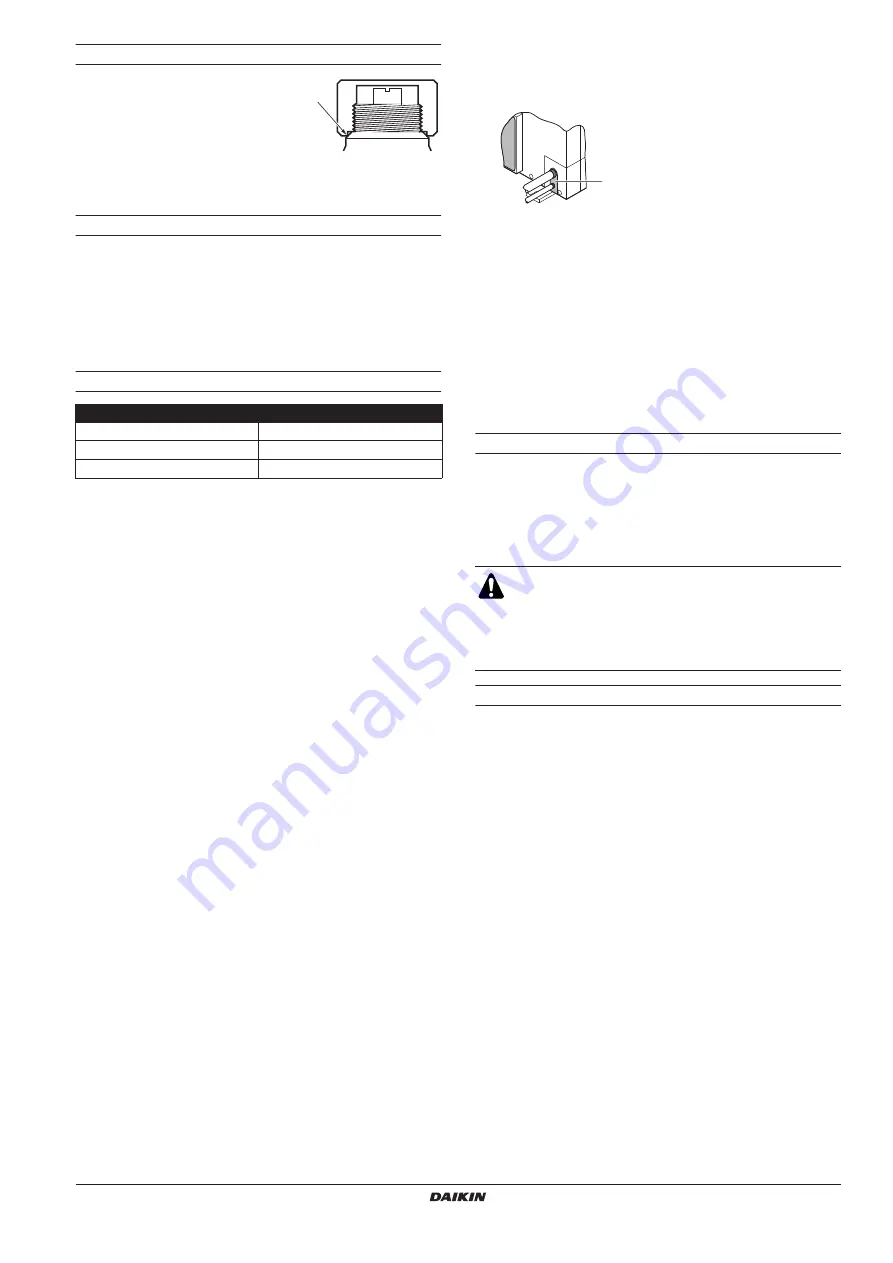
ERSQ+ERRQ011~Y1
Outdoor unit for air to water heat pump
4PW49635-1C
Installation manual
10
Cautions on handling the stop valve cover
■
The stop valve cover is sealed
where indicated by the arrow. Take
care not to damage it.
■
After handling the stop valve, make
sure to tighten the stop valve cover
securely. For the tightening torque,
refer to the table below.
■
Check for refrigerant leaks after tightening the stop valve cover.
Cautions on handling the service port
■
Always use a charge hose equipped with a valve depressor pin,
since the service port is a Schrader type valve.
■
After handling the service port, make sure to tighten the service
port cover securely. For the tightening torque, refer to the table
below.
■
Check for refrigerant leaks after tightening the service port
cover.
Tightening torques
7.
P
IPING
CONNECTION
WORK
7.1.
Refrigerant piping
■
Field pipes can be installed in four directions.
Figure -
Field pipes in four directions
When connecting the piping in the lateral direction (on the rear),
remove the piping cover (rear) in reference to
■
To install the connecting pipe to the unit in a downward direction,
make a knockout hole by penetrating the center area around the
knockout hole using a Ø6 mm drill.
.
■
Cutting out the two slits makes it possible to install as shown in
.
(Use a metal saw to cut out the slits.)
■
After knocking out the knock-out, it is recommended to apply
repair paint to the edge and the surrounding end surfaces to
prevent rusting.
7.2.
Preventing foreign objects from entering
Plug the pipe through-holes with putty or insulating material (field
supply) to stop up all gaps, as shown in the figure.
Insects or small animals entering the outdoor unit may cause a short
circuit in the electrical box.
7.3.
Leak test and vacuum drying
When all piping work is complete and the outdoor unit is connected to
the indoor unit, it is necessary to (a) check for any leakages in the
refrigerant piping and (b) to perform vacuum drying to remove all
moisture in the refrigerant piping.
If there is a possibility of moisture being present in the refrigerant
piping (for example, rainwater may have entered the piping), first
carry out the vacuum drying procedure below until all moisture has
been removed.
General guidelines
■
All piping inside the unit has been factory tested for leaks.
■
Use a 2-stage vacuum pump with a non-return valve which can
evacuate to a gauge pressure of –100.7 kPa (5 Torr absolute,
–755 mm Hg).
■
Connect the vacuum pump to
both
the service port of the gas
stop valve and the liquid stop valve to increase efficiency.
Setup
Item
Tightening torque (N•m)
Stop valve cover, liquid side
13.5~16.5
Stop valve cover, gas side
22.5~27.5
Service port cover
11.5~13.9
1
Drill
2
Center area around knockout hole
3
Knockout hole
4
Slit
5
Connecting pipe liquid (field supply)
6
Bottom frame
7
Front plate
8
Pipe outlet plate
9
Screw front plate
10
Pipe outlet plate screw
A
Forward
B
Backward
C
Sideways
D
Downward
1
Piping cover (rear)
1
Putty or insulating material (field
supply)
■
Do not purge the air with refrigerants. Use a vacuum
pump to evacuate the installation. No additional
refrigerant is provided for air purging.
■
Make sure that the gas stop valve and liquid stop
valve are firmly closed before performing the leak test
or vacuum drying.
1
Pressure reducing valve
2
Nitrogen
3
Siphon system
4
Vacuum pomp
5
Valve A
6
Gas line stop valve
7
Liquid line stop valve
8
Stop valve service port
9
Charge hose
1