosphere.
If compressors or compressor oils are to be
removed, it should be ensured that it has been
evacuated to an acceptable level to ensure that
there is no flammable refrigerant remaining within
the lubricant.
Only refrigerant recovery equipment designed
for use with flammable refrigerants should be
employed.
If the national rules or regulations permit the
refrigerant to be drained, this should be done safely,
using a hose, for example, through which the
refrigerant
is
discharged
into
the
outside
atmosphere in a safe area. It should be ensured
that
an
inflammable
explosive
refrigerant
concentration cannot occur in the vicinity of an
ignition source or penetrate into a building under
any circumstance.
In the case of refrigerating systems with an indirect
system, the heat-transfer fluid should be checked
for the possible presence of refrigerant.
After any repair work, the safety devices, for
example refrigerant detectors and mechanical
ventilation systems, should be checked and the
results recorded.
It should be ensured that any missing or illegible
label on components of the refrigerant circuit is
replaced.
Sources of ignition should not be used when
searching for a refrigerant leak.
This chiller, whether with R134a,R513A or R1234ze,
must be maintained by qualified technicians.
Before beginning any work on the system the
personnel shall assure that all security precautions
have been taken.
Always protect the operating personnel with
personal protective equipment appropriate for the
tasks to be performed. Common individual devices are:
Helmet, goggles, gloves, caps, safety shoes. Additional
individual and group protective equipment should be
adopted after an adequate analysis of the specific risks in
the area of relevance, according to the activities to be
performed.
10. EWLD J, EWLH AND EWLS
VERSIONS
CONNECTING THE REFRIGERANT CIRCUIT
This product is factory charged with N
2
The units are equipped with a refrigerant inlet
(discharge side) and a refrigerant outlet (liquid side) for
the connection to a remote condenser. This circuit must
be provided by a licensed technician and must comply
with all relevant European and national regulations.
10.1. Precautions when handling
piping
If air or dirt gets in the water circuit, problems may
occur. Therefore, always take into account the
following when connecting the water circuit:
1.
Use clean pipes only.
2.
Hold the pipe end downwards when removing
burrs.
3.
Cover the pipe end when inserting it through a
wall so that no dust and dirt enter.
The discharge and liquid line must be welded directly to the
remote condenser piping. For use of the correct pipe diameter
see table of Technical specifications.
Make sure the pipes are filled with N
2
during welding in
order to protect the pipes against soot.
There should be no blockage (stopvalve, solenoid
valve) between the remote condenser and the
provided liquid injection of the compressor.
10.2. Leak test and vacuum drying
The units were checked for leaks by the manufacturer.
After connection of the piping, a leak test must be performed
and the air in the refrigerant piping must be evacuated to a
value of 4 mbars absolute by means of a vacuum pumps.
Do not purge the air with refrigerants. Use a vacuum
pump to vacuum the installation.
10.3. Charging the unit
1. Perform an integral pre-start inspection like explained in
“
BEFORE STARTING
”.
Carefully perform all required procedures like
explained
in chapters from which is referred to in chapter
“BEFORE STARTING”
, but do not start the unit.
It is also necessary to read the operation manual delivered
with the unit. This will contribute to understand the operation
of the unit and its electronic controller.
Pre-charge of refrigerant without operation of the unit
2. Use the
1/4” SAE Flare stop valve on the filter drier to
pre-charge the unit with the complete calculated pre-
charge.
Do not operate the compressor for pre-charging,
Summary of Contents for EWWD J Series
Page 20: ...D EIMWC01006 11EU 20 20 ...